Because they can be soluble in a variety of substances, emulsifiers are frequently used when immiscible components have to be combined. In order to achieve a suitable mixture, such as in food production, the pure, highly concentrated emulsifier is diluted beforehand to the working intensity. Above all, mixing installations for producing a suitable emulsifier have to have high metering accuracy in order to ensure an exact degree of dilution and prevent incorrect mixtures or fluctuations in individual batches.
Since this could not be guaranteed sufficiently by its former manual process, an international chemical company turned to the experts at LEWA GmbH. Its metering systems are equipped with flow meters that continually check the required degree of dilution of 20 percent; in the event of possible deviations, incorrect mixtures can be prevented thanks to the short settling time and the fast response of the control system. Use of the LEWA mixing modules also makes it possible to minimize logistics costs. By stocking the highly concentrated emulsifiers, which are only later diluted with water, the use of additional tankers delivering pre-diluted concentrate mixture, can be dispensed with.
ACCURACY AND FULFILLMENT OF SAFETY-RELATED STANDARDS
With regard to the right dosing, what is most important in emulsifier dilution is accuracy and fulfillment of the safety-related standards. As the additives are primarily used in the food industry, the dilution systems used must meet high operating requirements. This includes requirements that the modules must be robust and wear-proof to prevent leakages and – in the case of a hydraulically operated pump—any possible contamination of the emulsifier with lubricants. At the same time, however, the system has to function as precisely as possible so that the dilution levels requested by the customer can be adhered to without any deviations.
Conventional packed plunger pumps, which the chemical company had used to dilute emulsifiers, are not ideally suited for this purpose. In the first step here, the concentrated emulsifier fluid was directed into the tank manually. If the required volume was reached, the valve was closed and a second one was opened for the addition of the process water for dilution. Then, an agitator needed to be operated for half an hour to produce a homogeneous mixture.
This time-consuming, labor-intensive process negatively impacted the customer’s production efficiency, while also at times the correct mixture couldn’t be achieved. The human error rate is high due to factors like stress or distraction. If the pump is stopped too late, for example, the intensity of the emulsifier mixture can be changed substantially, leading to more water needing to be added in order to restore the concentration required originally. In turn, though, this means spending extra time.
HIGH METERING ACCURACY THANKS TO OPTIMIZED CONTROL
The large corporation, headquartered in Great Britain, therefore contacted pump manufacturer LEWA GmbH and commissioned the German company to construct a system for diluting a 70-percent emulsifier. After visiting the company’s location and developing a customized offer that took the specific spatial and logistical circumstances into consideration, the customer ultimately decided to purchase a LEWA metering system with ecodos diaphragm metering pumps, which were to be used to dilute the emulsifier to 20 percent.
The system consists of two pump groups: One pumps the emulsifier, the other the dilution water. A flow meter is located in both which monitors the current flow rate before the two fluids flow into a static mixer, where they are mixed. A third measuring instrument in the tank lastly shows the sum of both flow rates for control purposes, thus giving the customer redundant security—the sum of the partial flows must ultimately equal the measured value of the sensor. If the measured partial flows do not match the desired mixing ratio, the control integrated into the system automatically readjusts it. The operator only has to first specify the desired mixing ratio.
Due to the fact that the control technology of LEWA smart control only requires a short settling time, meaning it can counteract incorrect mixtures faster and in a more targeted manner than commercially available controllers—the transition times with imprecise mixture intensities are thus noticeably shorter. According to customer specification, the emulsifier mixture may not deviate from the required 20 percent by 1 percent. Thanks to the optimized control system, we can easily comply with this requirement.
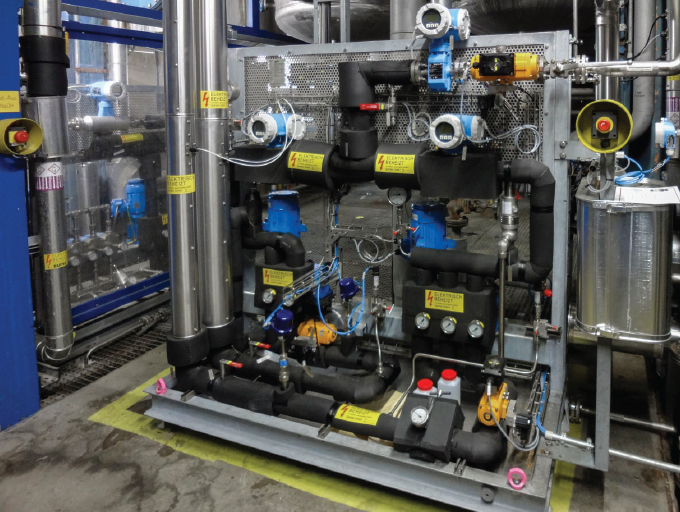
SPACE-SAVING STOCKKEEPING BY USING A METERING SYSTEM
Another specification from the British company was the use of the same sizes in the planning for the new metering as in a previous project system. If needed, it should be possible to exchange individual components between the mixing units quickly and easily in order to prevent production bottlenecks. Since diaphragms and valves for both systems are of the same type, this also simplifies procurement processes and the stocking of wear parts.
Furthermore, the LEWA dilution module ensures more efficient stockkeeping thanks to its space-saving concept. For example, if the customer wants to further process the emulsifier in three different concentrations, in a conventional method, this would require the use of three tankers to deliver the necessary quantities in the desired intensities of dilution. Thanks to the possibility of blending the emulsifier continuously over a wide concentration range in-house, only a single tanker filled with a high concentration is needed.
The dilution system, through which a 44,000 pounds mixing volume flows on a daily basis, has been in operation since summer 2018. The customer has ordered from us once again, and not without reason. In particular, the production efficiency was able to be increased significantly thanks to the faster, automated sequence. Based on this positive assessment, nothing is standing in the way of another co-operative effort.
FOR MORE INFORMATION
Siemens Digital Industries Software, a business unit of Siemens Digital Industries, is a leading global provider of software solutions to drive the digital transformation of industry, creating new opportunities for manufacturers to realize innovation. With headquarters in Plano, Texas, and over 140,000 customers worldwide, we work with companies of all sizes to transform the way ideas come to life, the way products are realized, and the way products and assets in operation are used and understood. For more information, visit www.sw.siemens.com.
Volker Kirschbauer is sales engineer at LEWA GmbH. LEWA GmbH is the world’s leading manufacturer of metering pumps and process diaphragm pumps as well as complete metering packages for process engineering. The Leonberg, Germany-based company developed into an international Group within a few decades and saw further improvement in its position on the world market as part of integration into Japanese NIKKISO Co. Ltd. in 2009. As a research and production-oriented company, LEWA develops technologies and provides solutions for the vast array of applications among its customers. Its products are used mainly in the oil and gas industry, in gas odorization, in refineries and petrochemicals, as well as in the production of plastics, detergents and cleaners. Additional application areas include the chemical industry, cosmetics industry, pharmaceuticals and biotechnology, food and beverage industry, and energy utilities. LEWA currently employs around 1,200 people and owns 14 subsidiaries around the world along with having 80 representatives and sales offices in more than 80 countries. For more information, visit www.lewa.com.
MODERN PUMPING TODAY, June 2019
Did you enjoy this article?
Subscribe to the FREE Digital Edition of Modern Pumping Today Magazine!
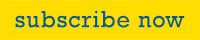