Thermoplastics are lightweight, averaging a weight of 1/16th of comparable metal materials.
The advantages of using thermoplastics in fluid handling applications are constantly being discovered. Over the last decade, there has been a dramatic increase in the application of thermoplastic valves and piping systems in areas where metal valves and piping were thought to be the only solution. Even the most corrosion resistant metals are still susceptible to galvanic and electrolytic corrosion, resulting in scale build-up, which reduces flow rates and increases pressure drop. Most importantly plastic will not rust!
Plastic valves and piping systems are offered in a wide assortment of materials and sizes. Each material has unique and specific mechanical properties. These diverse properties allow plastic to become the preferred system for many applications that range from the transport of aggressive chemicals to the distribution of ultra-pure water. Because each material has its own unique properties, understanding them becomes vital to the successful design, installation, and operation of a system.
Understanding the benefits and limitations of both advanced thermoplastics and metals is essential to making an informed choice in valve and piping materials.
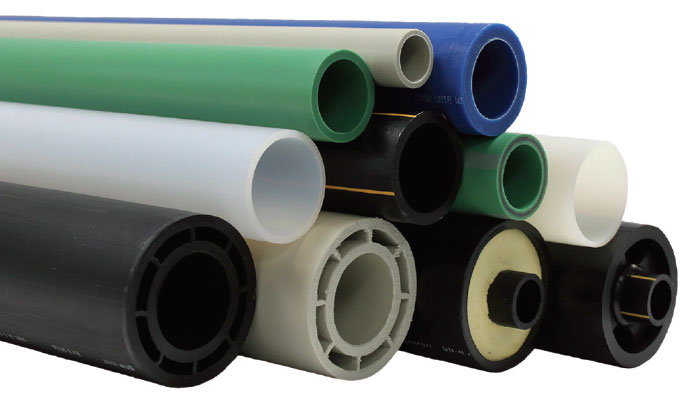
Plastic valves and piping systems are offered in a wide assortment of materials and sizes.
THE BENEFITS OF THERMOPLASTICS
Thermoplastics present many benefits across a range of industry areas. They are dielectric and exhibit low thermal conductivity. Thermoplastics are also smoother than metal for better flow rates and less energy required to move fluids—plus they are made to last longer than metal, even when in contact with corrosive liquids. Furthermore, unlike their metal counterparts, they are pure, so they do not contaminate the fluids they transport.
Additionally, thermoplastics are chemically resistant and corrosion resistant, much more so than metals, which is why thermoplastics are favored by the EPA. They are also lightweight, averaging a weight of 1/16th of comparable metal materials and are lower in total material and installation costs than conventional metal systems.
Overall, thermoplastics are more efficient than metals, especially in operational efficiencies including chemical inertness, resistance to permeation and impurity absorption, abrasion and freeze resistance—and because of their lightness in weight, good maneuverability, and compact size, they are also easier to install than metals,
Thermoplastic valves and pipe can handle many different temperatures and pressures and can outperform metal with respect to corrosion, abrasion and freeze resistance, and provide lower installed cost. Thermoplastic valves and pipe are application-tested having been installed in a wide array of industrial and commercial applications. For process lines, from wet chlorine, plating solutions, and acidic waste to demineralized water, thermoplastic valves and piping materials are your best solution.
Knowing the compatibility of the process media with the valve materials of construction, which include body, seat, seals, gaskets, diaphragms, discs, plugs, balls, packings, and trims—non-wetted as well as wetted parts—impacts the valve’s life and performance and contributes to its overall cost. Designing a system made of thermoplastic materials differs considerably from that of metallic materials.
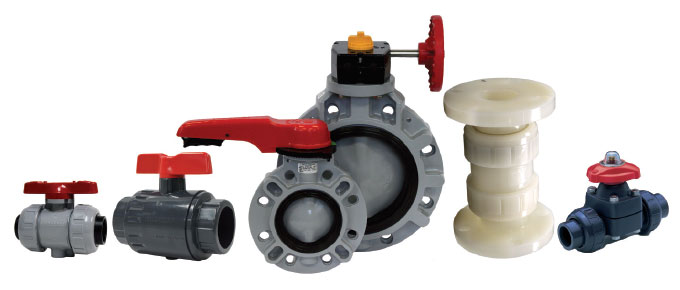
THE PLASTIC ADVANTAGE
For pipe, fittings, and valves, thermoplastic materials offer superior corrosion resistance, lighter weight, simple installation, and a more cost-effective alternative.
Corrosion Resistance
Plastics are non-conductive and are therefore immune to galvanic or electrolytic erosion. Because plastics are corrosion resistant, pipe can be buried in acidic, alkaline, wet, or dry soils without requiring a protective coating. In addition, cathodic protection devices are not required.
Chemical Compatibility
Impervious to many chemicals, thermoplastics are gaining an ever-increasing acceptance and preference in a large variety of applications. Additionally, the variety of materials available allow a wide range of chemical solutions to be handled successfully with plastic piping.
Thermal Conductance
All plastic piping materials have low thermal conductance properties. This feature maintains more uniform temperatures when transporting fluids in plastic than in metal piping. Low thermal conductivity of the plastic piping wall may eliminate or greatly reduce the need for pipe insulation to control sweating.
Low Friction Loss
Because the interior surface of plastic piping is generally very smooth, less power may be required to transmit fluids compared to other piping systems. Furthermore, the excellent corrosion resistance of plastics means that the low friction loss characteristic will not change over time.
Long-term Performance
Due to the relative chemical inertness and the minimal effects of internal and external corrosion, there is very little change in plastic piping’s physical characteristics over the decades. Examinations of pipe samples taken from some systems have shown no measurable degradation after tweny-five years of use.
Light Weight
Many plastic piping systems are about one-sixth the weight of steel piping. This lends to lower costs in many ways: lower freight charges, less manpower, simpler hoisting, and rigging equipment, etc. This characteristic has allowed unique, cost-effective installation procedures in several applications.
Variety of Joining Methods
Plastic piping can be joined by numerous methods. Each material has several different joining methods. The following incorporates some of the most common joining methods:
- Socket fusion
- Butt fusion
- Electrofusion
- Hot air
The various joining methods allow plastic piping to be easily adapted to most field conditions.
Nontoxic
Plastic valves and piping systems have been approved for potable water applications, and certain systems are recognized by the FDA as appropriate material to be in contact with food stuff.
As evidence, all plastic potable water-piping materials and products are tested and listed for compliance to NSF/ANSI Standard 61. All ASTM and AWWA standards for plastic pressure piping that could be used for potable water contain a provision whereby the regulatory authority or user can require product that has been tested and found to be in conformance with NSF/ANSI Standard 61–Drinking Water System Components–Health Effects. When plastic pipe or fittings are NSF/ANSI Standard 14 listed, and have the NSF-pw (potable water) mark, they also meet the NSF/ANSI Standard 61 requirements. The NSF-pw mark certifies to installers, users, and regulators that the product meets the requirements of NSF/ANSI Standard 14 for performance and the NSF/ANSI Standard 61 for health effects.
Biological Resistance
To date, there are no documented reports of any fungi, bacteria, or termite attacks on any plastic piping system. In fact, because of its inertness, plastic piping is the preferred material in deionized and other high purity water applications.
Abrasion Resistance
Plastic piping materials provide excellent service in handling slurries such as fly ash, bottom ash, and other abrasive solutions. The material toughness and the smooth inner-bore of plastic piping make it ideal for applications where abrasion resistance is needed.
Low Maintenance
A properly designed and installed plastic piping system requires very little maintenance because there is no rust, pitting, or scaling to contend with. The interior and exterior piping surfaces are not subject to galvanic corrosion or electrolysis. In buried applications, the plastic piping is not generally affected by chemically aggressive soil.
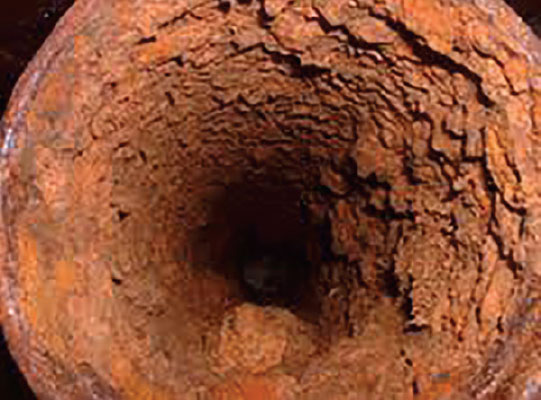
Even the most corrosion resistant metals are still susceptible to galvanic and electrolytic corrosion, resulting in scale build-up, which reduces flow rates and increases pressure drop.
Applications where thermoplastics are used
- Chemical processing
- Petrochemical
- Mining
- Pulp and paper
- Plating
- Pharmaceutical
- Food
- Semiconductor processing
- Municipal and industrial water
- Wastewater treatment
- Aquariums
- Landfill recovery
- Ultra-pure water
- Theme parks
- Cruise ship construction
- Solar panel manufacturing
- Ethanol production
- Railroad yard switching systems
Corrosive chemicals that thermoplastics can transport safely*
- Sulfuric acid
- Hydrofluoric acid
- Nitric acid
- Oxidizing chemicals
- Caustics
- Solvents
- Halogen
*Note: Please consult with the valve or pipe manufacturer’s chemical resistance guide before selecting the appropriate material for your application. Temperature, pressure, and chemical concentration are important factors to consider.
A LOOK AHEAD
In next month’s conclusion, we’ll take a deeper dive into the benefits of these materials. If you find yourself having corrosion problems with metal valves or pipes, plastics is your answer.
ABOUT THE AUTHOR
Jeffrey Baker is marketing and catalog sales manager for Asahi/America Inc. in Lawrence, Massachusetts. Baker has more than fifteen years’ experience promoting the benefits of thermoplastics as an alternative to metal for fluid flow applications and can be reached at jbaker@asahi-america.com. For more information, visit www.asahi-america.com.
_______________________________________________________
MODERN PUMPING TODAY, August 2018
Did you enjoy this article?
Subscribe to the FREE Digital Edition of Modern Pumping Today Magazine!
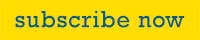