Pumps 2000 is the only diaphragm pump in the world designed for mining conditions at the request of the Australian mining industry due to the significant costs associated with using other brands, neck and back injuries, harmful emissions and skin allergies from lubrication, indirect costs to machinery from a wet mine due to ineffective and unreliable dewatering pumps, and high energy costs. Benefits and savings result from a significant reduction in pump maintenance and replacement pump costs, reduced energy costs, and lower indirect costs due to a drier mine.
FACING HARSH CONDITIONS HEAD ON
Mount Isa Mines in Queensland, Australia, needed reliability and toughness in their pumps, and they had a lot of them. Initially using over 1,000 pumps and spending millions of dollars in pump maintenance costs including replacing hundreds of pumps per year, the mine tested various brands and chose Pumps 2000. The savings from a reduction in pump maintenance costs is astronomical and the mines use fewer pumps resulting in a drier mine. They have been able to operate with close to half of the previous fleet and reduce their overall air usage by nearly 35 percent. In addition, they benefit from a reduction in indirect costs such as vehicle maintenance and work related injuries due to a drier mine.
Not only does the mine save on energy costs from using fewer pumps, each pump uses significantly less air so they can run more pumps on less air. Also, less air is available the farther away the pump is from the compressor so they can pump more volume on less air (cfm’s).
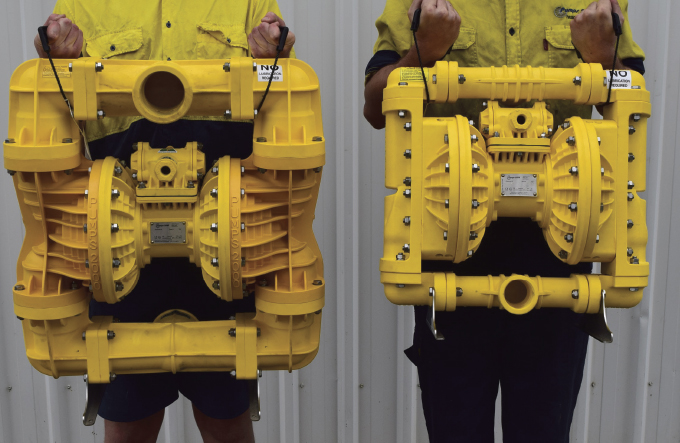
INNOVATION THAT CREATES RESULTS
The Australia mining board requested that our founder, Joe Santa, create a new diaphragm pump that would be lighter to reduce manual handling injuries and one specifically designed for mining conditions so it would hold up longer to dirty air and particulate laden liquids and slurry more effectively ultimately creating a drier mine and lowering indirect costs such as vehicle maintenance. He was well known as a consultant for setting up mines and developing equipment to solve problems in various industries, in particular mining from revolutionizing roof bolts with the use of time released resins to handheld drills.
The competitor’s units were unreliably lasting three or four weeks on average before requiring replacement parts and were eventually replaced after approximately one year because they could no longer be repaired. To combat the issues others in its sector were having and to offer the industry the most efficiently designed and running pumps, it developed and patented a system to eliminate the issues being reported.
Our unique combination of in-house R & D and manufacturing enables us to offer pumps which are technically superior and of significantly higher quality than those offered by the competition. Pumps 2000 pumps are made of engineered plastics. Several patented features make it possible to offer market-leading low life cycle cost and energy savings while delivering outstanding performance in the harshest environments.
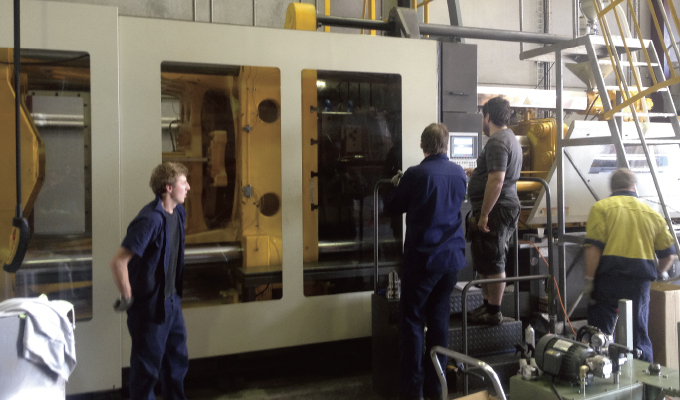
THE WORLD’S FIRST HIGH VOLUME DIAPHRAGM PUMPS
Pumps 2000 offers a complete range of pneumatic diaphragm pumps from 1/2 to 3-inch in our portable range and recently introduced the world’s first 3- and 4-inch High Volume pumps. The 3-inch High Volume ball valve pump has a flow rate to 417 gallons per minute. The 4-inch HV slurry pump has a flow rate of 540 gallons per minute and is ideal for pumping slurry at high volume. The slurry pumps are capable of passing large solids (3/4-inch with 1-inch pump, 1.5-inch with a 2-inch pump, and 3.5-inch with a 4-inch pump).
We also offer our two-stage pumps which are currently available in the 1.5-, 2-, or 3-inch portable models. A double-stage pump will produce lower flow than a single stage until a head pressure of about 50 psi, above this it will out-perform a single stage pump. Another application is low air pressure (doubling discharge pressure of the available air pressure).
Run by an air motor that is less sensitive and more resistant to wear from dirty air, non-freezing and kept smoothly running without any lubrication, Pumps 2000 was also the first lubrication-free design.
PERFORMANCE MATTERS
The company also highlights its performance attributes, including low air consumption (maximum of only 80 cfm for a 2-inch slurry valve pump, 85 cfm for a 2-inch ball valve pump and only 90 cfm for a 3-inch portable ball valve pump.
A lighter weight aids in the prevention of manual handling injuries with weights from 9 to 62 pounds in the portable range, the 3-inch portable pump is the only true portable 3-inch in the world weighing only 62 pounds.
Pumps 2000 are impact resistant, and designed and tested for mining to reduce damage to pumps. They can handle the impact of their own weight due to reinforcement from ribbing and gussets or supports, used in bridge design and airplane construction. The light weight also reduces damage because they can be moved by hand or hung up very easily.
All Pumps 2000 pumps are ATEX M2 Certified and our (FRAS) fire retardant anti-static conductive plastic carrying an Atex M1 rating is also a proprietary feature of the unit, so use in more explosive situations is not an issue.
The high suction lift of Pumps 2000 allows for more efficient usage over time while designed to be maintenance-free. The supersuction ability is due to the unit’s patented double hinged diaphragms, long stroke, and patented self-cleaning slurry valves.
The spare parts are the same for various models, including the high volume pumps, so you have fewer parts to keep on hand and versatility of parts for multiple types. The material design is not only a lighter alternative, but also one that resists deterioration even in low-pH locations. It was the very first plastic pump ever made.
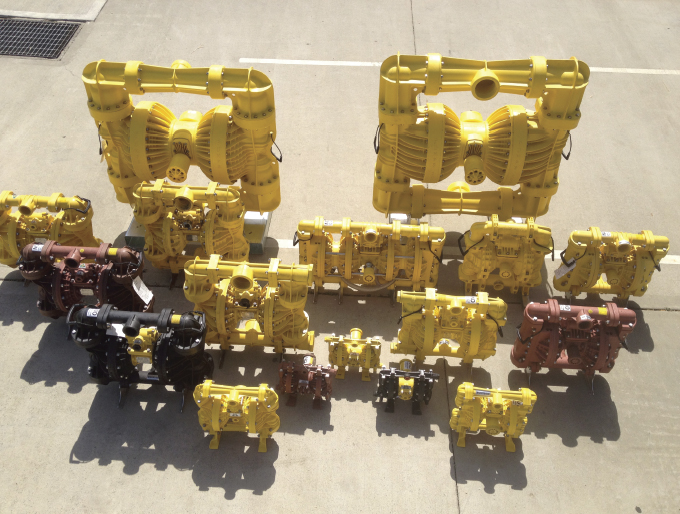
LONG LIFE AND A RANGE OF APPLICATIONS
Historically, diaphragm pumps have delivered a similar design and have been viewed as a commodity, both details that the company sought to change in its design and research. Other diaphragm pumps are difficult to differentiate from one another.
The need for tough, corrosion resistant, solids handling diaphragm pumps that provide greater capabilities, reliable performance, lower air consumption, low noise levels, and light weight has led to Pumps 2000 finding users in automotive, ceramics, chemical, coatings, construction, food processing, marine, oil and gas, pharma/personal, pulp and paper, wastewater, and more.
A long life and efficiency edge are two benefits of the Pumps 2000 product. There is no end of life for Pumps 2000 so it can always be repaired. There are fewer wear parts that can be replaced more easily. The Pumps 2000 design, on average, lasts years with no end of life and allows for the same work to be done with fewer units.
Based on feedback from operators, we believe that our design will reduce the amount of money spent on pumps yearly, lower overall maintenance costs, and increase productivity. We can offer each company that uses the Pumps 2000 design significant cost savings as a result of the superior design features and benefits. A number of other products are currently under development.
FOR MORE INFORMATION
Pumps 2000 provides products and solutions globally. Today, its pumps continue to be used in coal and hard-rock mining, as well as in general industry, marine, building and construction, food processing, chemicals, and pollution control applications. For more information, visit www.pumps2000.com or www.pumps2000america.com for North and South America.
MODERN PUMPING TODAY, May 2019
Did you enjoy this article?
Subscribe to the FREE Digital Edition of Modern Pumping Today Magazine!
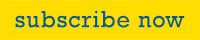