Dan Biby learned it all the hard way. An ordeal concerning several inverter-controlled pump motors with bearing damage made him a believer in the need for shaft grounding.
KILLER SHAFT VOLTAGES
Although destructive currents can occur in any motor, they are more common in motors controlled by inverters, also known as variable frequency drives (VFDs). VFDs can save 30 percent or more in energy costs, but they induce motor-shaft voltages that damage bearings. In fact, the cost of repairing or replacing failed motor bearings can wipe out any savings that a VFD yields and severely diminish the reliability of an entire system. Contractors and consulting-specifying engineers (CSEs) end up with unhappy customers, who soon discover that most warranties do not cover electrical bearing damage. This typically leads to finger pointing and the CSE and end user getting stuck with repair costs.
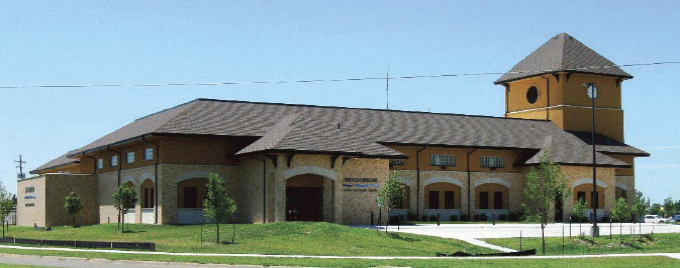
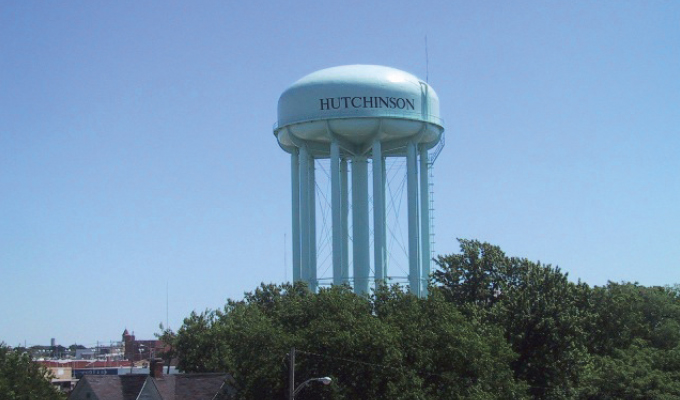
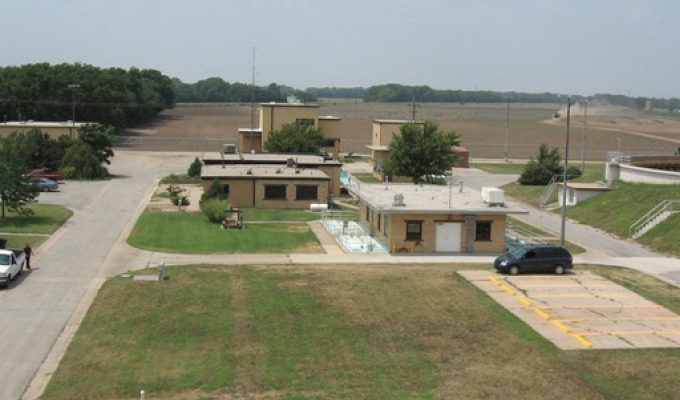
CASE IN POINT
Electrical engineer Dan Biby of Professional Engineering Consultants (PEC), Wichita, Kansas, helped design the new Reverse Osmosis Water Treatment Center for the city of Hutchinson, Kansas. With the capacity to pump 10 million gallons of drinking water daily, the plant is the solution to a groundwater contamination problem. Pumps lift contaminated water from beneath an industrial area and remove most of its volatile organic compounds (VOCs) through reverse osmosis and aeration. The water is then diluted with uncontaminated water from wells across town before being pumped to the city’s supply towers. All of the pump motors are controlled by VFDs that provide adjustability in flow rate and pressure.
Within two months of the plant’s completion, one of its high-service, 250 horsepower vertical pump motors was making the telltale whine of fluted bearings, and Biby soon found himself in charge of a remediation project that would last more than two years. “The motor manufacturer replaced the bearings on that first motor,” Biby recalls. “But when we soon had the same problem with the rest of the motors, the manufacturer concluded it wasn’t a bearing problem.”
Biby shipped some motors to a repair shop, but when they were re-installed, the noise began again. The repairs had been inadequate, and Biby recouped some of the cost. Then he tried Independent Electric Machinery Company (IEMCO), a Kansas City motor repair shop.
“We had never experienced this problem at this magnitude,” Biby continues. “Finding out what was causing it was exhausting, but Scott Wilkins’ team at IEMCO was a lot of help. Once we concluded that drive-induced shaft voltage was the culprit, we shipped the motors to IEMCO for repair.”
A PROVEN SOLUTION
IEMCO had developed the Vertical Motor Solution, a virtually foolproof process to prevent electrical bearing damage caused by stray shaft currents in vertical hollow-shaft motors. And for six years, Scott Wilkins, the company’s manager of motor shop operations, had overseen the reconditioning of hundreds of vertical pump motors, none of which had experienced repeat bearing failure.
IEMCO usually works on motors with failed bearings. After replacing the pitted bearings, his team installs a shaft grounding ring next to the motor’s guide (lower) bearing and, using proprietary techniques, applies ceramic insulation to the carrier that holds the thrust (upper) bearing in place at the motor’s drive end. For medium-voltage motors, Wilkins uses the larger AEGIS® PRO grounding ring, designed for motor shafts to 30-inch in diameter.
Coordinating the remediation with Biby was Don Koci, superintendent of water treatment systems for the city of Hutchinson. To keep the water plant up and running, they shut down and shipped only one or two motors at a time. An IEMCO technician took shaft voltage readings for each motor after the motor was repaired, to confirm that voltages were below a level that could damage bearings.
“As far as I’m concerned, IEMCO is the best around,” says Biby. “I don’t think there are very many motor shops with their level of experience installing AEGIS rings on these motors. And it is one of a very few motor repair shops that provides a warranty on the bearings against VFD-induced bearing damage for the life of the motor. They obviously know their stuff.”
After the first ten damaged motors had been successfully reconditioned, Koci sent the plant’s remaining seven pump motors to IEMCO for preventive maintenance, at the city’s expense. Four were horizontal pump motors, in which IEMCO installed an AEGIS ring at the nondrive end and ceramic-coated bearings at the drive end. By the end of 2011, all seventeen of the plant’s pump motors were protected from electrical bearing damage. Today, they are all still running without any problems.
HINDSIGHT IS 20/20
Biby is glad to have the problems behind him. “We’ve learned a lot,” he notes, “and we have updated our motor specifications to include shaft grounding rings on all new motors that will be connected to VFDs. We insist that the shaft grounding devices be factory installed or installed by a reputable motor shop with expertise in their proper installation. We also specify that, if the devices are not factory installed, they should be tested by a third party to ensure no shaft currents are present. And lastly, we require a warranty against VFD-induced bearing damage or failure for the life of the motor.”
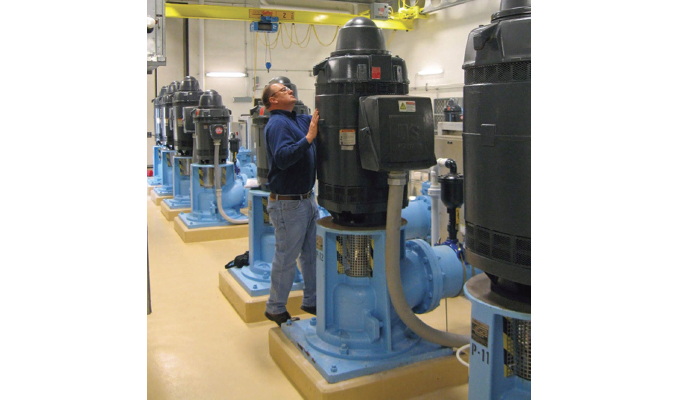
“We use the rings on all of our jobs to eliminate downtime, replacement, and installation costs. Installing rings can prevent these problems altogether. And the cost is insignificant when compared to total project cost.”
Realizing that motors could be built to withstand shaft currents in the first place, a few forward-looking motor manufacturers now offer models with the AEGIS Bearing Protection Ring factory installed, but retrofitting is still the most common way to prevent electrical bearing damage.
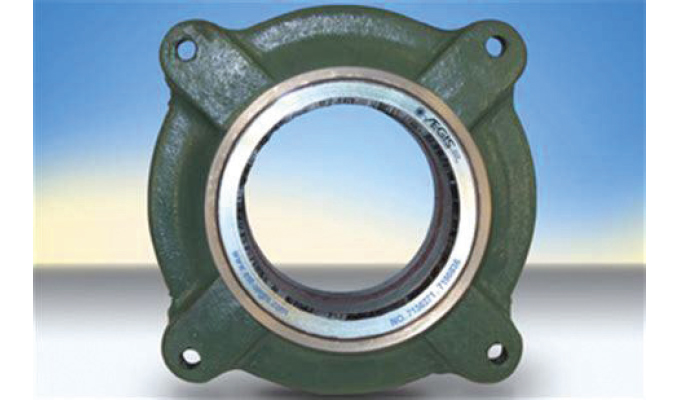
REVOLUTIONARY AEGIS NANOGAP TECHNOLOGY…
Key to the AEGIS Bearing Protection Ring’s effectiveness is its patented Nanogap Technology, which ensures superior contact/noncontact grounding protection for the normal service life of the motor’s bearings.
The AEGIS ring’s unique design includes proprietary conductive microfibers arranged in a continuous circle around the motor shaft, providing hundreds of thousands of voltage discharge contact points. These microfibers maintain electrical contact for the life of the bearing—even if physical contact is lost—through three distinct noncontact electron transfer processes that work simultaneously. These noncontact nanogap processes provide highly effective electron transfer—even in the presence of grease, oil, dust, and other contaminants—and are unaffected by motor speed. No other grounding product works with both contact and noncontact electron transfer, and no other product offers the long-term, maintenance-free performance of the AEGIS ring.
…AND A SYSTEMATIC APPROACH
For vertical hollow-shaft motors, IEMCO’s systematic approach requires the AEGIS ring to remove the voltage and a welltooled carrier to control the voltage until it is removed, so it doesn’t transfer to attached equipment.
Some carriers conduct electricity, but Wilkins is convinced that a carrier should be electrically isolated, disconnecting the motor from the pump shaft electrically though not mechanically. In addition to protecting the motor’s thrust bearing from electrical damage, this keeps shaft currents from jumping to the bearings of the pump itself, or to the bearings of a gearbox, tachometer, encoder, etc.
To apply the coating of ceramic, IEMCO uses a tightly controlled flame-spray welding procedure. Wilkins’s team also grinds each newly coated carrier to very tight tolerances. The finished carrier has a hardness of Rockwell 50C and provides a resistance of more than 1 gigaohm at 1000 volts—far better than the National Electrical Manufacturers Association (NEMA) standard of 1 megaohm at 500 volts.
IEMCO is not the first motor repair shop to attempt to VFD‑proof vertical hollow shaft motors, but it may be the first shop to do it right. Notes Wilkins, “After we’ve added the grounding ring and upgraded the carrier, the motor is truly inverter-ready.”
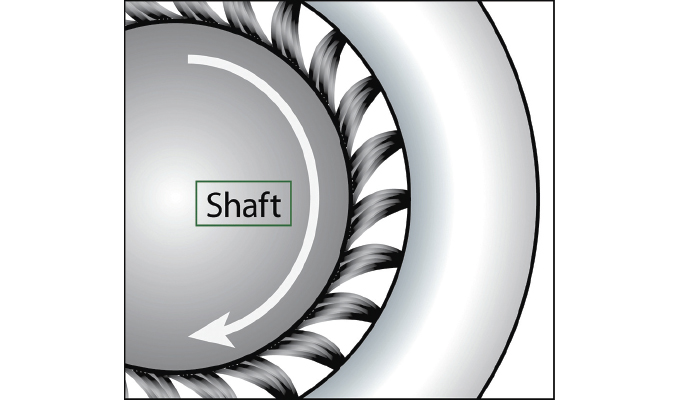
Matt Laufik is global sales manager for AEGIS, a leading brand in bearing protection. Electro Static Technology, the world leader in passive static control solutions, solves industry challenges posed by static charges in many of today’s sophisticated machines from printers and copiers to sensitive medical equipment, aerospace systems, and automated electronics manufacturing equipment, process machines, kiosks, and many other applications. For more information, visit www.est-aegis.com.
MODERN PUMPING TODAY, May 2019
Did you enjoy this article?
Subscribe to the FREE Digital Edition of Modern Pumping Today Magazine!
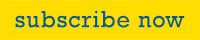