The piston-actuated round diaphragm pump was the standard in pumping higher pressure slurries and flows than other positive displacement pumps for many years. The need for an equally efficient design, but with a more hermetic ability and less parts was needed. Contamination throughout the diaphragm and even the associated air compressors and air/fluid combination valves became known with the old style round diaphragm design.
FIGHTING THE GOOD FIGHT AGAINST RUPTURES
In hose diaphragm pumping, each double hose that could fail would also have a secondary hose, one inside the other. If both hoses rupture, the fluid would only contaminate one cylinder head and not be pumped under pressure throughout the pump. This next generation of reciprocating pumping of heavy, solids-ladened and gaseous fluids and slurries would be conveyed by means of a double-walled hose that is both hermetic and isolated in nature.
During pump disrupt events, hose-diaphragm pump, bolstered by a complement of self-contained air-regulated pulsation dampeners, cone valve, ball valve, double ball valve and various other mechanically actuated check valves and valve monitoring equipment would be a better option than that of a round diaphragm pump which has had no significant design updates in years.
TAKING ON HIGHER PRESSURES
These older style round diaphragm pumps also contain more parts than that of a double hose diaphragm style pump, which makes total cost of ownership and maintenance both harder and more expensive. Unlike the peristaltic hose pump, the double hose-diaphragm pump can achieve higher flows and pressures like the old round style diaphragm pumps. This is possible because of balanced pumping where fluid surrounding the double hose acts upon the hose and provides hydraulic distortion like the human vein instead of a mechanical style actuation, which can damage or excessively wear the elastomer.
The double hose-diaphragm pump reaches peristalsis like a regular hose pump with greater pressure and flow ranges. Unlike the old style round diaphragm pump, the double hose diaphragm pump does not crimp and deform over time, nor allow pathways of fluid to get behind it during failure. The same elastomer rules for chemical compatibility and operational physics apply. The range of applications for the double hose-diaphragm pump would be mostly the same as any larger round diaphragm pump such as filter press, oil and gas applications, chemical, petrochemical, mining, wastewater, etc.
The design of hose diaphragm pumps is more likened to a human vein being elastically distorted or slightly compressed by its own lubricating fluid rather than a plunger pushing back and forth upon the fluid and a sloshing taking place in a valve and round diaphragm housing. The hose diaphragm produces a true hermetic, more linear path for the fluid to travel, thus achieving almost perfect peristalsis pumping. The natural flow of the product continues right through the pump itself.
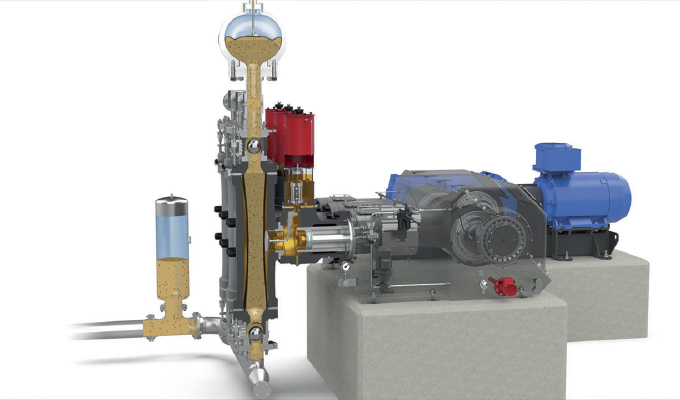
VERSATILITY BY DESIGN
The double hoses for these pumps are offered in several elastomers to match the fluid for chemical compatibility. They usually have a life span of about 10,000 hours as opposed to 6,000-8,000 hours with that round older style diaphragm pumps. Double ball valves are also common with this type of pump, which most round diaphragm pump manufacturers do not offer. No special valve extraction tools are required and component replacement is done with standard tools by one or two people.
These types of pumps can have a swing-away valve housing that allows one person the ability to change out a valve in under thirty minutes alone, again with no special tools. The monobloc style drive and crank offer a more compact and less horizontal profile with motors that can be placed vertically, which saves space. Since the fluid only comes into contact with the inside of the hose, the need for special construction materials for the pump housing are not usually necessary unless the pump is in a vaporous environment. This saves a significant amount of money or having to coat the inside of the pump. This adds to the life of the pump since the chances of a chemical attack on the housing exists.
These types of pumps have the ability to reverse the direction of the flow from inlet at the bottom (which is the usual configuration), to inlet at the top to allow thick and abnormally heavy viscous slurries to flow downward and pass through the pump better. These pumps average a life span of more than thirty years and, even with thick slurries. This represents a significant Capex benefit that last throughout the life of the pump.
FOR MORE INFORMATION
Chuck Martin is the president of Feluwa Pumps USA Inc. in Houston, Texas. He has over thirty-two years of experience in the pump industry in sales and management. Martin has worked both in manufacturing and distribution of pumps. Wherever abrasive, aggressive and toxic media are conveyed, the hermetically sealed, oscillating displacement pumps from Feluwa are used. Feluwa technology offers ideal pump systems to the customers for various applications, even for extreme operating temperatures and heterogeneous mixtures with high solids content. For more information, visit www.feluwa.com.
MODERN PUMPING TODAY, January 2024
Did you enjoy this article?
Subscribe to the FREE Digital Edition of Modern Pumping Today Magazine!