see Part 1 here
The benefits of simulating early as a part of the design process have been documented extensively. The cost of each engineering change increases with each step from concept to production. According to the U.S. Department of Defense (as reported by the Defense Acquisition University), while 20 percent of the actual cost has been accrued, 80 percent of the total life-cycle cost of U.S. defense projects were determined by the test phase. In other words, the cost of the product was locked in by decisions made during the early concept stages when little is known about the design. Also, the cost to fix defects rose as you proceed further down the process.
Although this data is from the defense sector, commercial entities likely face similar life-cycle costs. For electro-mechanical designs, simulating early and often is important. The right tools need to be made available at the right time so that the information can be accessed for early evaluation. This practice is called frontloading.
Interestingly, testing a design only at the prototype stage has been proven to be very costly. According to a report by Lifecycle Insights, failed prototypes lead to project milestones being missed, extra rounds of testing and having to work long hours among many other issues.
TIP #5
Select the right tool to frontload CFD, significantly shorten simulation time and achieve a more competitive design process.
THE MOVE FROM TRADITIONAL CFD
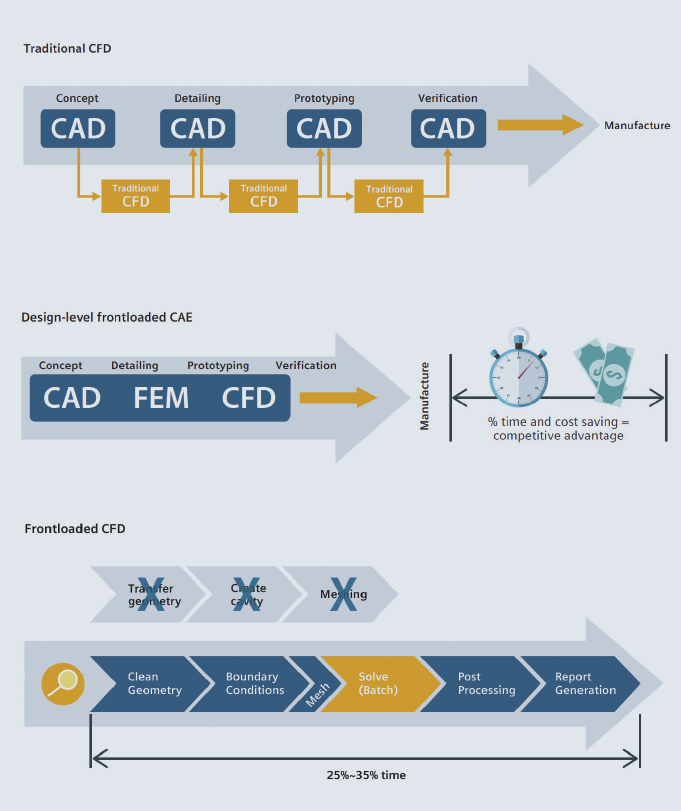
In last month’s introduction, we started an overview of traditional CFD methods. However, design-centric CFD solutions include built-in intelligent automation. They have been developed to be simply another supported feature inside the CAD system, alongside finite element method (FEM) analyses such as stress, to help frontload CFD.
Also frontloaded CFD solutions compress analysis time significantly—some organizations have reported a time compression of 75 percent. How is this possible? Frontloaded CFD solutions offer key proven technologies that greatly reduce model preparation and preprocessing, such as the following.
First, by being fully embedded in CAD, the software uses the same native geometry for analysis. Exporting data and healing it in preparation for analysis is no longer required. In addition, the software simply slots in – it does not require you to learn a new interface nor does it require a familiarity with the interface every time the software is used. CFD analysis is simply another functionality offered by the CAD package.
Also, in fluid-flow and heat-transfer analysis, we are interested in understanding what is happening in the negative space, the empty space. With traditional CFD, additional geometry has to be created to represent that cavity. Frontloaded CFD solutions are intelligent enough to recognize that the empty space is the fluid domain so that no time is wasted creating geometry to accommodate software. This step is completely unnecessary.
Finally, before analysis can begin, the model has to be meshed. With traditional CFD, the engineer has to be fully conversant in which algorithm best depicts the flow phenomenon being studied. Frontloaded CFD solutions have a fully automated mesher that will automatically generate the best possible mesh for the problem being set up. The software has built-in intelligence such as SmartCells that make it possible to use even coarse meshes without sacrificing accuracy.
The National Institute for Aviation Research has verified the time savings offered by frontloading comparing it with traditional methods. In short, by using the right tool to frontload CFD, you may be able to significantly shorten your simulation time and achieve a shorter, more competitive engineering design process.
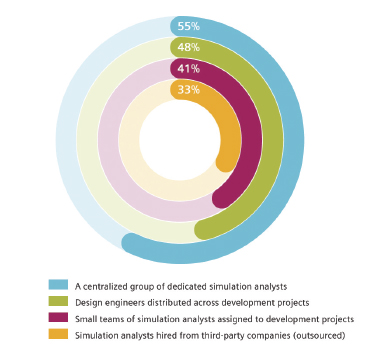
THE DESIGNER
Today’s typical designer is a mechanical engineer. During the course of their education most mechanical engineers have been exposed to the principles of CFD in one shape, form, or another. But most importantly, an engineer working on the design of any product is fully versed in the background of what he or she is designing. For example, a design engineer working on the design of automotive lighting got the job because they have a background in electronics design and is familiar with the basic properties and behavior of automotive lighting. They understand that electronics generate heat and the effect of excessive heat on performance. They understand that squeezing electronics into an enclosure will create a thermal problem. They understand that many electronic components are at their disposal to reduce the heat, including heatsinks. Even the use of different materials may create a different operating environment that may change the effect of heat.
In short, design engineers are more than capable of assessing the problem, checking multiple design variants to see which ideas are the most effective, testing them, and generating a solid design. In fact, industry research corroborates that design engineers are in fact conducting fluid simulation in great numbers.
TIP #6
Using the right tool, design engineers are more than capable of assessing a problem, checking design variants, and testing trends.
WHY IS SIMCENTER FLOEFD THE RIGHT SOLUTION?
Simcenter FLOEFD technology, first introduced to the market in 1991, has been used by thousands of engineers to frontload CFD in the design process. The award-winning Simcenter FLOEFD will not disturb or require modification of the workflow. Simcenter FLOEFD simply fits into the process without any disruption. It provides increased flexibility to test many design ideas in less time—when the R&D cost committed to the project is lower and fairly flexible. It helps the design team become more efficient at discarding suboptimal ideas sooner and lets the analyst team focus on solving more complex analysis problems and complete verification faster.
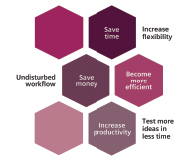
Proven Productivity Gains
Conducting analysis with Simcenter FLOEFD is significantly fast. The speed is a result of intelligent automation, use of the CAD environment, and ease-of-use. Simcenter FLOEFD is completely embedded in the most popular CAD programs. Despite its different interface for each CAD program, the experience remains the same. Designers have reported being able to use the software with less than eight hours of training, much less than traditional CFD programs which can require as long as twelve months training to use the software productively.
Because the engineer operates Simcenter FLOEFD in a native CAD environment and uses native geometry, data does not need to be transferred out of CAD and into Simcenter FLOEFD. The model is immediately available for analysis, thus saving time and effort. Wizards, plain engineering language, and extensive libraries further enhance the experience and allow the designer to setup models quickly and effortlessWly. Its automatic mesher lets the designer mesh the model with minimal intervention. In addition, the software automatically recognizes the fluid region.
Simcenter FLOEFD also makes it easy to analyze multiple variants of the design. The designer simply modifies the model in CAD, and Simcenter FLOEFD automatically attaches the previously set analysis information including boundary conditions and material properties to the new variant. Upon remeshing, the model can again be analyzed.
Speed is of the essence for enabling the engineer conduct analysis in a timely manner to keep up with the fast-moving world of design. Simcenter FLOEFD significantly saves time.
During a recent benchmark, design engineers at an aerospace company realized a 10x productivity enhancement with Simcenter FLOEFD compared to a traditional CFD package when simulating pressure loss in a complex shape channel. The traditional CFD tool required more time investment during the preprocessing stage, especially for model preparation, which included time for transferring the model out from the CAD package and then healing it. It also required significantly more time for mesh generation. During the solution phase, the traditional CFD tool needed significantly longer to solve the problem given the size of the mesh. Arguably, the solution time can be handled with brute force by throwing as many processors as possible at the problem. However, when comparing apples to apples (using the same hardware), Simcenter FLOEFD required less time to solve the same problem. When looking at the entire process, Simcenter FLOEFD required only four hours versus forty hours to complete the same task, with the same accuracy. Needless to say, the design team is now using Simcenter FLOEFD.
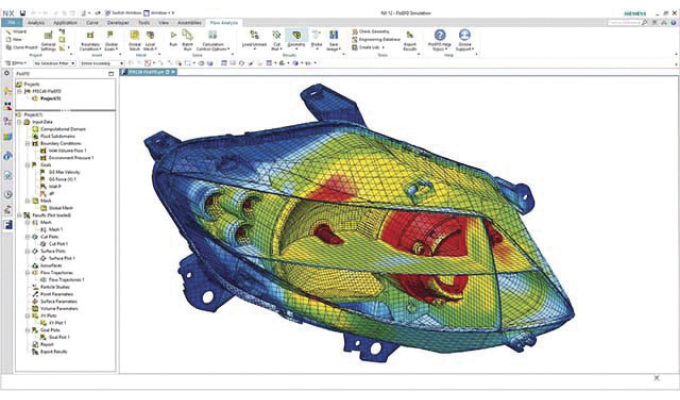
Proven Accuracy
Being fast is good but being fast and accurate is better. Simcenter FLOEFD technology has its roots in the Russian aerospace industry and has been in use since 1991. Its first validation was made in collaboration with the German Aerospace Centrum (DLR). It focused on the separation in a rocket nozzle and compared simulation results versus experiment, and the results proved that the technology was solid.
Since those early days, Simcenter FLOEFD technology has undergone a fair amount of scrutiny by leading aerospace and automotive organizations. Most recently the Society of Automotive Engineers of Japan (JSAE) published a blind benchmark of seven, leading, commercial-CFD, simulation-software programs to demonstrate the accuracy of each tool against validated test results from a wind tunnel. Simcenter FLOEFD again proved its accuracy in this nonpartisan benchmark.
Accurate and Fast
CFD simulation as an integral step during the design stage is no longer a luxury, it is a must. Companies that embrace that change prosper. Those who do not will continue to waste precious resources.
Can your company afford to be in the latter group?
FOR MORE INFORMATION
Siemens Digital Industries (DI) is an innovation leader in automation and digitalization. Closely collaborating with partners and customers, DI drives the digital transformation in the process and discrete industries. With its Digital Enterprise portfolio, DI provides companies of all sizes with an end-to-end set of products, solutions and services to integrate and digitalize the entire value chain. Optimized for the specific needs of each industry, DI’s unique portfolio supports customers to achieve greater productivity and flexibility. DI is constantly adding innovations to its portfolio to integrate cutting-edge future technologies. For more information, visit www.siemens.com/software.
MODERN PUMPING TODAY, September 2022
Did you enjoy this article?
Subscribe to the FREE Digital Edition of Modern Pumping Today Magazine!