In this concluding section of our three-part series on the upkeep of reverse osmosis (RO) systems, we’ll finish out with a detailed look at membrane fouling. Fouling doesn’t necessarily reduce RO membrane life if the RO is effectively cleaned. If the RO is allowed to foul too severely and cleaning is not effective, then the membrane will likely continue to lose performance.
CARTRIDGE FILTERS: A CLOSER LOOK
It is common to include a filter housing on the RO system inlet that contains 2.5-inch-diameter cartridge filters, whose pore size is nominally rated. The actual ability for removing smaller particles can vary greatly. Some (regardless of rating) only protect the RO against large particles that might get caught within the membrane flow channels or damage the high-pressure pump. These are inexpensive and may last weeks before an elevated pressure drop indicates the need for replacement. Tighter porosity filters that can remove more of the incoming suspended solids are more expensive and also require more frequent replacement. Therefore, the use of these tighter filters becomes more economically viable if the concentration of suspended solids in the water has been minimized by upstream treatment.
Suspended solids can often be effectively reduced to reasonable concentrations for the downstream RO system with just a multimedia filter. Its inclusion in the RO water system might be sufficient to prevent a high RO fouling rate that could result in unmanageable cleaning requirements. Multimedia filters contain granules of two or more different types or sizes of sand, crushed rock, or anthracite (a hard form of coal). Such a filter can be successful at removing most of the particles that make up the suspended solids if:
It is sized for a downward flow velocity approaching 2 feet per second.
It has a lower collection lateral system designed to obtain uniform flow distribution across the media when the filter is operated at low flow velocity, while also allowing the entry of a sufficient backwash flow rate for a 40 percent bed expansion.
The filter is backwashed before its previously removed smaller/fine particles are shed, which may occur before there is an appreciable buildup in filter pressure drop.
After backwashing, the filter is forward-rinsed at its service flow rate until its effluent quality is acceptable (such as based on effluent iron concentration, turbidity, or SDI).
The preceding points do not provide all the filter design requirements, but were chosen because these particular guidelines are often not followed (mostly because they would increase the filter’s cost). Some water sources may contain unusually high concentrations of fine particles. In these cases, it may be necessary to send the water through large reaction tanks intended to give the particles more time to coagulate into larger particles that can then be more easily filtered.
An inorganic chemical coagulant (never a cationic polymer) may be added to the water upstream of the tank to speed the coagulation process. The coagulant is most effective if it is first well-mixed with the suspended solids. If soluble metals (such as iron or manganese) are present in the water source, some percentage will be oxidized by allowing the water to contact atmospheric air in the tank, although this percentage is typically small. A chemical oxidizer such as chlorine (bleach) can be added to the water to oxidize the metals into their insoluble oxides (actually into their hydroxides when present in water) prior to coagulation.
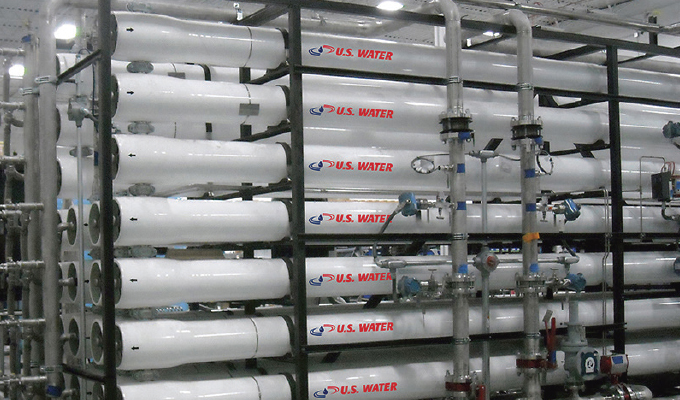
MEMBRANE FILTRATION
Membrane filtration is becoming more common in various applications, including pre-treatment for RO systems. It can often provide water that is more consistently low in its concentration of suspended solids than that provided by a pressurized multimedia filter. Therefore, these systems may be used as an alternative to multimedia filtration, or possibly downstream to further polish the water and minimize RO fouling.
The most common configuration is hollow-fiber technology. Fibers of an inert polymer are extruded with a hollow internal region, or lumen. The fibers may be relatively fine/small in diameter where the inlet water passes around the outside of the fibers, and through the fiber wall to the fiber lumen. It then moves toward one end of the module for collection.
Because the fibers are tightly packed, flow movement around them is not uniform. Feedwater particles will come out of suspension on the membrane surface as the water goes through the fiber. They are not concentrated within a passing stream as the particles mostly would be with spiral-wound RO, so there is no concentrate stream. The systems are simply operated at 100 percent recovery, except for the water losses from frequent backwashing with filtered water, resulting in an overall recovery of 90 to 95 percent.
There also are modules with larger fibers that use an inside-out service flow direction. The fatter fibers offer improved membrane surface flow characteristics for better distribution of the fouling solids, while the finer fibers offer the cost advantages of more membrane surface area in the modules.
The membrane filtration systems should be sized to keep the fiber pressure differential (transmembrane pressure, or TMP) relatively low to prevent compaction of solids against the fiber and into the fiber pore structure, and to reduce the potential for fiber breakage. This may mean sizing the fiber for a filtrate flux rate of 30 gallons per square foot per day or less.
The fiber modules are backwashed using the filtrate water at a frequency of roughly once every thirty minutes, again to try to keep the solids from compacting and to prevent particles from getting forced into the pores and subsurface structure. Some manufacturers reduce the backwash volume by knocking the solids free with compressed air.
Backwashing alone may not fully restore the original TMP, and a chemically enhanced backwashing may be required. If this fails to restore original performance, a circulated cleaning for an extended period of time may be needed.
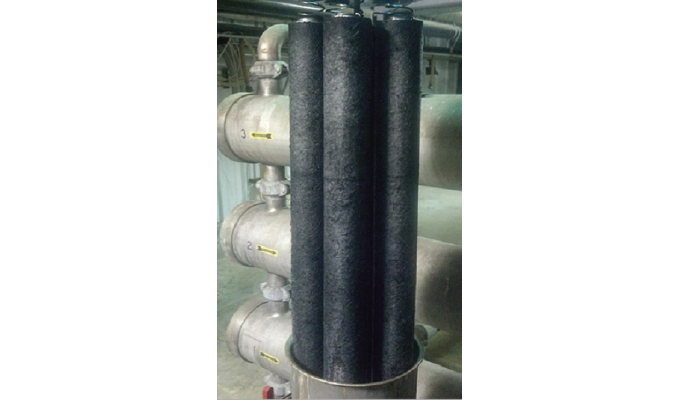
UPSTREAM PRIORITIES
It is not only feasible, but it is practical with larger RO systems to design chlorine destruction and scale inhibition systems with safeguards to prevent any problem with their operation from compromising the RO membrane life expectancy. For example, an oxidation-reduction potential (ORP) instrument can continuously monitor the RO inlet water for the presence of an excessive concentration of any oxidant, like chlorine. It can be interlocked with an alarm system to shut down the RO if its reading remains high for an appreciable period of time.
When relying on chemical injection systems, the RO membrane should be protected from both the absence of the injected chemical, as well as from an excess of that chemical. The inclusion of automatic isolation valves on the chemical injection lines located just prior to their points of injection into the water lines will prevent chemical dumping while the RO is shut down. This often occurs when compressible (which also means de-compressible) air collects over time within the injection line. The valve actuators should be programmed to close during the RO shutdown process prior to the water line pressure declining and in conjunction with the stoppage of the associated injection pump.
The operation of a chemical flow sensor located on each chemical injection line can be interlocked with an RO alarm and shutdown function. This feature can protect against faulty programming that results in negligible chemical being injected, while also protecting against an injection pump failure or failure to replenish the injection chemical.
While the 100 percent correct operation of the chlorine destruction and scale inhibition systems would be considered to be critical to the success of the RO system, it may not be practical to remove 100 percent of the suspended solids from the RO inlet water. It then becomes subjective as to whether to invest more capital into the upstream media filters or ultrafiltration system, versus planning to spend more operating money in the cleaning of the RO membrane elements as related to their increased rate of fouling due to a higher concentration of suspended solids in their inlet water. A higher rate of membrane fouling does not necessarily mean that the life of the membrane elements will be reduced, not if the RO system is successfully cleaned when needed, as based on the RO operating data.
U.S. Water, a subsidiary of ALLETE, Inc., provides options for environmentally friendly, safe, and cost-effective water management. As experts in water, they use their in-depth industry knowledge and experience to enhance system reliability, efficiency, and profitability. For more information, visit www.uswaterservices.com.
MODERN PUMPING TODAY, May 2019
Did you enjoy this article?
Subscribe to the FREE Digital Edition of Modern Pumping Today Magazine!
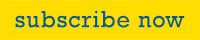