By Eric Sengheiser, Control Products Inc.
When we think of steam, perhaps an image comes to mind of the old steam train in a Western movie, hissing and clanking, as it rattles into some long-forgotten dusty town. This may even lead us to the misconception that steam is an outdated and unused technology. However, the use of steam for transporting and transferring thermal energy is more common today than many people realize. Steam is also used to do mechanical work in the generation of electrical power in nearly all large fossil-fueled and nuclear power plants and in industry for making everything from paper to potato chips to pharmaceuticals. In addition, steam is still commonly used for heat and hot water in many large city and college campus buildings, as well as providing humidification and sterilization in healthcare facilities. Steam is by nature non-toxic and sterile. And it is manageable and easy to distribute in a properly designed system, while possessing excellent and predictable heat transfer properties.
In its simplest form, today’s steam heating system consists of three major elements: a boiler, a distribution system for the steam and condensate return, and the heat exchange equipment (energy consumers). The distribution system itself includes many different components including the steam and condensate piping, steam traps, manual valves, control valves, condensate return pumps, and a boiler feed pump or deaerator. In the case of high-pressure steam systems, pressure reducing valves (PRVs), safety relief valves, and flash tanks are often needed as well. Of the many components in this system, one of the most critical is the condensate return pump. However, determining the optimal design of that pump requires system designers to consider several factors. Figure 1 shows the basic layout of the steam system.
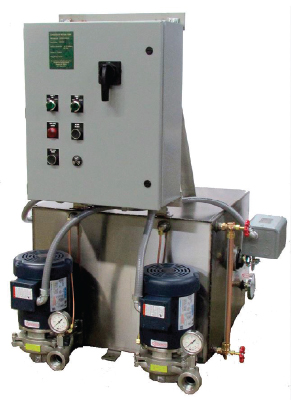
Image credit: Russell Pump & Engineering Inc.
TYPES OF CONDENSATE RETURN PUMPS
There are two basic types of condensate pumps used in steam systems today: electrically-driven and pressure-operated, with each having their own strengths and limitations.
A packaged electric condensate pump essentially consists of a condensate receiver tank (often vented to atmosphere), an electric centrifugal or turbine-style pump, and a float-activated switch. The electric pump is activated whenever the receiver fills with enough condensate to trip the float switch. Once the level in the receiver is suitably pumped down, the float switch senses this and deactivates the pump. Then, the cycle repeats.
Condensate pump packages are commonly offered with one (simplex) or two (duplex) pumps. Duplex pumps are controlled by an alternating float switch to even out usage of the two pumps and also offer the advantage of pump redundancy. Condensate receivers come in different configurations (rectangular or cylindrical, floor-mounted or elevated), various gallon capacities, and in several materials of construction including carbon steel, cast iron, and long-lasting stainless steel. Pumps can be end-suction or tank-mounted and are most often constructed with a cast iron housing and bronze impeller, with even longer life achieved through stainless steel componentry. A myriad of accessories is available, including a level sight glass for the receiver, thermometer, pump discharge pressure gauges, pump isolation valves, and a pre-wired electric control panel. Figure 2 is an example of a duplex electric condensate pump in all stainless-steel construction.
By comparison, pressure-operated condensate pumps (POCP) use no electrical energy for pumping, but instead operate on a two-cycle method of either filling up or pumping out of the pump housing using either steam or air as the motive gas to pump the condensate. The motive pressure for pumping is initiated by either a spring-activated/mechanical or electrical valve (this article focuses on the spring-activated mechanical type only). Figure 3 demonstrates the filling and pumping cycles of the pressure-operated pump with mechanical valves.
Pressure-operated pumps are often assembled as a “skid package,” consisting of a condensate receiver (again, often atmospheric), pressure-operated condensate pumps (POCPs), with interconnecting piping, isolation valves, and accessories. Packages are commonly offered in simplex and duplex configurations, although triplex and quadraplex variations are possible. Carbon steel, cast/ductile iron, or sometimes stainless steel are used for the condensate receiver, pump housings, and interconnecting piping, with stainless steel almost universally used for the spring-type pump mechanism internals.
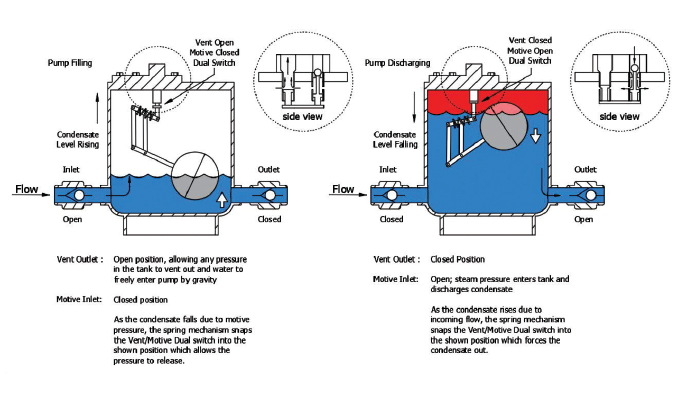
SIZING AND SELECTION
In the United States, steam and condensate flow rates are measured in terms of mass flow rate, in units of pounds-per-hour. Flow rates for electric condensate pumps are typically described in gallons per minute). An approximate conversion from pounds-per-hour condensate to gallons-per-minute is condensate flow (pounds-per-hour) ÷ 500 = condensate flow (gallons-per-minute).
Alternatively, some electric manufacturers rate their pump capacity using a steam heating term called square-feet EDR (equivalent direct radiation). To convert from pounds-per-hour to square-feet EDR, the equation is condensate flow (pounds-per-hour) × 4 = condensate flow (EDR).
In order to minimize pump short-cycling, note that most electric condensate pump manufacturers rate their pumps with a built-in safety factor of gallons-per-minute capacity that is 2 to 3 times the EDR or pounds-per-hour rating.
By contrast, sizing tables for pressure-operated pumps are shown directly in terms of pounds-per-hour. When determining the required head pressure of the pump, we start by calculating the back pressure and lift of the downstream system piping, just like any other pump application. Lift and back pressure for most electric condensate pumps is expressed in terms of feet of head, while the sizing tables of pressure-operated condensate pumps is shown in terms of psig of backpressure. An easy way to convert from feet of head to psig is by using the following formula: backpressure (psig) = lift (feet of water)/2.31.
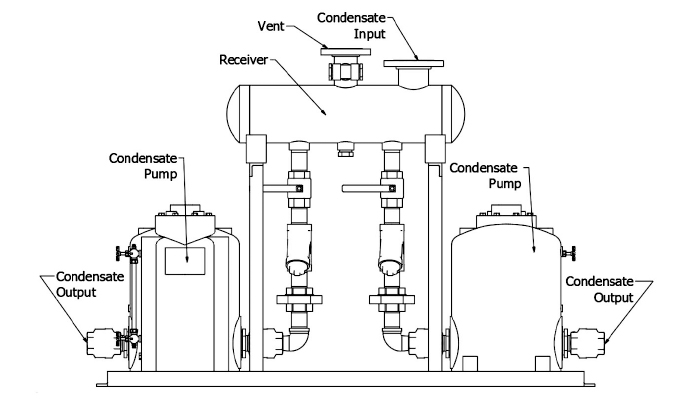
So how do we decide which pump is best for our application?
IMPORTANT CONSIDERATIONS DURING CONDENSATE PUMP SELECTION
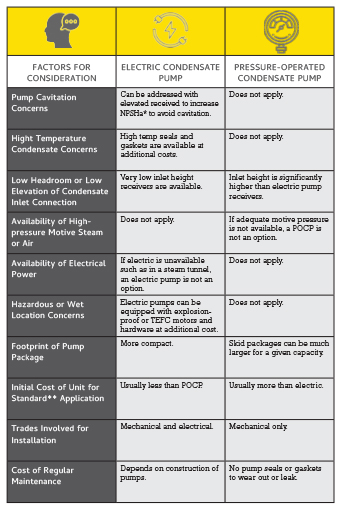
** Comparing pump packages for indoor installation in a non-hazardous location, using typical materials of construction (carbon steel receivers, cast iron/bronze-fitted pumps for electric pumps, steel housings with stainless steel mechanisms for POCPs).
Receiver Sizing
Most manufacturers size the minimum net receiver capacity on their electric condensate pump packages for 1 minute’s worth of pumping capacity. On pressure-operated pump packages, consult with the manufacturer, as there may be other considerations, such as the amount of flash steam that the receiver must accommodate. On either type of pump, there is no downside to over-sizing the receiver other than higher initial cost and minor system energy losses from added radiation.
Inlet Height of Receiver
The elevation of the condensate pump receiver inlet must never be higher than the outlet of the steam traps it serves. Condensate must flow freely by gravity into the pump receiver without any lifts in between!
High Temperatures
Particularly when using electric condensate pumps, pay attention to the condensate temperature that the pump will see, ensuring that seals and gaskets are compatible. Also on electric pumps, check that the pump will not cavitate with the expected condensate temperature entering the pump. Remember that NPSHa (available to the inlet of the pump) must always be greater than NPSHr (required per the pump manufacturer), for it not to cavitate. If high pressure/high temperature condensate returns lines are routed to an electric condensate pump, a separate flash tank is recommended upstream of the pump to allow condensate to cool somewhat before entering the electric pump receiver. By contrast, pressure-operated pumps have no cavitation concerns whatsoever.
Accessories
Good practice is to include (at a minimum) a receiver level gauge glass and thermometer, in order to monitor condensate conditions within the tank. Also, consider adding pump discharge pressure gauges, and isolation valves for ease of servicing pumps without draining the receiver.
Multiplex Pumps
Specifying a duplex (two pump) system or more (e.g., triplex, etc.) adds redundancy to the system, resulting in higher availability of the system should one pump fail.
Electrical Characteristics
Be aware of any potential corrosive or hazardous environments, in which the pump will be expected to operate. Examples include outdoor applications exposed to rain and freezing temperatures (or even flooding), or areas exposed to explosive gases or dust. In these cases, selection of the correct pump motors, control panels, and other electrical accessories is absolutely critical for safe and reliable operation! In some cases, a pressure-operated pump (which uses no electricity) may be a better choice for these applications.
The steam system designer must consider a number of variables when choosing a condensate return pump for their system. Factors such as inlet height constraints, maximum condensate temperature, availability of utilities, and external environment all play a role in determining the right selection for the application. It’s best to work with an industry professional who has experience in guiding these types of decisions.
FOR MORE INFORMATION
Eric Sengheiser is a mechanical engineer and the president of Control Products Inc., a steam and fluid control specialist providing reliable system solutions for more than sixty years. In addition to in-house expertise, the company’s stocked warehouse of control valves, steam traps, and regulators from a variety of brands, assures its customers that they will receive the parts they need quickly. For more information, visit www.cpinc.com.
MODERN PUMPING TODAY, December 2021
Did you enjoy this article?
Subscribe to the FREE Digital Edition of Modern Pumping Today Magazine!
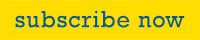