Read Part 1 Here!
In last month’s start to this article, we explained how, for several different applications, medium voltage VFDs are typically superior to alternative technologies. In the conclusion that follows, we’ll explore how medium voltage VFDs stack up, specifically against mechanical devices, mechanical transmission methods, and mechanical throttling devices. Plus, depending on the particular application, medium voltage VFD installations can exhibit other benefits that may be difficult to quantify.
COMPARISON AGAINST MECHANICAL DEVICES
The common thread of medium voltage VFDs versus mechanical device applications is that with a VFD the motor is operated at the exact speed required to satisfy the actual process flows and load on the motor, and no greater. This is in contrast to solutions that use transmissions, valves, or dampers to throttle excess mechanical or hydraulic energy that is generated by the equipment operating at full speed or a fixed reduced speed.
VFDs inherently generate only the mechanical or hydraulic energy necessary to operate the actual load; therefore, medium voltage VFDs will use less energy in almost any given application. With proper design, operating the motor at slower speeds also tends to reduce motor and equipment maintenance requirements. It can also extend operating life, often by years. Additionally, using a VFD eliminated the starting mechanical stress on the motor, which also increases the motor life. In new applications, a motor designed to operate exclusively with a VFD can be less expensive than a motor designed to allow an across-the-line start, because of the benign nature of VFD starting characteristics. In effect, the additional costs of a VFD are partially offset by the opportunity to use a less-expensive motor.
The electronic nature of medium voltage VFDs can also allow more precise speed control than with mechanical throttling components that can stick or fail. Controlling speed closer to its set point can improve operations by enabling production of better quality products and by increasing plant capacity and reliability.
For example, control valve and fan damper movement can become sluggish over time, moving control further from the set point for longer periods. Installing a medium voltage VFD will move control much closer to the set point, improving operations as well as reliability by eliminating the throttling devices and all of their associated problems and maintenance.
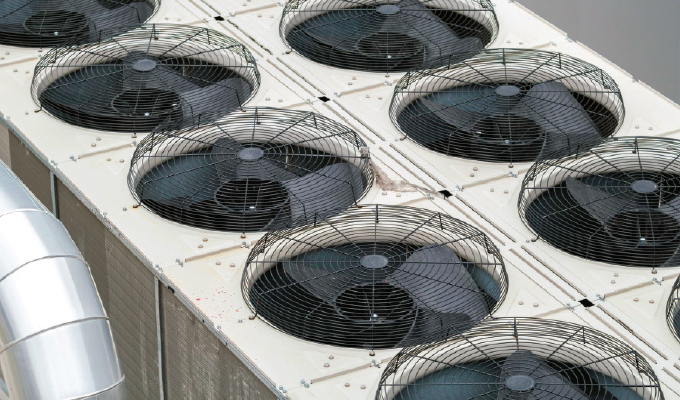
IN CONTRAST TO MECHANICAL TRANSMISSION METHODS
Mechanical transmissions are often installed between a full-speed motor and its associated drive equipment. Adjusting the transmission allows the speed of the outlet shaft of the transmission to vary to match load, but the motor will still operate at full speed, with its effective speed throttled by the transmission to match the load. This causes the motor to expend more electrical energy than if operated at the speed required by the load. The extra energy is dissipated in the transmission, and thus wasted.
Approximately 10 percent energy savings are typically associated when a mechanical transmission is replaced with a VFD. The electrical energy savings associated with a 2,000-kW load is, therefore, $800 per year per kW, or approximately $160,000 per year.
In addition, VFD operation generally reduces the complexity and sophistication of the mechanical transmission, and can actually eliminate the need for a transmission in some applications. Although most applications require operation at lower-than-rated motor speed, some VFDs are capable or operating at frequencies up to 450 Hz, or a motor speed of up to 22,000 rpm. In these cases, the complex transmission can be completely eliminated; the maintenance costs associated with these devices are also eliminated.
For example, a fan can be throttled between 100 and 400 rpm by using an 1,800-rpm motor with a hydraulic coupling that can adjust the speed of its outlet shaft speed and, hence, fan speed. This mechanical configuration could be simplified by using a reducing coupling and a VFD. In some instances, elimination of the coupling would be possible by directly coupling a motor operated by a VFD.
There are many such pump, blower, and fan applications that use mechanical transmissions to vary equipment speed. However, many major pieces of equipment in the mining industry (see Table 1) deserve special scrutiny because (depending upon application) medium voltage VFDs can improve speed control, allow implementation of torque control, improve product quality, reduce inrush current and smooth motor starts, lengthen maintenance intervals, and lower the energy costs associated with operating the equipment.
In new applications, the cost savings associated with eliminating engineering, purchasing, installation, and maintenance of the mechanical transmission can offset much—or even all—of the cost of the medium voltage VFD, in addition to occupying less space in the plant. In existing applications, energy savings, and operational improvements should be evaluated to justify replacing the existing motor starter and mechanical transmission with a medium voltage VFD.
VERSUS MECHANICAL THROTTLING DEVICES
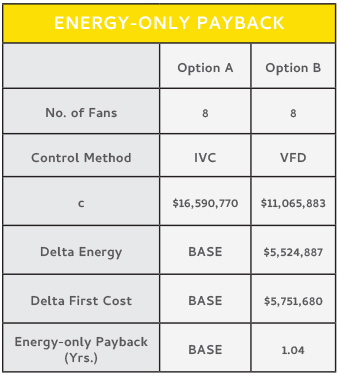
Perhaps the most common alternative solution to medium voltage VFDs is where mechanical equipment is directly connected to an electric motor operating at full speed, and the load is varied using a throttling device (such as a control valve or damper) to control air or fluid flow in order to satisfy the process demand. Pump, blower, and fan installations are often configured in this manner.
Operating a motor at full speed and then dissipating a portion of that energy across a throttling device is inherently wasteful. Nonetheless, this scenario is common practice in industry. In many cases, this is due to a continuation of past practices that may have made sense many decades ago when medium voltage VFDs were relatively expensive and power was cheap. But in today’s world, using a medium voltage VFD to operate the same equipment at a lower speed such that its energy output exactly matches the load offers a very quick and reasonable payback in nearly all cases.
Because the discharge of pumps, blowers, and fans powered by medium voltage motors is typically throttled, this equipment and associated motors are routinely oversized to account for maximum operating conditions, plus some contingency for abnormally high loads. Oversizing increases initial and operating costs, often by substantial amounts, particularly as the equipment and the motor are often quite large.
For example, a single-speed medium voltage motor with mechanical throttling may need to be sized at 1,200 kW to handle a nominal 1,000 kW load. The motor will, of course, operate at full speed, with the throttling device matching the load to the process requirements and dissipating energy. Applying a VFD in this case could reduce the required motor size to 1,000 kW and allow operation at about 70 percent of load, or 700 kW. The VFD would thus save 500 kW per hour—equating to a savings of $400,000 per year, assuming 8,000 hours of operation and power purchased at $0.10 per kWh.
Mechanical throttling devices are subject to mechanical degradation that tends to increase the hysteresis inherent to their design. For example, a damper mechanism may increasingly stick over time. These degradations further reduce performance and increase costs. Utilizing a medium voltage VFD instead of a throttling device not only decreases the inherent hysteresis to the speed resolution of the VFD, but also eliminates mechanical degradation, reducing required maintenance while improving performance.
ADDITIONAL BENEFITS
Depending on the particular application, medium voltage VFD installations can exhibit other benefits that may be difficult to quantify. Although these benefits don’t apply in all situations, they can be significant in certain applications.
For example, synchronous transfer allows a single VFD to control the speed of multiple motors, which can not only reduce cost but also simplify operation and maintenance. Savings can be substantial as only one VFD needs to be purchased, installed, and maintained. Of course, these benefits only apply when just one of the multiple motors is needed at any instant in time.
Sinusoidal VFD outputs can reduce the wear and tear on the motor, which can extend its useful life. This benefit becomes more significant as the quality of the VFD output improves, and as the motor’s operating hours increase.
Finally, purchasing the VFD and the motor from the same manufacturer can extend warranty life, as some suppliers will extend warranty periods in these cases, and can decrease operating costs due to a closer match between the VFD and the motor.
CONCLUSION
The economic and operational advantages achieved by applying VFDs to medium voltage motors is overwhelming in many cases, particularly when utility rebates are taken into account. For example, a project with motors totaling 10,000 kW can result in a one-time rebate of almost $500,000. To further quantify, consider this application where a utility in Texas needed to choose between two options for the operation of eight 10,500-horsepower, induced draft (ID) fans, four per each for two new 850 MW power plants.
Option A would run each fan and its associated motor at full speed, and control the air flow output with vanes. Option B would use a VFD on each motor to control fan speed as required to deliver the precise required air flow. Each fan would be driven by a medium voltage motor: 13.8 kV in the case of Option A and 6.6 kV for Option B.
Option B would cost $5,751,680 more to implement, but would result in annual energy savings of $5,524,887, equating to an energy-only payback period of just 1.04 years (see Table 3). These savings don’t take into account utility rebates, which vary significantly but are generally quite substantial. They also don’t take into account the other benefits delivered by VFDs as detailed in this article.
Applying VFDs to medium voltage motors provides the ability to do the same amount of work with less energy while increasing operational flexibility. Even modest speed reductions can result in large energy savings due to the relatively large motor sizes involved—especially when applied to centrifugal equipment. In addition to energy savings, medium voltage VFDs allow control closer to set point, which improves quality, reduces raw material usage and increases throughput.
Finally, reliability is improved because the motor and its associated equipment is controlled to a speed that closely matches the load, which minimizes wear and tear as opposed to other solutions. Achieving these significant gains is a multifaceted activity that can involve people knowledgeable in the electrical, mechanical, instrumentation, utility, chemical, and hydraulic disciplines as well as plant operations and management. Medium voltage VFDs are typically superior to alternative technologies. They should be considered for every medium voltage motor because even modest energy and operational savings can cost-justify VFD purchase and installation.
FOR MORE INFORMATION
Mark Harshman is principal engineer at Siemens. Siemens Corporation is a U.S. subsidiary of Siemens AG, a global technology powerhouse that has stood for engineering excellence, innovation, quality, reliability, and internationality for more than 170 years. Active around the world, the company focuses on intelligent infrastructure for buildings and distributed energy systems and on automation and digitalization in the process and manufacturing industries. Siemens brings together the digital and physical worlds to benefit customers and society. For more information, visit www.siemens.com.
MODERN PUMPING TODAY, December 2021
Did you enjoy this article?
Subscribe to the FREE Digital Edition of Modern Pumping Today Magazine!
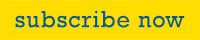