By Mark Harshman, Siemens
Medium voltage variable frequency drives (VFDs) are often the best choice to capitalize on opportunities to significantly reduce the operating and maintenance costs associated with relatively large rotating equipment. And because even a seemingly modest energy savings of a few percent of the operating load can translate into significant energy savings, there are many potential applications for medium voltage VFDs.
Medium voltage VFDs are applied to relatively large motors that can range in size from 200 to 100,000 horsepower. Such medium voltage motors typically operate between 10 and 15,000 rpm, at voltages between 2.3 and 13.8 kilovolts. Locating potential medium voltage VFD applications is relatively straightforward because every medium voltage motor should be considered a potential application—if only because of the significant energy savings associated with large motors.
Medium voltage drives are used for new installations or retrofit installations. In a new installation, the saved cost of not having to install alternative solutions such as dampers, valves, and mechanical transmissions can be applied to purchasing the medium voltage VFD. In some new applications, the installed cost of a medium voltage VFD can be less expensive than utilizing alternative solutions—especially when the alternative solution is expensive and requires additional plant modifications. In these applications, medium voltage VFDs not only reduce the overall cost of installation but also provide the additional benefit of reducing the total cost of operation.
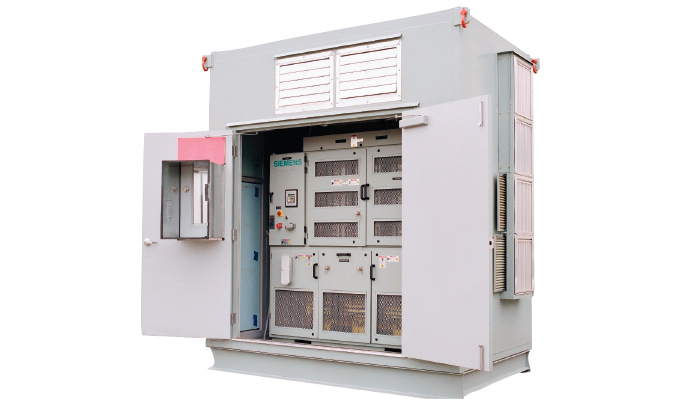
In retrofit applications, the full costs of purchasing and installing the medium voltage VFD—plus the cost of removing or disabling the existing alternative device—makes justification more challenging. Nonetheless, there are still many viable retrofit applications, especially when averted maintenance, repair and replacement costs for mechanical systems can be applied to purchasing the medium voltage VFD—along with much lower energy consumption. In many cases, the VFD will provide a payback in less than two years due to these energy savings; this does not include the reduced cost of ownership when compare to some mechanical systems.
For both new and retrofit applications, the utility serving the plant will often offer financial incentives for installing a VFD, which can greatly reduce costs as well as payback time.
Motors in which the hydraulic energy or mechanical energy generated by the motor is throttled are prime applications for medium voltage VFDs because matching the motor speed to the load conserves the electrical energy associated with generating the throttled energy. For example, it is not uncommon to throttle equipment down to as low as 70 percent of its full load capacity. By matching the motor speed to the reduced capacity of 70 percent, a 50 percent reduction of energy costs is achieved. The affinity laws allow for significant energy savings for even minor reductions in speed, which are realized and saved by using a VFD.
LEADING MEDIUM VOLTAGE VFD APPLICATIONS IN MAJOR VERTICAL INDUSTRIES
Building automation | Cooling tower pumps, cooling tower fans, chiller fans, chilled water pumps, refrigeration compressors |
Cement | Conveyors, kiln drives and fans |
Chemical and Petrochemical | Utility pumps, process pumps, fans, blowers, air compressors, process compressors, coolers, cooling tower pumps, cooling tower fans |
Food and Beverage | Utility pumps, fans, blowers |
Marine | Long cable, offloading pumps, topside compressor |
Mining | Conveyors, ball mills, grinders, crushers, mobile equipment (haul trucks, draglines, shovels) |
Oil and gas | Utility pumps, process pumps, fans, process compressors, air compressors |
Power | Induced draft fans, forced draft fans, cooling tower pumps, cooling tower fans, atomization air compressors |
Pulp and Paper | Chippers, conveyors, debarking, fans, paper machine line shafts, pumps, refiners, shredders |
Water/Wastewater | Process pumps, fans, blowers, air compressors |
BIG MOTORS, BIGGER SAVINGS
A VFD is an electronic device that electronically alters the frequency and/or voltage fed to a motor to change its speed, and consequently the speed of the attached equipment. Most plant engineers are comfortable with low voltage VFDs and may use them extensively in their processes to control motor (and equipment) speed where necessary or desirable to improve product quality, increase productivity and/or reduce maintenance. Creative plant engineers are constantly finding new VFD applications in their plants.
Medium voltage VFDs accommodate larger motors than their low-voltage equivalents, operating at higher voltages to drive larger equipment. Their applications are often similar in nature to low voltage VFDs—just with bigger sizes and higher voltages and costs. Importantly, the energy savings associated with medium voltage VFDs are typically much higher than for low voltage VFDs because medium-voltage motors use much more electrical power.
For example, the savings associated with a 40 percent energy use reduction in a motor consuming 50 kilowatts is 20 kilowatts. The savings associated with a 20 percent energy use reduction in a motor consuming 1,000 kilowatts is 200 kilowatts—10 times more energy savings. This illustrates how the energy savings associated with one medium voltage motor can dwarf the energy savings associated with many smaller low-voltage motors.
To put these savings in numerical terms, if power is purchased from the utility at $0.10 per kilowatt-hour and if the motor operates for 8,000 hours per year, the annual energy savings is approximately $800 per year per kilowatt. In the above example, applying a VFD to this medium-voltage motor will reduce electrical energy costs by approximately $160,000 per year.
However, many plant engineers are not aware that medium voltage VFDs are available at reasonable costs, relative to their potential energy savings. They may also not know that they have been using throttle control for their large mechanical equipment in industrial plants and other facilities for decades—often for months or years without being shut down—and sometimes in applications that require precise speed control. Further, they are often not aware of the magnitude of the potential energy savings associated with medium voltage VFD applications.
Table 1 lists some industries where medium voltage VFDs are commonly applied, along with their typical applications. Naturally, plants with more medium voltage motors tend to have more potential medium voltage VFD applications. However, having only a few medium voltage motors should not discourage consideration; the application of just one or two medium voltage VFDs—even in plants dominated by low-voltage motors — can have important economic implications. In the cement industry, for example, a single plant typically has almost thirty medium voltage drives, ranging in power from 500 to 2,000 horsepower in pump, kiln and fan application.
In some plants, even as few as one or two medium voltage VFD applications can reduce overall electrical energy consumption significantly more than dozens of low voltage VFD applications. Therefore, the large economic impact of applying medium voltage VFDs in these plants typically results in considering the largest motors first, as this is where savings are greatest.
ADVANTAGES OF MEDIUM VOLTAGE VFDS OVER ALTERNATIVE SOLUTIONS |
1. Decreased electrical energy consumption |
2. Lower electrical demand charges from utilities |
3. Decreased capital cost due to rebates from electric utilities |
4. Decreased net electrical energy costs from power regeneration |
5. Improved operating efficiency |
6. Improved process control due to superior speed control |
7. Increased product quality |
8. Increased process reliability |
9. Increased process throughput |
10. Reduced downtime |
11. Reduced maintenance |
12. Reduced mechanical stress on associated equipment |
13. Reduced motor stress through inherent soft-starting |
MEDIUM VOLTAGE VFDS VS. ALTERNATIVE SOLUTIONS
In many applications, medium voltage VFDs are superior to alternative solutions for controlling motor speed such as direct current drives, soft-starters, two- and three-speed motors, and single-speed motors coupled to various transmission components.
In other applications, medium voltage VFDs can replace mechanically based solutions used to control process parameters, such as the flow of a gas or liquid. For example, the flow of air into a large furnace or boiler can be regulated using a single-speed motor and air vanes. However, controlling the mechanical equipment by using a medium voltage VFD to vary motor speed usually results in a superior process control, increased reliability and improved operational costs.
In either case, medium voltage VFDs offer many advantages over alternative solutions. Some of the advantages are listed in Table 2. Note that these advantages apply to specific applications in varying degrees. This will become evident when the advantages and expected results from various medium voltage VFD applications are discussed below.
Medium Voltage VFDs vs. Direct Current Drives
Direct current (DC) drives vary motor speed by fluctuating the direct current voltage to the motor. VFDs, however, vary motor speed by fluctuating the frequency to the motor. Some of their advantages are similar because both control motor speed electronically.
DC motors are not as common and are typically more expensive than the corresponding alternating current (AC) motors used with VFDs. DC motors also have internal brushes that require periodic maintenance, thus compromising reliability.
As a result, the industry trend has been towards the application of AC motors. The large population of AC motors and numerous variable speed applications has tended to reduce the cost of VFDs as compared to DC drives.
DC drives have historically been used for applications that require precise speed and torque control, but due to improved AC VFD technology and declining costs, few applications still require DC drives and motors with their higher upfront and maintenance costs.
Medium Voltage VFDs vs. Soft-starters
Motors generally exhibit high inrush currents when started. The current falls to normal levels after the motor reaches full speed a few seconds later. Inrush currents can play havoc with plant electrical distribution systems, and can also result in very high demand charges from the electric utility. Demand charges are typically assessed based on the greatest instantaneous power usage—a figure that can be quite high if a large motor is started at full speed.
One method of reducing the magnitude of inrush currents and the resultant stress on the motor is to use a soft-starter that electrically reduces voltage to the motor for a few seconds before switching to line voltage. Soft-starters cannot vary motor speed, so they are not an alternative to a VFD in most applications.
VFDs are inherently soft-starters because VFDs ramp the voltage to the motor and limit inrush currents. In this regard, VFDs provide even softer starts than traditional soft-starters. VFDs can almost always start a motor and will draw significantly less starting current (usually less than 100 percent rated FLA) than soft-starters that still draw up to 300 percent inrush current.
VFDs are not recommended in applications where precisely controlling motor speed does not provide economic or operational benefit. In these applications, soft-starters may be required to address electrical problems associated with high inrush current, and will be a more economical solution than a VFD.
Medium Voltage VFDs vs. Two-speed Motors
Starters that electrically alter the motor winding connections can allow the same motor to operate at two speeds—typically full speed and 50 percent speed. Operation at the reduced speed when the motor is lightly loaded can reduce the electrical energy consumption of the motor. This can represent significant energy savings under low load conditions. However, when the process load increases, the motor will be switched to full-speed operation and consume much more energy.
In contrast, VFDs can vary the motor speed continuously from zero to full speed, allowing the motor to operate at the precise speed needed to match the load and process requirements. The VFD strategy of matching the speed to the load is much more energy efficient, resulting in significant savings.
To illustrate, consider this VFD application: A medium voltage motor connected to a centrifugal fan consumes 600 kilowatts of electrical energy while operating at 60 percent speed using a VFD.
In contrast, a two-speed motor would have to operate at full speed because 50 percent speed will not satisfy the load. Increasing the motor speed in this manner will increase energy consumption to 1,000 kilowatt at full speed.
If power is purchased from the utility at $0.10 per kilowatt-hour and if the motor operates for 8,000 hours per year, the annual energy savings saved is approximately $800 per year per kilowatt. If this motor can be operated at 60 percent speed, applying a VFD to this motor will reduce electrical energy consumption by approximately 400 kilowatts—or $320,000 per year.
A LOOK AHEAD
In next month’s wrap-up, we’ll further explore how medium voltage VFDs stack up, specifically against mechanical devices, mechanical transmission methods, and mechanical throttling devices. Plus, depending on the particular application, medium voltage VFD installations can exhibit other benefits that may be difficult to quantify. All of this bolsters how medium voltage VFDs are typically superior to alternative technologies.
FOR MORE INFORMATION
Mark Harshman is principal engineer at Siemens. Siemens Corporation is a U.S. subsidiary of Siemens AG, a global technology powerhouse that has stood for engineering excellence, innovation, quality, reliability, and internationality for more than 170 years. Active around the world, the company focuses on intelligent infrastructure for buildings and distributed energy systems and on automation and digitalization in the process and manufacturing industries. Siemens brings together the digital and physical worlds to benefit customers and society. For more information, visit www.siemens.com.
MODERN PUMPING TODAY, November 2021
Did you enjoy this article?
Subscribe to the FREE Digital Edition of Modern Pumping Today Magazine!
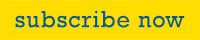