By John Calder, Dura Pump
Mechanical seals prevent pumps from leaking by containing the pressure of the pumping process and withstanding the friction caused by the pump shaft rotating. This leads to less wasted product, money saving, and less clean up.
Mechanical seals are the most common cause of pump downtime and account for more pump repair costs than any other part of a pump. Therefore, it’s important that they are installed and maintained properly to prevent failures. Here are some of the things you should be looking out for.
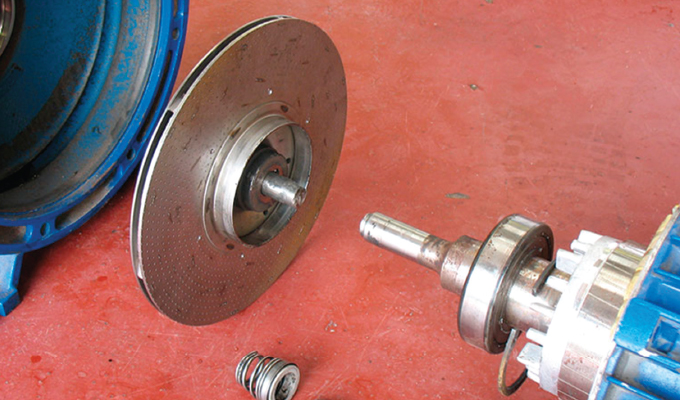
INSTALLATION ERRORS
Installation errors can easily damage mechanical seals so it’s incredibly important that mechanical seals are installed by a professional and that the installation instructions are followed exactly. If a pump is started with an incorrectly installed seal major damage could occur and potentially damage other parts of the pump as well as the seal.
Potential errors include:
- Shaft misalignment
- Seals not mounted perpendicular to the shaft
- Axially moving shaft
- Wrong assembly length
- Dirt on the seal face
- Over-tightening of fasteners
- Hammering couplings into the shaft
- Using the wrong seal
Seals not mounted perpendicular to the shaft
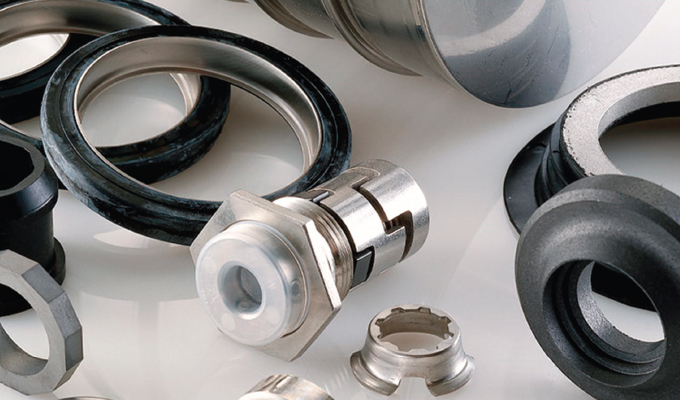
POOR OR ABSENT LUBRICATION
A mechanical seal might fail due to poor lubrication, or no lubrication at all. When there is no liquid around the seal it will be subjected to increased amounts of friction which will increase the temperature inside the pump. This rapid increase in temperature can cause burnt elastomeric parts and damage o-rings or rubber on the seal. This usually happens when there is no pumped medium in contact with the seal rings to transfer the heat.
Also, when lubrication is poor or absent mechanical seals made of hard materials will make quite a loud noise, this will cause parts of the seal to vibrate which can reduce the life expectancy of both the seal and the pump.
SYSTEM FAILURES DUE TO CHANGES IN OPERATING PARAMETERS
It is vital that the operating parameters of your pump system are what the pump system was designed for, or least the parameters can be met by the pump system you are using. A change in operating conditions may affect the performance of the mechanical seal.
The following parameters affect the performance of a mechanical seal.
- The pressure in the seal chamber
- The temperature around the shaft seal in the seal chamber
- The pumped medium
- The speed
- The shaft seal dimensions
Any adjustments to these parameters could result in malfunction or damage to the mechanical seal. If you plan to make any adjustments to any of these parameters, we would recommend consulting a professional first. Dura Pump can talk you through your pump system to ensure that it is actually capable of running with the adjusted parameters.
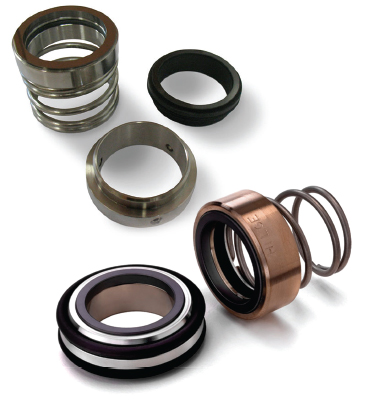
HIGH CHEMICAL AND PHYSICAL DEMANDS
All parts of the mechanical seal need to be resistant to the chemical and physical demands of the pumping process. Severe chemical or physical loading can reduce the expected working life of the seal and potentially lead to rapid degeneration and malfunction. It is vital that the pump system is designed to handle such demands and if any changes are made to the level of chemical and physical demand of your pump process, the pump system should be assessed to ensure it can handle it.
Also, when seals are exposed to high-pressure gas at elevated temperatures for a prolonged period of time the gas absorbs into the rubber. If the pressure is decreased and the absorbed gas cannot escape as fast as the pressure is decreased the gas will expand and cause blisters and ruptures on the seal surface. This could cause complete destruction of the seal and even an explosion due to decompression. On the other hand, if the volume of trapped gas is small, the blisters may recede as the pressure is equalized with little effect on seal integrity.
PUMPING SLURRY
Slurry is a semi-liquid mixture typically of fine particles of manure, cement, or coal and water; however, it can be any type of solid suspended in any liquid. A slurry is particularly likely to damage mechanical seals. Some of the problems they can cause include:
- Clogging of the flexing parts of the mechanical seal causing the lapped faces to open
- Wear on rotating components
- Eroding of the impeller
- Wear will gradually decrease the efficiency of the pump
EXPERIENCING PROBLEMS WITH YOUR MECHANICAL SEAL?
Dura Pump’s team of experienced pump engineers are available for repairs 24/7. If you are experiencing problems with your mechanical seal, get in touch and we’ll send out an engineer who will attempt to carry out repairs on site. If this isn’t possible, we use our state-of-the-art workshop to get everything back up and running quickly and efficiently.
To maintain our high standards of service we currently operate within a two-hour radius from Northampton with our trusted partner companies covering the remainder of the United Kingdom. So whether customers need a simple, urgent pump repair, or a whole new system, Dura Pump’s team can provide options to help.
FOR MORE INFORMATION
Dura Pump’s dedicated team of pump specialists key aim is to ensure we provide customers with specialist fluid control that guarantees increased productivity and profitability for our clients through reliable and efficient solutions. For more information, visit www.durapump.co.uk.
MODERN PUMPING TODAY, May 2020
Did you enjoy this article?
Subscribe to the FREE Digital Edition of Modern Pumping Today Magazine!
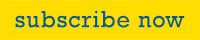