By Heinz P. Bloch
High asset reliability should be our priority, because the illusory “savings” derived from forever repairing cheap equipment have vanished with the first major repair. That repair, of course, was often decades ago. But suppose that not only is your plant old but the EPC (engineering/procurement/construction) contractor received a bonus for coming in under budget. In that case, some of your equipment is almost certain to have come from the lowest bidder and the average MTBR (mean time between repairs) of your vertical pumps is probably well below today’s industry average of around 4.5 years.
IMITATE BEST-IN-CLASS PERFORMERS
If moving towards the ranks of best-in-class performers (“BiCs”) is in your plans, consider viewing the next repair event as an opportunity to go beyond the usual repair. Work with a competent shop facility, one that will assist you in combining the repair with some judicious upgrading. While improvements to hydraulic efficiency and extending the safe head/flow range are often feasible, upgrading equipment also implies imparting extended life expectancy or greater run lengths before the asset requires repairs. That type of upgrading usually involves the mechanical end of a vertical pump.
Experience shows that proven upgrades will move vertical pumps out of the failure-prone side of the MTBR data base and to the more reliable side of a facility’s MTBR tabulation (see reference 1). The reasonable incremental cost of proven upgrades will often surprise the plant’s reliability staff and their managers. Where no in-plant statistics exist, interested parties can select time-tested ways to perform straightforward, yet relatively accurate cost justifications for upgrades to either the widely used back pull-out vertical inline pumps in figure 1, or the column-style deep-well pumps shown in figure 2 (see reference 2).
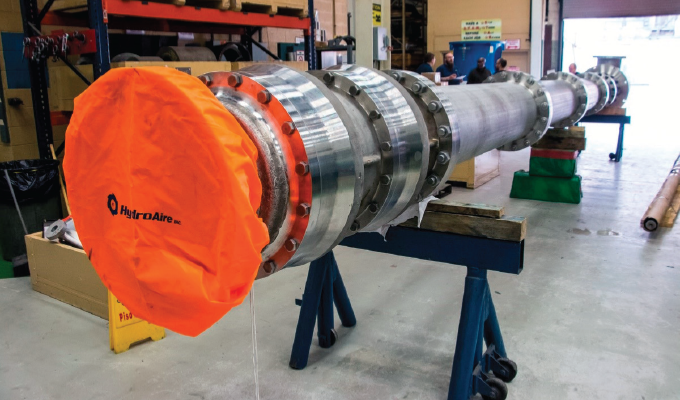
SINGLE-STAGE IN-LINE PUMPS
A widely used version of a single-stage in-line back pull-out pump is shown in figure 1. Contrary to occasional assumptions, these pumps fail no more often than their traditional horizontal shaft counterparts. A major refinery with over 1,000 horizontal and hundreds of vertical API-compliant single stage back pull-out pumps (Style OH5) recorded its failure statistics over a five-year period. With a mean-time-between repairs (MTBR) of 7.4 years for one and 7.6 years for the other style, there was no meaningful difference. However, an often-overlooked installation prerequisite is to allow such pumps to float; they should never be bolted down on the foundation. In other words, they must be free to move to wherever the associated piping is pushing them. Upgrading consisted of bolting a steel plate to the top of the concrete foundation and allowing the pump to freely move in whatever direction it wanted to go. Resist the temptation to insert only a single Teflon® plate between pump body and steel plate. The rough surfaces of plate and pump body will dig into the Teflon and inhibit movement. If you want low-friction movement, use either two Teflon plates or none at all.
Note that single-stage vertical pumps are also available with an extended-length distance piece bridging the approximately 8-inch distance between the motor frame and pump housing. This will allow insertion of a suitable spacer coupling. The less expensive and more widely used standard version (API designation OH5) depicted in figure 1 uses a rigid coupling and short motor shaft. Here, the prevailing loads must be absorbed by the motor bearings whereas, in the slightly more expensive extended-length version, the loads are distributed over both motor and pump bearings.
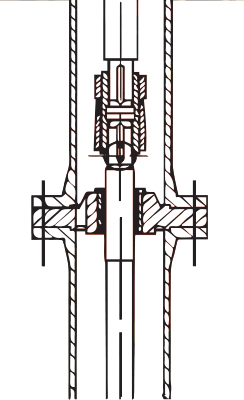
Pump styles incorporating rigidly coupled short shafts and styles with pump-to-motor shafts bridged by a flexible spacer coupling, are available with drivers delivering well in excess of 100 kW. The extended length distance piece version requires slightly more attention to vibratory resonance suppression. However, competent vendors and reliability-focused users know how to avoid surprises related to resonance-induced vibration activity.
Today’s analytical methods can be used to recommend where and what external pipe locations or supports will benefit from stiffening or bracing. Alternatively, an adjustable weight pendulum could be mounted at the structure to move resonances away from pump speeds and their respective multiples. In any event, many existing vertical pumps benefit from upgrading at the next repair opportunity.
Bearing upgrades are not usually needed for OH5 style inline pumps. However, wear ring replacement is often cost-justified. Top-of-the-line carbon-filled Perfluoro-Alkoxy (PFA/CF) materials have been used to upgrade the wear rings in virtually every type of pump. PFA/CF has also become the material of choice in situations where metallic wear rings are not standing up to harsh conditions (see reference 2). Perfluoro-Alkoxies are in the Teflon family but exhibit a lower coefficient of thermal expansion (CTE) than either Teflon or the metallic wear parts used earlier in a particular pump design.
UPGRADING MULTI-STAGE VERTICAL PUMPS
Multi-stage deep well pumps are available in styles and models that range from just one horsepower and single stage to multi-stage versions that often comprise over twenty stages and horsepower levels in the mid four-digit range (see reference 3). Some have their column bearings encased in a tube or inner pipe which allows strict separation between lubricant and the liquid (“pumpage”) being pumped in the surrounding annulus. In other words, the pumpage rises between the inner pipe and a much larger diameter outer pipe. However, in the most popular style (see figure 2), there is no separate inner pipe. On its way from pump suction to discharge, the pumpage makes contact with the column bearings, one of which is shown in figure 3.
INVOLVE EXPERIENCED PUMP REBUILDERS
The largest independent repair-upgrader has branch facilities in countries around the world and pre-qualifying (assessing the competence) one of the rebuilder’s nearby locations will save much time later. A qualified rebuilder will be staffed by key employees with instant access to a team of highly experienced design engineers. Expect this team to be stationed at the rebuild shop’s HQ location in a major industrial city. Designating a rebuilder with a test stand for vertical column pumps in the high power and deep-well categories could prove advantageous. Discontinuing metallic wear parts and replacing them with carbon fiber-filled Perfluoro-Alkoxy (PFA/CF) wear rings is usually cost justified and should be part of the upgrading (see reference 2).
BEARING UPGRADES
A closer look at more substantial bearings and advantageous lube application methods is desired whenever in-plant failure statistics point to weaknesses.
This is when reliability-focused plants consider upgrading to better bearings and lube application methods. Possible bearing upgrades and proven lube application methods include tapered roller bearings and oil mist lubrication (see reference 4).
REFERENCES
- Bloch, Heinz P., “Pump Wisdom, Problem Solving for Operators and Specialists” (2011), John Wiley & Sons, Hoboken, NJ, ISBN 978-1-118-04123-9.
- Bloch, Heinz P., “Fluid Machinery: Life Extension of Pumps, Gas Compressors and Drivers” (2020), DeGruyter, Berlin, Germany, ISBN
978-3-11-067413-2. - Bloch, Heinz P., “Petrochemical Machinery Insights” (2017), Elsevier Publishing, Oxford, UK, and Cambridge, MA.
- Bloch, et al.; “Optimized Equipment Lubrication, Oil Mist Technology and Storage Preservation” (2020), Reliabilityweb.com, Ft. Myers, FL, ISBN
978-1-941872-98-7.
FOR MORE INFORMATION
Heinz P. Bloch resides in Montgomery, Texas. His professional career commenced in 1962 and included long-term assignments as Exxon Chemical’s regional machinery specialist for the United States. He holds B.S. and M.S. degrees (cum laude) in mechanical engineering from the New Jersey Institute of Technology’s Newark College of Engineering (“NCE”) and was honored as one of ten inaugural inductees into NCE’s “Top 100 Hall of Fame.”
MODERN PUMPING TODAY, January 2021
Did you enjoy this article?
Subscribe to the FREE Digital Edition of Modern Pumping Today Magazine!
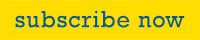