By Jason Wellnitz, Yaskawa America, Inc.
Many production settings have changed in the midst of social distancing. Employees are spaced six feet apart, assembly lines shut down, and some facilities are wholly left idle. As we prepare to get back to work, engage our customers, and ramp up production, it is important to consider the condition of our machines.
Performing preventive maintenance on your electrical equipment before powering them back up is an important step to a smooth startup and in ensuring machine longevity. Variable frequency drives (VFDs) are commonplace on motor-operated equipment for several reasons. One of the most noteworthy reasons is the reduction of maintenance costs, but VFDs also have a unique maintenance cycle.
INTRODUCTION TO PREVENTIVE MAINTENANCE
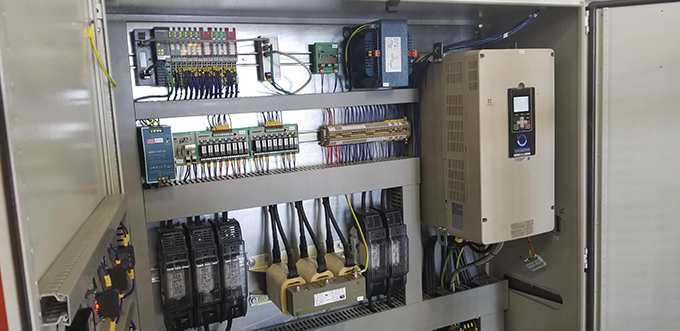
VFD preventive maintenance should be performed by a trained professional, which may be an on-staff electrician, contract electrician, or local electrical distributor. The preventive maintenance process should typically consist of four steps:
• Visual inspection of key components
• Checking power connections
• Verifying component life
• Reforming capacitors
VISUAL INSPECTION
During the visual inspection there are a few things that should be reviewed. First, look for signs of condensation, corrosion, dust, and foreign objects—think insects. Catching these simple issues can often be corrected onsite and save considerable repair expenses.
Next, check for heatsink and fan obstructions that can prevent the VFD from running cool. Enclosure air filters should also be checked for dust buildup, gaskets checked for deterioration, and replaced as necessary.
CHECKING POWER CONNECTIONS
Power connections can loosen with heating and cooling cycles. Loose connections can overheat and cause VFD faults, tripped branch circuit protection, or premature failure. The inspection should verify all power connections meet the torque specifications of the electrical equipment OEM(s).
Following proper torque specifications is critical. Some types of terminal blocks are prone to damage if over torqued. The maintenance professional may go the extra mile using a thermal imaging camera to check the power wiring for hot spots and correct accordingly. To perform the thermal imaging step, the equipment will need to be operational and running near capacity.
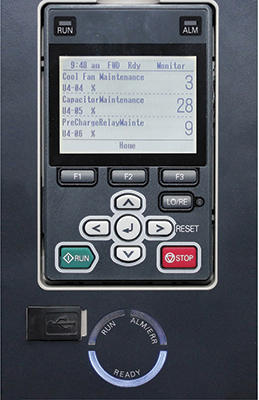
VERIFYING COMPONENT LIFE
VFDs are designed to operate maintenance-free for a defined period of time, usually five to ten years of operating time, depending on the manufacturer and model. Larger VFDs are designed to be serviced as specific components age.
During the preventive maintenance process, the VFD should be checked to determine the remaining life of the transistors, capacitors, fans, and pre-charge contactor, much like the remaining oil life readout in a car. This allows operations and maintenance staff to plan for service down time.
CAPACITOR REFORMING
Most VFDs utilize aluminum electrolytic capacitor technology as a fundamental component of the power structure. When left unpowered for long periods of time the capacitor dielectric breaks down and permanent damage can occur if power is applied in this condition.
Fortunately, aluminum electrolytic capacitors can be self-healed in a process called “capacitor reforming.” Capacitor reforming consists of slowly applying voltage to the drive and capacitors using a device known as a variac transformer or a current limited DC power supply. Some newer VFD models do not require capacitor reforming, but completing the process will not hurt the VFD in any way if it is not required.
Capacitor reforming is an important step in recommissioning VFDs and you should always follow the manufacturer’s recommendations when powering up a drive idle for more than six months.
VFDs left in storage as spare parts should have their capacitors reformed every one to two years to prolong their shelf life. Protecting VFDs from extreme temperatures, corrosive gases, and moisture will extend their life while they are in storage or long-term shutdown.
CONCLUSION
VFDs are designed to save energy, improve product and process quality, and reduce maintenance costs. Proactively maintaining your VFD investment on an annual basis will maximize uptime and help keep product flowing out your dock doors.
FOR MORE INFORMATION
Jason Wellnitz is product marketing manager for Yaskawa America, Inc. Yaskawa is the world’s largest manufacturer of AC inverter drives, servo and motion control, and robotics automation systems. Products are marketed through direct sales, partners, representatives, dealers, and distributors. Yaskawa America, Inc.—Drives and Motion Division is a wholly-owned corporation of Yaskawa Electric Corporation of Japan. Since 1915, Yaskawa Electric has served the world needs for products to improve global productivity through Automation. This website is designed to support Yaskawa customers in the Americas. For more information, visit www.yaskawa.com.
MODERN PUMPING TODAY, August 2020
Did you enjoy this article?
Subscribe to the FREE Digital Edition of Modern Pumping Today Magazine!
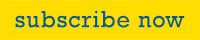