Finding the right test instrument for a defined application requires specific expertise. CETA Testsysteme, as a manufacturer of leak and flow testing devices, has more than thirty years of experience in industrial testing technology. Compressed air and hydrogen are used as test media. Several thousand CETA test devices are used worldwide by well-known industrial customers in production lines of serial products.
EVEN THE SMALLEST LEAKS MATTER
Leak testing with compressed air can be used to test tightness against liquids, as the viscosity of air is lower compared to liquids. Here the differential pressure test method is often used, in which the pressure drop due to leakage is measured as a pressure difference against a sealed reference volume. The minimum leakage rates detectable with this method are in the range of 10-3 mbar per liter per second. Would the leak only consist of a single hole, it would have a diameter of approximately 20 micrometers at a test pressure of 1 bar.
The size of the products tested for tightness ranges from small-volume microswitches with a volume of 0.1 milliliter up to tanks of 1,000 liters capacity. Depending on the application, CETA leak testers with gauge pressure or differential pressure sensors are used. Available pressure ranges are between -1 and 30 bar up to 400 bar with the pressure rise method (for example, testing of injection valves).
THE NEW FRONTIER IN LEAK TESTING
Typical leak testing applications are testing on oil and water tightness. By using suitable methods, a wide variety of products can be tested: directly fillable products (for example, housings, gear covers, containers, and lights), objects whose internal and external tightness must be ensured (for example, ball valves and gears), components with pressure compensation elements (membranes), as well as sealed test parts (for example, sensors, micro assemblies, and watches).
For the detection of smallest leakages in large-volume test parts, leak testing devices with calorimetric mass flow sensor and various measuring ranges (up to 600 millimeters per minute) are used. Here, the mass flow caused by the leakage is measured directly.
Very low leakage rates down to 10 mbar per liter per second (equivalent to a hole diameter of approximately 0.1 micrometer at 1 bar test pressure) can be detected with hydrogen leak testers. The patented and highly sensitive method is based on the detection of gases or vapors escaping from the test part in the case of leakage. This method detects forming gas (5 percent hydrogen and 95 percent nitrogen), alcohols, solvents, and generally volatile organic gas or vapor mixtures. These are either present in the test part itself or are supplied beforehand as tracer gas.
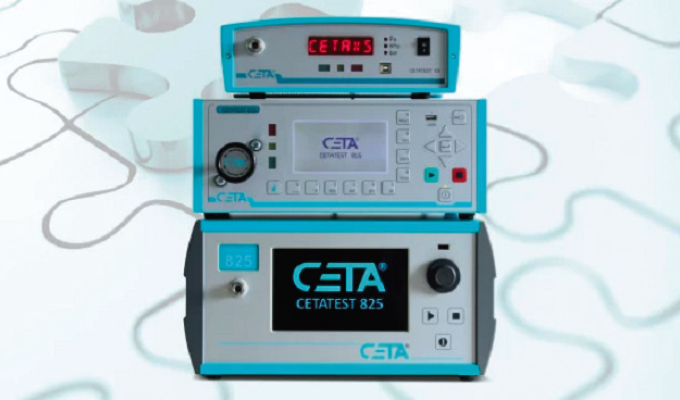
THE VALUE OF PRECISION TESTING
Due to different test device technologies and a wide scope of pressure and measurement ranges, nearly every test requirement can be fulfilled by modern testing technology like those provided by CETA. An integrated control of the correct test device function guarantees a high standard of process reliability.
The test devices are used by the customers for quality assurance, quality control, and production assurance. The customers mostly come from the fields of automotive industry, medical technology, heating and air-conditioning industry, fittings, and household appliances industry. The scope of products also includes semi-automatic test stands.
TODAY’S TECHNOLOGY CAN HELP
In addition to leak testing, there are products that are tested for flow. With the CETA flow testers, a range from 3 milliliters per minute to 200 liters per minute can be measured with different laminar flow elements. Typical products of which the flow rate is tested are pipes, cooling channels, valves, exhaust systems, and membranes.
The CETA testers are usually integrated into automated series production lines. A large number of common industrial interfaces are available for the connectivity. Well-known customers from the automotive industry, e-mobility, fittings, heating and air conditioning, medical technology, packaging, and appliance industries use the CETA test devices for quality assurance and to secure production.
THE LEARNING NEVER STOPS
But there’s more to today’s leak detection and prevention than just the equipment. Valuable insight can be shared from peers in the industry. For example, beginning this year, the CETA test device program, which includes leak test devices and flow test devices, has gone online with virtual seminars free to the public.
In order to be of the most benefit to the largest number of end users, the introductory online seminar will give an overview of the leak detector series and some application examples will be presented:
- CETA leak detectors
- Measuring principles (overpressure, differential pressure, mass flow)
- Schematic structure
- Leak tester series CETATEST XS and CETATEST 715 with overpressure sensor
- Leak tester series CETATEST 515 and CETATEST 815 with differential pressure sensor
- Leak tester series CETATEST 615 with mass flow sensor applications
During the introductory seminar, the test medium compressed air is mainly used, but there are different measuring methods for leak testing, which are covered by different product series.
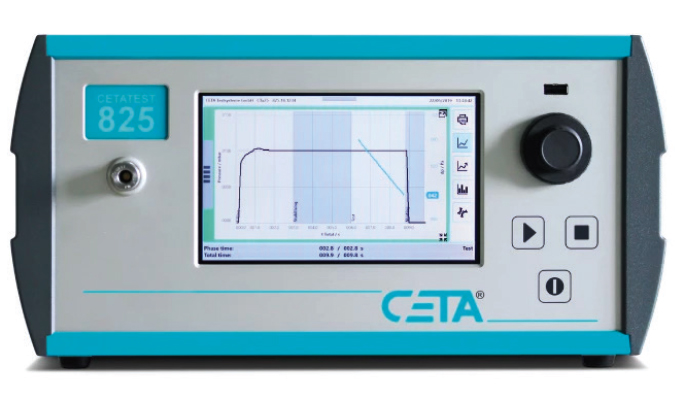
INNOVATION BUILT ON EXPERIENCE
CETA customers appreciate the longevity and the high quality of the test equipment, they honor the on-time delivery, the many years of experience and the high level of competence in solving test tasks and handling projects. Due to the high level of customer orientation, it is increasingly evident that CETA is involved at a very early stage of product development.
The company is certified according to DIN ISO 9001 and the calibration laboratory (D-K-19566) is accredited as a DAkkS calibration laboratory (according to DIN EN ISO/IEC 17025) for the measurand pressure up to 60 bar (also for on-site calibrations). The CETA test instruments are quality products and are delivered with a warranty of three years, with the optional extension to five years. The decision as to which test method is suitable depends on many factors, such as the special properties of the test part, the test parameters, the production cycle, and the specifications for measuring equipment capability.
Due to many years of experience in the implementation of testing tasks, combined with own product development, CETA advises its customers comprehensively in finding the optimal solution. These added values distinguish CETA as a solution partner for industrial testing tasks.
FOR MORE INFORMATION
DR. JOACHIM LAPSIEN is sales manager for CETA Testsysteme GmbH. CETA Testsysteme sees itself as a solution partner for industrial leak measurement technology and has been manufacturing physical measuring devices for industrial leak testing and flow testing applications for more than thirty years. CETA customers come mainly from the automotive industry; medical technology; the fittings, air conditioning, and household appliance industry; the packaging industry; and e-mobility. CETA measuring devices are used by customers for quality assurance, quality control, and production safeguarding, even in larger production plants. For more information, visit www.cetatest.com.
MODERN PUMPING TODAY, March 2022
Did you enjoy this article?
Subscribe to the FREE Digital Edition of Modern Pumping Today Magazine!
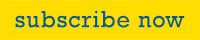