By Lin Liu and Suri Ganeriwala, SpectraQuest Inc.
In this article, fracture propagation is simulated using a finite element model for a gearbox that is designed for a rotor dynamic test rig. The circumferential plates of the gearbox are welded along the side as well as the bottom edges. Micro-cracks are usually generated at weld toes and the welding process will introduce residual stresses. The effect of the locations of initial fracture on fracture propagation path is studied.
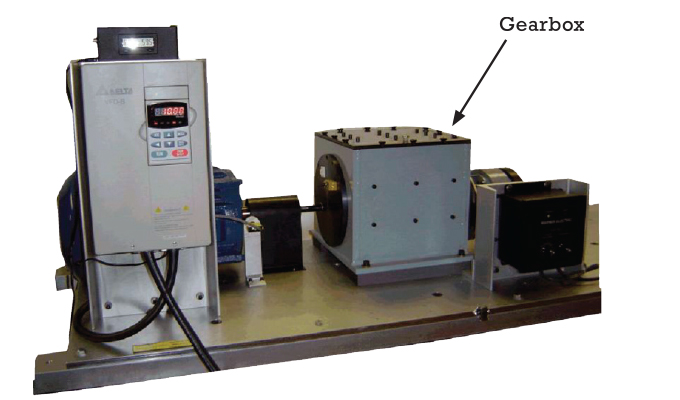
INTRODUCTION
SpectraQuest Inc. specializes in design, development, and fabrication of gearbox system for diagnostics and prognostics researches. Upon request from a customer, we have performed a numerical simulation of crack propagation in a gearbox. The gearbox is installed in the Gearbox Dynamic Simulator, which is illustrated in figure 1.
The gearbox is made of six aluminum plate. Each one of the four circumferential plates is welded with one another. Furthermore, the circumferential plates are welded to the bottom plate. The top plate is bolted to the circumferential plates. A closer look of the gearbox is displayed in figure 2.
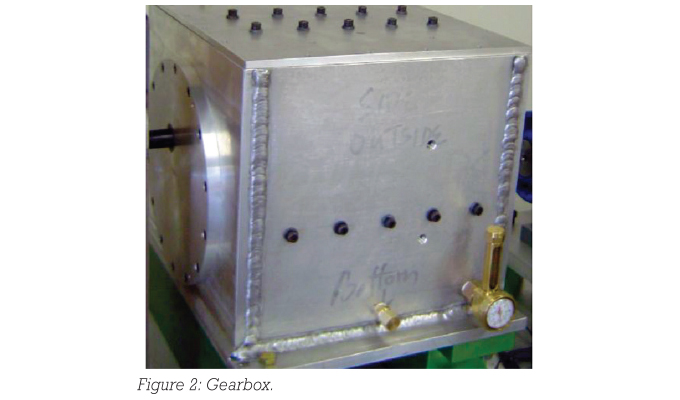
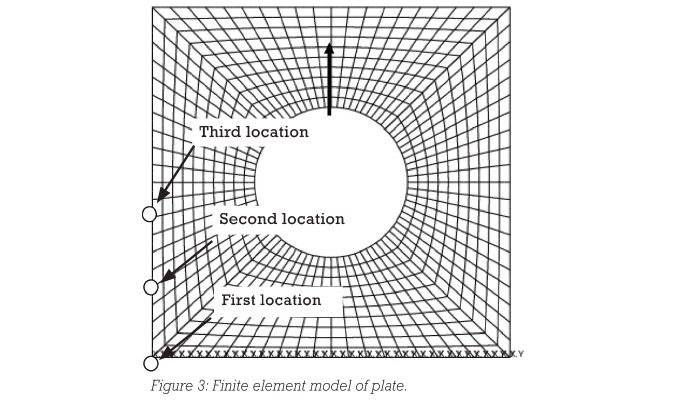
GEARBOX MODEL
The end plate of the gearbox facing the direction of the rotor “B” assembly is modeled in the work. The geometry of the plate is a 14 by 14 inches square with a 3-inch radius hole in the center. The thickness of the plate is 0.5 inches. Because of the small thickness of the plate, it can be considered as a plane stress problem and two-dimensional finite element model is created using FRANC2D software.
The finite element model is displayed in figure 3. There are total of 800 Q8 quadrilateral elements. The bottom edge is constrained both in the x and y directions. The assumed load is a node load applied at the uppermost node in the hole in the y direction with amplitude of 200 pounds.
An edge fracture is introduced on the left side of the plate with different initial locations. The three fracture initial locations studied in the work are displayed in figure 3. The lengths of three initial fractures are all 0.21 inches. And the initial crack direction is horizontal for all the three cases.
For each fracture studied, automatic fracture propagation is performed. The crack increment length is 0.2 inches, and fifteen steps are simulated.
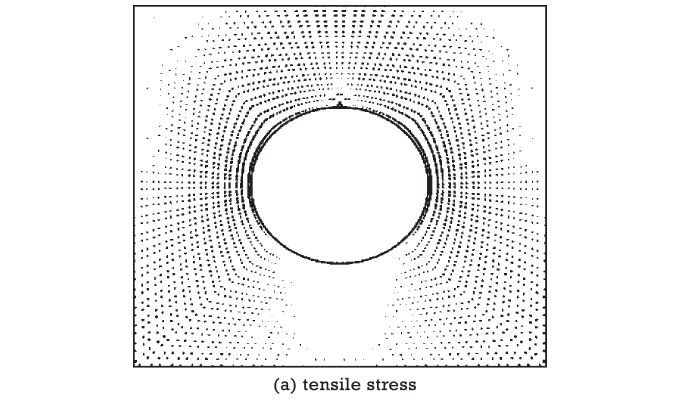
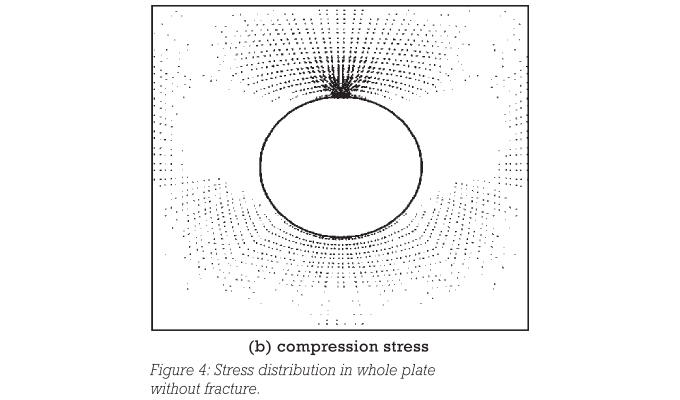
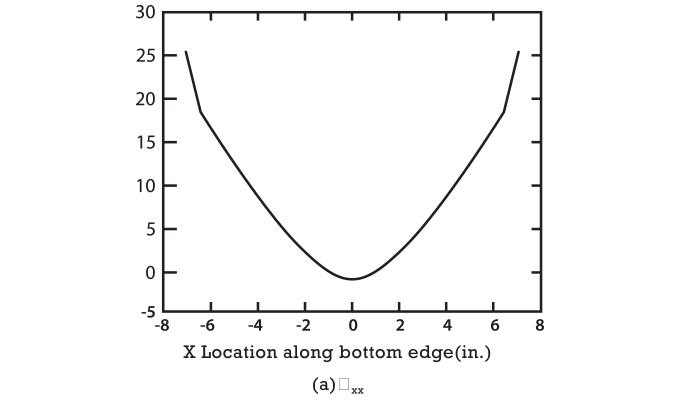
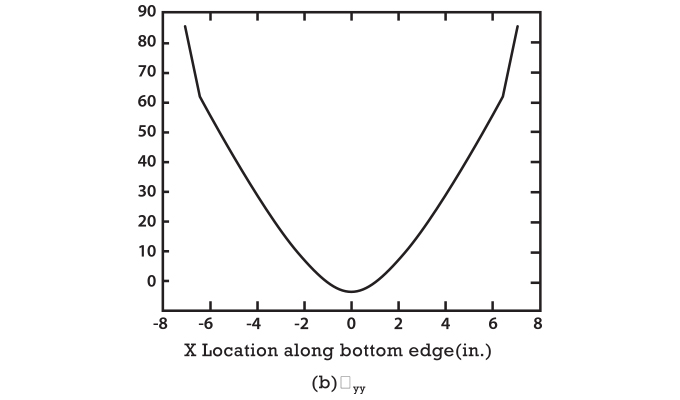
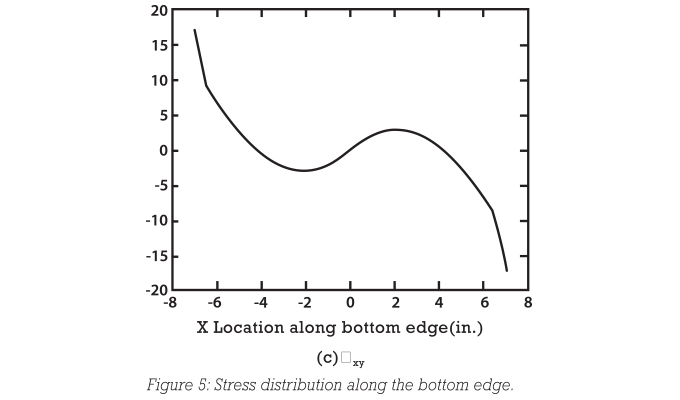
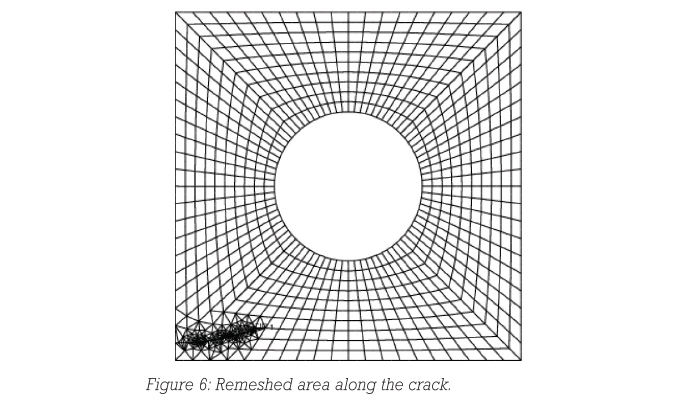
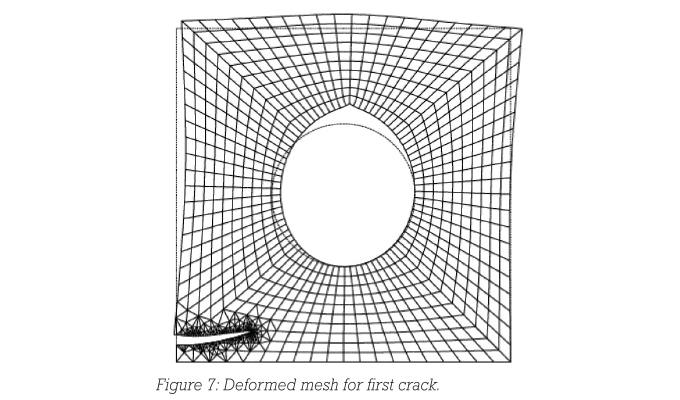

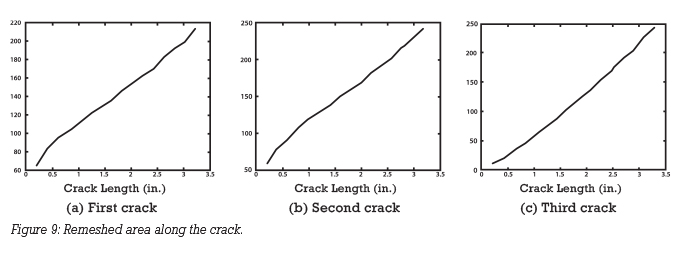
SIMULATION RESULTS
The tensile and compression stress bar distributions for a plate without fracture are displayed in figure 4.
The three sigma distributions along the bottom edge are displayed in figure 5. It can be noticed that the vertical external load will introduce normal stress in the horizontal direction as well as shear stress beside the normal stress in the vertical direction.
The software has the capability to remesh the cracked area every time the fracture is propagated. The mesh scheme after the first crack simulation is finished is displayed in figure 6. Note the refined mesh along the crack.
The deformed mesh for the first crack case is displayed in figure 7. The deformation is amplified to make it distinguishable.
The crack propagation paths for the three crack cases are displayed in figure 8. The first crack, which has the lowest vertical initial location among the three cases, will propagate in an upward direction. The third crack, which has the highest vertical initial location among the three cases, will propagate in a downward direction. However, the second crack, which is initiated at a position between the first and third cracks, will develop in a horizontal direction.
The Mode I stress intensity factor history for the three crack cases is displayed in figure 9. Figure 9 indicates second and third cracks have larger stress intensity factors which suggest faster fracture propagation.
CONCLUSIONS
Under the simulation conditions for this work, the results indicate an edge crack initiated close to the bottom of the plate has lower stress intensity factor than those initiated at a higher position along the plate side edge. An edge crack along the gearbox plate needs to be monitored carefully.
FOR MORE INFORMATION
SpectraQuest, Inc. is a leading developer and manufacturer of complete turn-key systems for training and diagnosis in machine vibration analysis, rotor balancing, and shaft/coupling alignment. System includes machinery fault simulators, interactive training program, data acquisition hardware/software, and accessories. To accelerate the learning and design process SpectraQuest offers a series of interactive software CDs on vibration fundamentals and calculations, signal processing, alignment, and balancing. For more information, visit www.spectraquest.com.
MODERN PUMPING TODAY, July 2021
Did you enjoy this article?
Subscribe to the FREE Digital Edition of Modern Pumping Today Magazine!
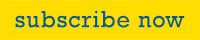