An actual pump reliability improvement issue might serve as a model for tackling sealing issues in modern refineries. You really don’t have to become a mechanical seal expert, but you will have to avail yourself of the right Internet Information Tools, interrogate your in-plant data, and ask the right questions of more than one mechanical seal manufacturer.
This example relates to Crude Vacuum Bottoms (“CVB”) Pumps and explains a North American refinery’s troubled history with seal systems for its 4x6x13 overhung top suction/top discharge pumps. The operating characteristics are somewhat typical for such pumping services: Flowrate between 750 and 800 U.S. gallons per minute, about 650 feet of head, 750 degrees Fahrenheit (399 degrees Celsius), about 5 psia suction pressure, S.G. = 0.77, and 3,560 rpm.
INSTALLATION HISTORY
The pumps were installed in 1972 when the refinery was commissioned; in 2014 they used a dual seal configuration with an API Plan 54 barrier fluid circulation arrangement. You can view or download all (close to 100) API Flush Piping Plans from www.aesseal.com/en/resources/api-plans and similar web pages. Figures 1 and 2 are helpful in this regard; they allow us to visualize modern seals in an API Plan 54 and (figure 2) show an up-to-date pump-around unit close-up.
In 2014 the relatively old dual seal systems on this refinery’s consisted of the following:
- Type ABC / XYZ dual cartridge seals (metal bellows) from manufacturer No. 1.
- Two barrier fluid circulator units with positive displacement pump, pressure- regulating valve, pressure relief valve, and cooling coil in the reservoir, all by manufacturer No. 2.
- Carbon steel piping (1/2-inch) between the circulator unit and pump seal.
- Current barrier fluid is “Compressor 100” lube oil.
The circulator system was put together back in the late 1980’s with little or no design engineering input. To paraphrase the equipment owners, they have in the past and continue to have, numerous failures on this seal system. A majority of the company’s serious seal failure incidents were attributed to stoppages of barrier fluid flow due to line blockage and the ensuing overheating of the inner seal. The refinery also reported instances where the pumps were started without the circulator units running, or where the pressure regulating valves were adjusted incorrectly, resulting in over-pressuring of the inner seal bellows.
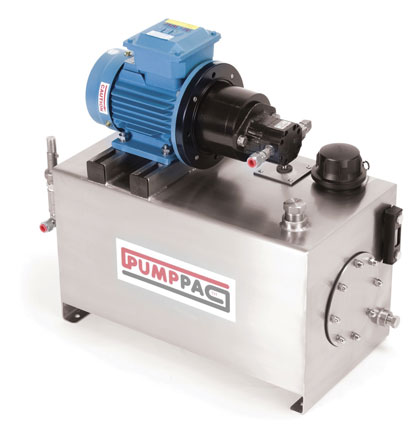
Featured Image: Figure 1-Typical API Plan 54 setup
Above: Figure 2-Barrier fluid pump-around unit used with API Flush Plan 54
The refinery quite accurately labeled these pumps their “worst bad actors” for mechanical seal life. While convinced that the seals themselves were good for the service, they recognized that there were issues with unreliable seal support systems. They now had to deal with two different proposals from manufacturers No.1 and No. 2. Manufacturer No.1 was suggesting installation of a new Plan 54 circulator system designed for the refinery’s application and fitted with short high-pressure hydraulic tubing runs, per the guidelines of API 682. However, manufacturer No.2 recommended installation of a Plan 53A system with a new seal, complete with a pumping ring and seal oil pot pressurized with nitrogen.
The refinery voiced two main concerns with both proposals:
PREFERRED SUPPLIER AGREEMENT
The refinery currently has a Preferred Supplier Agreement with Manufacturer No.1. Fortunately, it was not an exclusive agreement; hence, they also dealt with Manufacturer No. 2 for some applications. “We have some people here in our maintenance organization in favor of the No.2 proposal simply because we have never been able to get our existing system operating reliably and they blame No.1. There are others more in favor of No.1’s proposal because we don’t fault their seal but rather the fact that we’ve tried to make an inherently unreliable support system work with little success, and also because the concern that No.1 raises regarding nitrogen absorption seems appropriate.”
“To get to the point,” notes the originator of the request, “I am interested in what you could advise with respect to reliable seal systems for pumps in CVB service such as ours. We are also looking for a system that is not operator-intensive—simply because many of our failures have been attributed to incorrectly operating the circulator units. An unbiased opinion from someone knowledgeable would go a long way towards helping us reach an agreement on how we should proceed.”
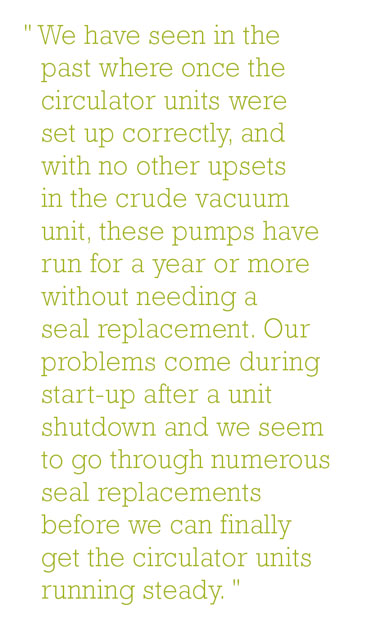
Our answer is probably useful in similar situations encountered by other seal users; so, here it is:
Perhaps we can answer your questions in a manner that’s either not offending any seal manufacturer or, alternatively, offends all involved parties in equal measure. That way, there is reduced suspicion of bias, although we well know it’s not possible to please everyone.
First off, you deserve credit for including lots of relevant data with your questions. Moreover, we commend your company for already working with more than one seal manufacturer, although, for comparison purposes, we have always included a third one. Since you have involved the two largest manufacturers of refinery pump seals, consider adding the third and fourth largest to your data bank. Speak with their Engineering Managers. Chances are these managers have considerable experience in exactly the application you are dealing with. They will have no reluctance to give you suitable client references.
Elaborating on this point and as a matter of recommended standard practice, be sure to ask all four companies to disclose to you where they have supplied seals of the type they recommend for use at your refinery. Of course, these seals must be in successful use in the same medium and at the same temperatures, pressures and –very important–at equal or higher PV (pressure-times-velocity) values. Do not let a seal manufacturer claim this to be proprietary information; it really is not. Incidentally, the various seals involved here are OK. We certainly have no hesitation to accept No.1’s model ABC / XYZ seal face combination as being quite suitable for your high temperature vacuum service.
Realize that API Plan 54 is certainly used elsewhere and is correct here, too. You may be dealing with the proverbial “straw that breaks the camel’s back” by not having the piping or hydraulic tubing runs comply with API 682. But more than the piping is involved here. A 25-year old barrier fluid circulator unit (of the proprietary type mentioned by the refinery) is not current technology. Let Numbers 3 and 4 advise you on their thoroughly engineered, fully packaged and thoughtfully instrumented seal support systems. Bring your support system into compliance with best-in-class practices and consider it money well spent.
After looking at recent and well-documented experiences, you will probably want to stay with Plan 54; the most profitable users have no problem with it and I would certainly stick with it. But realize also that operator vigilance and correct operational and surveillance steps are indispensable for success. All machines devised by humans can be made to fail by operator error. Be sure to use detailed startup checklists!
Finally, question the use of your locally favored lubricant as a barrier fluid. With very few exceptions at best, compressor oils are not heat transfer fluids. Go for a reliable barrier fluid—talk to an experienced oil formulator about an appropriate synthetic lubricant or a much lower viscosity Dowtherm® heat transfer fluid. ISO Viscosity Grade 100 is probably far too viscous.
The underlying point in this story deals with drawing the right conclusions from your own data and realizing that component upgrading is often needed in situations involving old seal support systems. Don’t invest in seal replacement efforts if these same seals are in verified successful use elsewhere. Study the seal support systems available from manufacturers Number 3 and 4 and involve both their Engineering Department and one or two lubricant suppliers. And do not hesitate to consult the right Internet sources—no salesperson will call.
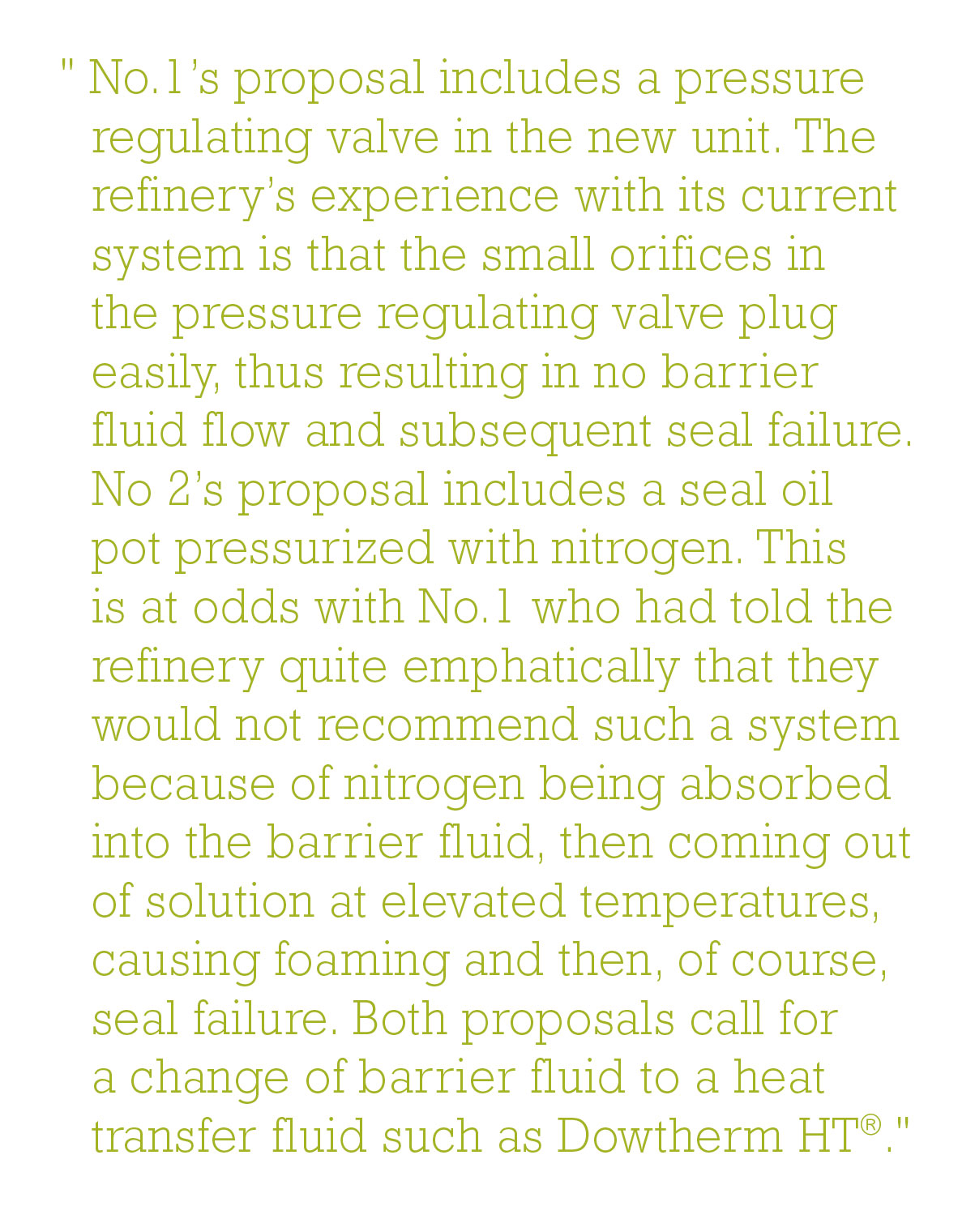
CONSULTING THE INTERNET
The website of the world’s fourth-largest mechanical seal manufacturer (www.aesseal.com) gave a welcome endorsement by way of a simple four-point summary. It started by listing the application parameters of API Flush Plan 54:
- Applications where no leakage to atmosphere can be tolerated; e.g., hazardous, toxic, inflammable.
- For dirty, abrasive or polymerizing products where the medium is unsuitable as a lubricant for inboard seal faces.
- For media with high pressure and / or high temperature and / or high heat generation between faces.
- Wherever Plan 53 A/B/C circulation is insufficient to dissipate heat.
The above mentioned website continued and cautioned with commendable candor; it informed its readers regarding seven additional points of interest:
- Carefully consider the reliability of your barrier fluid source, if a central source is used.
- Expensive system; proper engineering required.
- Circulating system must be pressurized at least 1.5 bar (22 psi) greater that the pressure in the seal chamber.
- Product contamination does occur. Barrier fluid selected should be compatible with the process fluid.
- Always check filter / strainer in the system for any possible blockages.
- Loss of pressure in system can lead to entire barrier liquid contamination.
- Product quality can deteriorate due to barrier fluid contamination.
CONCLUSIONS
We recommended that the oil refinery should be very confident that Plan 54 is the way to proceed. They should make sure that supervisory instrumentation is part of the package. We encouraged them to inform and explain their intentions in a meeting with operating technicians. It’s always wise to let them ask questions. You’ll be surprised at the good outcome of the reliability improvement strategy that this represents.
Keep in mind also that a competent pump rebuild shop (CPRS) has the ability to combine pump repairs with substantial pump upgrading. While probably not needed in connection with this particular CVB pump, there are instances where modifications to the seal environment make economic sense.
We asked the refinery to refer to Subject Category 21 in reference 1. We also re-emphasized that we do not have to be seal experts to select good mechanical seals. All we need to do is ask the right questions, carefully examine vendor-supplied reference data and tabulate the responses. Never let a vendor make you the test location for cheaper substitutes. Vendors 1 through 4 know each other’s products. You, the buyer, are entitled to see full disclosure of all prior experience.
REFERENCE
Bloch, Heinz P.; “Petrochem Machinery Insights,” (2016), Elsevier Publishing, Oxford, UK and Waltham, MA.
For More Information
Heinz P. Bloch, P.E., is one of the world’s most recognized experts in machine reliability and has served as a founding member of the board of the Texas A&M University’s International Pump Users’ Symposium. He is a Life Fellow of the ASME, in addition to having maintained his registration as a Professional Engineer in both New Jersey and Texas for several straight decades. As a consultant, Mr. Bloch is world-renowned and value-adding. He can be contacted at heinzpbloch@gmail.com.
____________________________________________
MODERN PUMPING TODAY, June 2016
Did you enjoy this article?
Subscribe to the FREE Digital Edition of Modern Pumping Today Magazine!
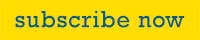