By George Roscoe, Siemens
An arc-flash event—a fiery explosion that can result from short circuits in electrical distribution equipment—is one that facility managers shudder to think about. An arc flash occurs when electrical clearances are reduced or compromised by deteriorating insulation or human error. The arc flash follows an undesired through-air conductive path between two energized conductors or between an energized conductor and ground.
The results are often violent and when a human is in close proximity to the arc flash, serious injury and even death can occur. Reaching an exorbitant temperature of 35,000 degrees Fahrenheit (19,426 degrees Celsius)—four times the temperature on the surface of the sun—an arc flash is a phenomenon to be avoided at all costs. An arc flash can be caused by many things including
- Dropped or misplaced tools
- Faulty installation
- Accidental contact with energized conductors
- Condensation
- Insulation failure
- Corrosion
- Dust
On average, there are five to ten arc-flash incidents per day in the United States resulting in more than 30,000 injuries and 400 deaths annually, with approximately 80 percent of the fatalities due to burns, not shocks. Energy management stakeholders are keenly aware of and compliant with PPE regulations for field workers performing electrical infrastructure tasks within defined proximities, but consistently grapple with the challenge of putting a worker in harm’s way.
At Siemens, we couldn’t agree more. Although exposure to energized equipment is a reality, effective prevention means removing the need for exposure in the first place. From this perspective, even 18 inches is too close.
REMOTE CONTROL WITH SM@RTGEAR MOBILE
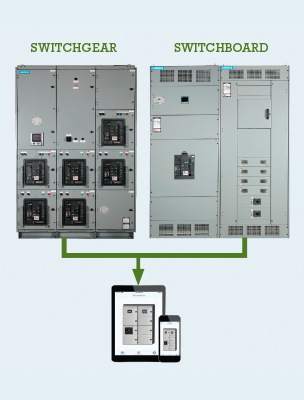
With Sm@rtGear™ Mobile, visualization takes center stage, providing a dashboard-driven interface that can display switchboards or switchgear views. Sm@rtGear Mobile removes workers from the arc-flash hazard zone, enabling remote execution of potentially dangerous procedures, as follows:
Open/Close Breakers
Closing a breaker that has active power on the line side when the equipment is first energized or after equipment maintenance is an operation that has increased arc-flash hazard potential. Sm@rtGear Mobile eliminates manual contact by enabling the operator to close the breaker from outside the arc-flash hazard zone and removes the need for a costly remote control panel.
Activate/De-activate Breaker Maintenance Mode
One of primary drivers for arc-flash incident energy is the clearing time of the upstream protective device. If the upstream protective device has a maintenance mode option, the clearing time can be reduced by lowering the pickup setting and time delay (if applicable) of the upstream protective device. Typically, it is the instantaneous pickup setting that is lowered to below the calculated arc-flash arcing current value.
The maintenance mode option is a standard Sm@rtGear Mobile feature and can be configured and activated from outside the arc-flash hazard boundary. This reduces the arc-flash incident energy exposure for anyone approaching the electrical distribution equipment.
Remotely Monitor and Configure Intelligent Devices
Sm@rtGear Mobile enables operators to remotely monitor and configure breakers, meters, relays, etc., that are embedded in the electrical distribution equipment. Remote monitoring and configuration are an effective way to maintain separation between personnel and energized equipment.
CONCLUSIONS AND RECOMMENDATIONS
Arc-flash safety is highly regulated in terms of both labeling and personal protective equipment (PPE) requirements. Of course, the recommended way to protect workers is to de-energize equipment prior to working on it. When de-energization is not feasible, incorporating guidelines from NFPA and OSHA into an organizational arc-flash study is critical.
The organizational study should include the organization’s actual level of danger and the required PPE for workers based on that level. Electrical systems are dynamic and change over time. Internal changes, such as adding new equipment can affect the level of arc flash energy. A study must be updated every time the system changes. External changes, such as a utility changing transformers or changes at the utility’s closest substation can severely impact the level of arc-flash energy.
Ultimately, the best approach to preventing arc-flash injury is remote operation and monitoring. Sm@rtGear Mobile creates a safer work environment by removing workers from harm’s way through visualization of voltage, current, power, operating conditions, and tripping event diagnostics. By delivering real-time data to maintenance personnel and engineers on their mobile devices, energy stakeholders can be assured that consistent monitoring is taking place and increased safety levels are the result.
FOR MORE INFORMATION
Siemens Corporation is a U.S. subsidiary of Siemens AG, a global powerhouse focusing on the areas of electrification, automation, and digitalization. One of the world’s largest producers of energy-efficient, resource-saving technologies, Siemens is a leading supplier of systems for power generation and transmission. For more information, visit www.usa.siemens.com/indelectricalsafety.
MODERN PUMPING TODAY, January 2021
Did you enjoy this article?
Subscribe to the FREE Digital Edition of Modern Pumping Today Magazine!
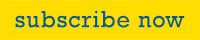