See Part 2 here: Supply Chain Resilience: Part 2 of 3
We’ve spent a large part of this series detailing the challenges to maintaining an effective supply chain. However, in this concluding section, we’ll turn our gaze to the here-and-now as well as the future—not only identifying industries facing supply chain disruptions in the current year but also suggesting a path forward for building greater supply chain resilience.
SIX INDUSTRIES THAT WILL FACE SUPPLY CHAIN DISRUPTIONS IN 2023
1. Automobile
The European automobile industry is facing significant challenges due to the energy crisis in the region. French and German carmakers, including Mercedes, BMW, and Renault, have been among the hardest hit. This is mirrored in Hubs’ survey, which identified rising energy costs as the top concern for the automotive industry. European automakers are also dealing with the closure of steel and aluminum plants, leading to reduced output predictions by hundreds of thousands of vehicles. According to Europe’s metal trade association, 50 percent of the European Union’s aluminum production capacity is now offline due to the ongoing power crisis. It is expected that these challenges will continue to impact the automobile industry through 2023.
2. Aviation and aerospace
Russia’s airspace plays a crucial role in global air travel, serving as a link between Europe and Asia. However, Russian airspace restrictions have forced international carriers to take longer, more expensive detours, reducing the profitability of an industry already struggling in the wake of the COVID-19 pandemic. Furthermore, the ongoing Russia-Ukraine war has disrupted the aircraft manufacturing industry by causing a shortage of titanium, which is a key component in the production of modern commercial aircraft. These events highlight the need for increased supply chain resilience in the aviation industry.
3. Medical
The Ukraine war is leaving a significant impact on the medical industry as well. In its latest survey, Hubs found that raw material shortages were the top concern for the pharmaceutical industry. This is in part due to the rising cost of metals and plastics used in medical devices, which has been exacerbated by the Ukraine war. Furthermore, the U.S. Food and Drug Administration’s clinical trial database indicates that many research sites in Ukraine, which were previously conducting over 250 active trials, are now under threat.
4. Electronics
The Russia-Ukraine conflict has also disrupted the global supply of semiconductor-grade neon, a crucial inert gas essential in chip production. As Ukraine supplies about half the world’s supply of neon gas, electronics companies are facing difficulties in obtaining it. Additionally, the hostilities between Russia and the international community have disrupted the supply of rare metals, leading to reduced manufacturing output for companies such as Apple. The impact of this situation on the electronics industry in 2023 remains uncertain.
5. Food and beverage
Ukraine and Russia are the two major players in the global fertilizer market, making them a crucial part of the global food supply chain. The ongoing conflict between the two countries has disrupted the supply of fertilizers, leading to a sharp rise in global food prices. With farmers struggling to secure the necessary resources to grow crops. This could lead to further food shortages and price increases in 2023.
6. Consumer goods
The ripple effects of supply chain disruptions are further exacerbating the situation. Many consumer companies are struggling to maintain their operations and are facing financial difficulties. Revlon and Hakle have already filed for bankruptcy.
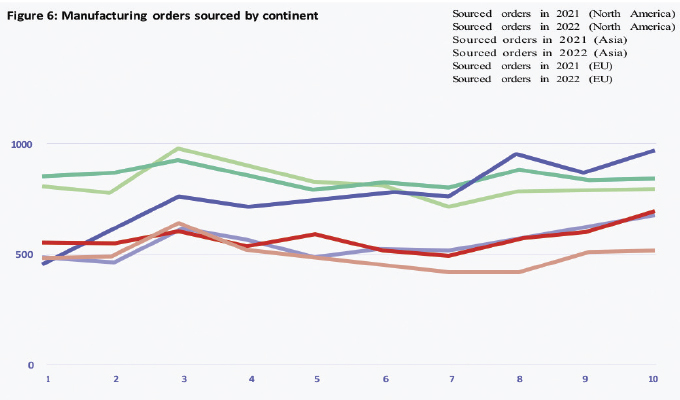
GLOBAL ONLINE MANUFACTURING SUPPLY CAPACITY
China’s supply capacity in 2022 underperformed year-on-year, especially for the first half of the year. Meanwhile, North America experienced a significant increase in manufacturing capacity starting in July. Europe saw the most significant growth, surpassing Asia towards the end of the year. The growth in Europe and North America can likely be attributed to businesses choosing local sourcing and the effects of China’s zero-COVID policy, which led to lockdowns in the country.
FIVE SOLUTIONS FOR STRENGTHENING SUPPLY CHAINS IN 2023
As the complexity of supply chains continues to grow and the number of unforeseeable disruptions increases, it is essential for businesses to develop a risk management strategy to address future disruptions. These strategies can help organizations identify potential risks and vulnerabilities in their supply chain and develop plans to mitigate those risks before they become major problems. Unfortunately, despite facing significant supply chain disruptions in recent years, many organizations remain unprepared for future risks.
Our survey found that approximately 30 percent of respondents had not taken any steps to improve the resilience of their supply chain. This is surprising given that 76.6 percent of surveyed companies experienced disruptions caused by external factors in 2022. It is clear that more needs to be done to ensure that businesses are able to withstand future supply chain disruptions.
For organizations looking to build a resilient supply chain, this chapter focuses on the key elements necessary for preparing for future disruptions, including Black Swan events:
- Automation
- Reserve inventory
- Geographical diversification
- Agile internal processes
- Supply chain monitoring
These solutions were echoed by respondents to our recent survey when they listed measures they thought would be the most effective in reducing future disruptions, shown in figure 7.
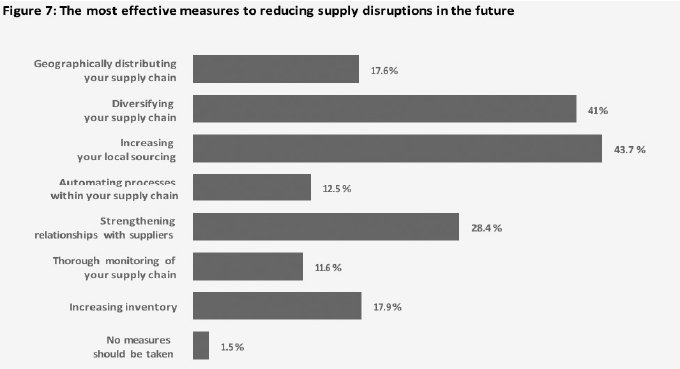
1. Automation
Automation can improve supply chains by increasing productivity and efficiency. These processes can mitigate the effects of certain supply chain risks, particularly those related to labor shortages and lockdowns. With robotic process automation, many repetitive manual tasks can be digitized and streamlined, reducing supply chain complexity and reducing reliance on manual labor. In 2021, 78 percent of organizations were already using RPA technologies, while only 6 percent had no plans to implement it.
Automation is particularly advantageous for its ability to speed up processes that can slow down supply chains if done manually. RFQ and DFM processes can be automated, providing clients with accurate quotes within seconds, rather than days or even weeks. Instead of using traditional, rules-based quoting, Hubs uses machine learning algorithms to provide instant quotes once a customer uploads a CAD file. The process involves comparing the customer’s design to millions of previously manufactured parts. The algorithms use millions of data points collected on part-specific factors such as geometric complexity, volume, material costs, tolerances, secondary processes, and quality control. This is combined with data points on market-specific factors such as global production capacity and the supply and demand of shipping.
Automation across the supply chain also enables businesses to break down silos and streamline the sharing and access of data between supply chain links. Digital process automation (DPA) creates greater efficiency by integrating various platforms used in the supply chain, effectively bridging processes and creating greater transparency and visibility. This in turn empowers suppliers to monitor processes and identify inventory needs as well as supply chain bottlenecks and weaknesses.
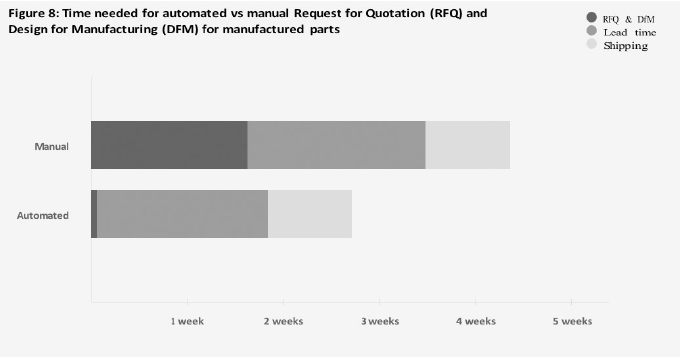
2. Reserve inventory
Though it goes against lean manufacturing strategies, building a reserve inventory can improve supply chain resilience substantially. It effectively creates a buffer so that if or when a link in the supply chain fails, there is enough inventory to keep things up and running while the link is reestablished. It is particularly valuable to have reserve inventory for critical parts and parts that could not easily be sourced from alternative suppliers.
A challenge to the broad adoption of reserve inventory strategies has been cost. However, as AI-driven cost analyses and predictions become more popular, supply chain partners will be able to more accurately predict the probability and cost of supply chain disruptions and weigh those against the costs of reinforcing inventories. In other words, intelligent technologies can make supply chains less reactive and more proactive. Predictive models can also help indicate other changes, such as demand drops or surges, which can help keep production and inventory levels in line with changing consumer trends.
Reserve inventory is an important element in long-term supply chain resilience strategies. Companies that rely on a lean manufacturing approach may benefit from incorporating more risk assessment, predictive models, and inventory buffers into their sourcing strategies.
3. Geographical diversification
Diversifying supply chains is essential to building resilience. Many recent events have demonstrated this: pandemic lockdowns in China brought manufacturing to a standstill at various times between 2020 and 2022; while Europe’s over-reliance on Russia for gas is leading to significant energy shortages. In our latest survey, we found that 41 percent of companies believe diversifying their supply chain is the best way to avoid disruptions in the future.
With a strong, distributed network of suppliers or potential suppliers, supply chains can adapt in the face of regional disruptions and changing geopolitics. If one geographic region goes down, suppliers in another can step up and fill the gap.
Enabling the greatest number of qualified manufacturers possible is a critical step to diversifying supply chains. The more complex a product is to make, the more specialized a manufacturer will have to be, which narrows the pool of possible production partners. By simplifying product designs, whether through consolidation or the elimination of complex features, companies will have access to a greater number of potential suppliers. Building a robust and diverse network of suppliers is a daunting task. However, Hubs’ approach to distributed manufacturing simplifies this process by guaranteeing instant access to vetted suppliers.
Hubs expanded its network of local CNC machine shops in the United States and Europe, allowing users to choose whether they want to source parts locally or globally. With its Hubs Local service, customers can order parts from manufacturers within their custom-clearance borders and enjoy lead times as fast as five days. In a survey conducted by Hubs in 2022, 43.7 percent of participants cited local sourcing as the most effective way to tackle supply chain disruptions in the future. This highlights the importance of having a diverse network of local suppliers in addition to global ones.
4. Agile internal processes
Supply chain resilience is not only about adding flexibility externally—internal processes are also paramount. Startups are typically associated with agile processes, with team members working quickly and dynamically to grow business, but big organizations can also benefit from agility.
By encouraging cross-functionality and greater autonomy across teams, internal processes like product development become faster and more flexible. An agile strategy prioritizes collaboration with clients or stakeholders throughout every stage of development as well as continual improvements based on feedback. This ultimately leads to superior product quality, process transparency, and efficiency, as well as lower risk, since the project is being monitored and evaluated at every step.
With an agile methodology, your internal processes will be more flexible and can seamlessly adapt to market changes. For example, 93 percent of businesses reported that their agile business units fared better than non-agile business units during the pandemic.
Recognizing the importance of collaboration in agile processes, Hubs introduced Hubs for Teams for its customers. It is a collaborative feature on our quote builder that allows you to work with colleagues to source custom parts. This feature enables engineers and purchasers to share and review order details in a single place, making it easier and faster to order parts. This can help improve the efficiency of your team’s workflow and reduce the time it takes to order parts.
5. Supply chain monitoring
In the manufacturing industry, tier-one suppliers are companies that supply parts or materials directly to the original equipment manufacturer (OEM). Tier-two suppliers are vendors that provide parts or materials to tier-one vendors, and tier-three suppliers are companies that provide parts or materials to tier-two. Generally, most businesses only monitor tier one and tier two suppliers as they are considered the most important. However, that’s not ideal because even tier-three suppliers can still play a significant role in the overall supply chain. Delays caused by deeper-tier suppliers can cause disruption throughout your entire supply chain. By closely monitoring suppliers across all tiers, you’ll be able to spot any warning signs well before the consequences of disruption take effect.
However, monitoring your supply chain from the raw materials to the finished product can be a complex and lengthy process. This may explain why this approach was the least popular according to our survey, with only 11.6 percent of respondents selecting thorough monitoring of supply chain as an effective measure to reduce the effects of supply disruptions.
Thankfully, specialized software tools have simplified the supply chain monitoring process. Additionally, companies are exploring emerging technologies such as AI and machine learning for supply chain optimization. While only 13.1 percent of surveyed companies revealed using AI and ML, a resounding 90.9 percent of the users found it to be useful.
- Supply chain mapping to monitor not only tier one and tier two suppliers, but the entire supply chain
- 24/7 supplier monitoring which alerts you to disruptions that may affect your suppliers
- Risk calculation of disruptive events with the potential revenue lost
TRUCK MANUFACTURER AUTOMATES PRODUCTION LINE TO EASE LABOR SHORTAGES
Based in Illinois, the Knapheide Manufacturing Company has been producing commercial vehicles since 1848, starting with wagons and now specializing in a variety of truck bodies and truck beds. Despite country-wide recruitment efforts, the company has struggled to find a suitable number of skilled workers in recent years, particularly welders, to meet its production demand.
In order to overcome this critical labor shortage, the company has invested in robots to further automate its production lines. In 2022, the truck manufacturer initiated a new production line for flatbed truck bodies using robots to feed steel parts into an automated welding process. The process will enable the company to maintain steady, consistent production rates despite labor shortages. Knapheide has also benefited from the integration of digital processes across its business.
Digital design solutions have enabled it to accelerate product development thanks to an agile approach, scale 3D modeling across its products, and facilitate communication and visibility between shop technicians and engineers.
TESLA MITIGATES MICROCHIP SHORTAGES BY REMAINING AGILE
In the face of a global microchip shortage stemming from increased demand and limited supply, automotive company Tesla has been able to mitigate the challenge by remaining agile. The company, whose vehicles are equipped with microchips for various control systems—including its self-driving software—took a two-pronged approach, switching to the use of microcontrollers in some cases and developing special firmware to accommodate the use of microchips from a wider range of suppliers. The ability to remain agile in its own processes and retain much of its automotive design and programming in-house, has significantly reduced the impact of the microchip shortage, which is expected to last for years. Whereas other automotive companies have suffered from significant production delays and even stoppages, Tesla has remained largely on track and is better equipped to deal with any microchip shortages down the line.
CONCLUSION
With the ongoing war in Ukraine creating instability in Europe and causing a global energy crisis, as well as an increasing frequency of cyber-attacks and natural disasters, supply chains face a greater degree of risk than ever. It is therefore critical for organizations to transform and upgrade their supply chain processes to minimize vulnerabilities and achieve greater resilience.
Fortunately, there are many tools and strategies for building a resilient supply chain that organizations can use. Automation technologies, diverse supply networks, and moving away from JIT manufacturing models will help establish a robust, future-proof supply chain that can withstand a wide array of disruptions. Resilience is a must for organizations looking to succeed over the long term and adapt to whatever the future brings.
FOR MORE INFORMATION
Hubs empowers engineers to create revolutionary products by making custom manufacturing more accessible. The company leverages automation to allow fast and affordable access to manufacturing capabilities from all over the world. Hubs started life as the world’s largest peer-to-peer network of 3D printing services, but as it grew with its customers it needed to offer a broader range of capabilities to help their businesses succeed. Today hundreds of manufacturers in the Hubs global network and their customers can order parts in a broad range of materials using multiple manufacturing technologies, and with many secondary processes as well. For more information, visit www.hubs.com.
MODERN PUMPING TODAY, June 2023
Did you enjoy this article?
Subscribe to the FREE Digital Edition of Modern Pumping Today Magazine!