In the first part of this series, we introduced how the vulnerabilities now exposed within lean manufacturing models are threatening supply chain reliability for various sectors. Below, we begin a run-down of these different threats. First, however, we should provide some general context for how these vulnerabilities are viewed by the industry as a whole. In brief, some key differences between the finding of 2021 and 2022 surveys include the following:
- The results of the 2022 survey show that 70 percent of participants have implemented measures to improve their supply chain resilience, compared to 63 percent in 2021. This indicates that companies are increasingly recognizing the importance of preparing for supply chain disruptions.
- In the 2021 survey, 26.8 percent of respondents considered the pandemic as a major supply chain concern. This number has increased significantly in the 2022 survey, with 57 percent of respondents citing it as the second biggest concern.
- 49.4 percent of respondents reported experiencing more raw material shortages in 2022 compared to 2021.
The following sections analyze a range of disruptions that were a major concern in 2022.
GEOPOLITICAL ISSUES
First, the Ukraine war brought global supply chain to its knees. In addition to the tragic loss of lives, the ongoing Russia-Ukraine war has significantly impacted global supply chains. The conflict has disrupted essential air freight and shipping routes, leading to disruptions in the supply of raw materials and finished goods. Unsurprisingly, 45.3 percent of businesses reported being impacted by the war in our 2022 survey.
The war has far-reaching consequences. In 2020, Russia accounted for approximately 29 percent of crude oil and 43 percent of natural gas imports into the European Union. The fresh round of sanctions against Russia has led to a significant increase in energy costs across Europe. As a result, many metal and chemical factories in Europe went dark in 2022. This aligns with the findings of our survey, where 55 percent of respondents expressed concern about the impact of rising energy costs on their businesses, and 55.6 percent of participants were worried about the impact of these costs on Europe’s manufacturing capabilities.
Another issue concerns how the United States-China trade war shows no sign of slowing down. The increased tariffs and trade barriers between the United States and China have disrupted the flow of goods and materials between the two countries. This has made it more expensive and difficult for businesses to import and export goods. As a result, many businesses have had to find alternative suppliers or production locations, disrupting their supply chains and increasing their costs. The uncertainty and instability caused by the trade war have also made it harder for businesses to effectively plan and manage their supply chains.
In what’s now considered a new cold war, the United States recently doubled down on its efforts to deprive China of semiconductor technology. In addition to the organizations, the U.S. government now bars its citizens from supporting the development or production of advanced chips at Chinese facilities.
Additionally, the United States saw more worker strikes in the first half of 2022 than in all of 2021. North of the border, Canada was hit by the truckers’ protest that impaired the supply chains in the country. Across the pond, U.K. port worker strikes strained the supply chains. Spain also faced supply chain issues driven by truck drivers’ strikes. Meanwhile in South Korea, the truckers’ protests disrupted production as well as the supply chain.
Lastly, rising shipping costs hurt the bottom lines of businesses. The steep rise in shipping costs significantly impacted businesses across the globe. In March 2022, it cost an average of nearly $10,000 to ship a 40-foot freight container, almost seven times more than in March 2020.
The higher freight costs contribute to the overall cost of goods and materials, making it more difficult for businesses to compete in the global marketplace. The increased shipping costs are an obstacle for businesses looking to access new markets and eat into profits for established businesses, making supply chain management more challenging.
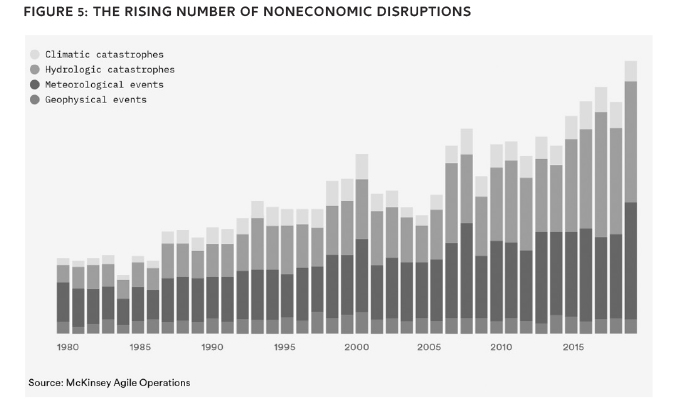
NATURAL DISASTERS
In recent decades, the world has faced more frequent and increasingly severe natural disasters. Hurricanes, floods, fires, and droughts have devastated communities and entire ecosystems. They also have a major impact on supply chains. They can halt or slow production, reroute resources, damage vital infrastructure, and more. Natural disasters cannot themselves be prevented, but their impacts can be mitigated through strategic investments and reinforcing supply chains.
In the year 2021 alone, 401 natural disasters were recorded globally. In the United States, natural disasters cost the economy to the tune of $145 billion in 2021, making it the third costliest year after 2017 and 2005.
In summer 2022, a record-breaking heat wave and drought in China caused disruptions and even closures of shipping routes such as the Yangtze. As a consequence, China experienced an energy crisis. Automakers with facilities in Sichuan—both Toyota and Tesla have operations there—were forced to halt production due to power cuts, causing knock-on effects for the Chinese economy and global automotive supply chains.
Cargo shipments along the Rhine, one of Europe’s key trade routes, were also slowed due to a drought in summer. Delays caused by the drought are expected to slow Germany’s economic growth in 2022 by as much as half a percentage point.
In the United States, Hurricane Ian caused over $60 billion in damages and is expected to cut Florida’s economic growth in Q3 by three percentage points and two percentage points in South Carolina. Flooding in Southeast Australia in October 2022 is expected to cost the country $5 billion in lost economic activity and drive inflation up by 0.1 percentage points.
CYBER SECURITY
As companies become increasingly reliant on digital solutions to accelerate and streamline operations, it becomes more important to invest in robust cybersecurity measures and technologies. Today, cybersecurity threats, such as data breaches and ransomware, pose a real danger to intellectual property (IP) and supply chains. Weak security systems, software vulnerabilities, supplier fraud, and third-party integrations can lead to financial losses and operational disruptions.
In Japan, manufacturers have been the biggest targets for cyberattacks, with data and entire digital systems held for ransom. Toyota was forced to shut down domestic production in Japan after a cyberattack at a major supplier in Q1 2022. The event illustrated how a single supplier undergoing a cyberattack can bring an entire production chain to a standstill.
In 2021, IT solutions company Kesaya was the victim of a supply chain ransomware attack, which in turn compromised as many as 1,500 businesses around the globe. In Sweden, 800 Coop grocery stores were forced to close because the attack had shut down their cash register operating systems.
Cybercrime reportedly cost the US businesses over $6.9 billion in 2021—an increase of $2.7 billion from 2020. The same year, 62 percent of large enterprises in IT, security, development, and DevOps, reported experiencing a software supply chain cyberattack—and 31 percent reported it having a significant or moderate impact.
FIVE SUPPLY CHAINS RISKS TO WATCH
As we move through 2023, many of the supply chain challenges experienced in 2022 will likely stick around or even escalate. To make matters trickier, there may be other disruptive events on the horizon.
- China-Taiwan crisis could worsen the global semiconductor shortage
- Escalating tensions between China and Taiwan have raised concerns about a military conflict in the region. This could destabilize Asia and have serious consequences for global supply chains. Taiwan is a leading producer of semiconductor chips and disruptions to its production capability could further exacerbate the global chip shortage and impede the production of smartphones, computers, vehicles, and electronic appliances. The involvement of other countries, such as the United States and Japan, could further increase trade tensions with China.
- No swift solution in sight for port congestion
- Global shipping delays initially triggered by the COVID-19 pandemic and subsequently aggravated by the Suez Canal blockage and the invasion of Ukraine are expected to continue into 2023. Barring any other unpredictable obstructions or major labor disputes, port congestion and the consequential higher shipping rates are expected to improve gradually as early as Q2 2023.
- Inflation can disrupt supply chains by causing uncertainty in demand
- With inflation at its highest in three decades and the cost of labor, materials, energy, and transportation rising, supply chain costs are also rising. These higher costs are reflected in commodity prices, and as the cost of living increases the more consumer behaviors and demands change. A rigid supply chain can collapse if it can’t adapt to uncertainty in demand. Inflation also comes with other risks, such as labor strikes and a greater chance of bankruptcy, which can disrupt trade networks.
- Surge of COVID cases in China may hamper manufacturing capabilities
- China’s enduring zero-COVID policy and an increase in outbreaks in various cities led to a number of major lockdowns in 2022, which has impacted supply chains. A lockdown in Zhengzhou in November 2022, where Apple operates its biggest iPhone production facility, caused delays for Apple customers around the world. Although the country’s zero-COVID policy is no longer in effect, supply chains are still susceptible to sudden disruptions due to factory closures or capacity reductions.
- New carbon emission regulations may lead to slower movement of goods
- New regulations designed to curb carbon emissions may lead to slowdowns in shipping speeds. As instructed by the International Maritime Organization, cargo ship operators must monitor and decrease emissions in 2023. In order to meet their emission targets, older cargo ships will either have to be upgraded or cruise at 10 percent slower speeds. The decrease in transport speeds is expected to create supply chain lags.
A LOOK AHEAD
In the conclusion to this series, we’ll explore six industries that will face supply chain disruptions in 2023 as well as a closer examination of the global online manufacturing supply capacity. Finally, we’ll conclude by discussing five solutions for strengthening supply chains in 2023 and in the years ahead. Truly, adaptive models of supply chain management will be a constant point of emphasis for any growth-oriented business in the future.
FOR MORE INFORMATION
Hubs empowers engineers to create revolutionary products by making custom manufacturing more accessible. The company leverages automation to allow fast and affordable access to manufacturing capabilities from all over the world. Hubs started life as the world’s largest peer-to-peer network of 3D printing services, but as it grew with its customers it needed to offer a broader range of capabilities to help their businesses succeed. Today hundreds of manufacturers in the Hubs global network and their customers can order parts in a broad range of materials using multiple manufacturing technologies, and with many secondary processes as well. For more information, visit www.hubs.com.
MODERN PUMPING TODAY, May 2023
Did you enjoy this article?
Subscribe to the FREE Digital Edition of Modern Pumping Today Magazine!