Supply networks drive the world’s economies. Not only that, we are dependent on global supply chains for access to everything from food, to medical equipment, to energy. This is why it is more important than ever for organizations to shore up their supply chains and make them more resilient to both predictable and unpredictable disruptions.
Traditionally, profit incentives have favored lean manufacturing models, or just-in-time manufacturing (JIT). While this approach has proven to reduce costs in the short term and boost efficiency, its vulnerabilities have become increasingly evident in the face of global crises, such as the pandemic and war in Ukraine. Where lean supply chains fail, resilient supply chains can adapt, ultimately decreasing the impacts of disruptions and keeping things up and running.
DEFINING SUPPLY CHAIN RESILIENCE
A resilient supply chain is prepared for unforeseen disruptions, able to react and recover fast, and emerge stronger after the event. Though many companies believe supply chain resilience merely implies the ability to manage risk, true resilience enables you to deal with and even benefit from disruptions.
Supply chain resilience does not develop passively, as it’s impossible to plan for every potential risk. Instead, it demands a dedicated, deliberate strategy to strengthen your organization in the face of the unexpected.
Resilience is crucial to the manufacturing industry, as generating revenue relies on adding value at each link of the supply chain, from the raw materials to the finished product. If one of these links becomes broken, or disrupted, value can no longer be added, making a resilient supply chain essential to bringing products to market.
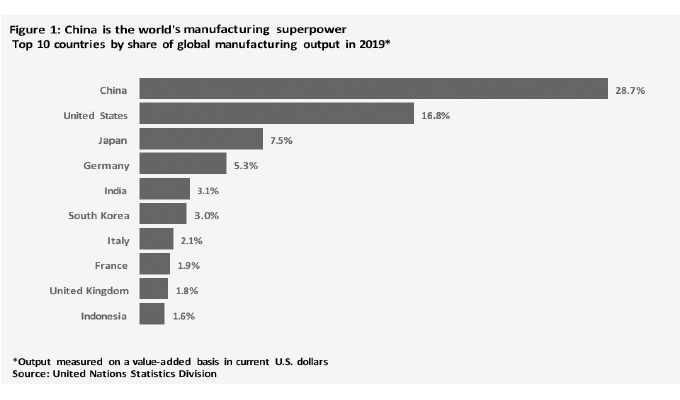
THE RISING NEED FOR RESILIENCE
Supply chain resilience has always been important and necessary in a world driven by global trade, but the need for it has been magnified in recent years by a combination of public health, environmental, and geopolitical concerns. The COVID-19 pandemic showed us how fragile global trade networks and supply chains were in 2020, causing massive disruptions and shortages across various industries as cities locked down and the supply of labor was dramatically impacted.
Today, some of the most pressing stresses on supply chains can be traced to geopolitical events, particularly the ongoing war in Ukraine and escalating tensions between China and Taiwan.
These conflicts pose serious threats to global supply chains due to trade route blockades, economic sanctions, and raw material shortages. Already, we are seeing the early ramifications of trade sanctions with Russia with an energy crisis across Europe. Fuel shortages caused by growing demand in the region are driving up costs. In emerging markets particularly, manufacturing facilities and factories are at risk of increased blackouts, and the higher cost of transport will drive up the cost of commodities.
Other supply chain risks, such as natural disasters, cyberattacks, labor shortages, and inflation, continue to be a concern, further emphasizing the need to think about and plan for a more resilient supply chain. Going by our latest survey, 70 percent of respondents have implemented measures in the past year to improve supply chain resilience, which—while a majority—still leaves many companies more vulnerable to disruptions.
In 2022, businesses small and large succumbed to supply chain troubles. A series of disruptions—including a fire, the pandemic, and a winter storm—led Texas petrochemical producer TCP Group to file for bankruptcy. Logistics challenges, labor shortages, and rising cost of ingredients forced cosmetics company Revlon to file for Chapter 11 bankruptcy. And shortages in wire harnesses, previously manufactured in Ukraine, have led to slowdowns in European automotive production.
There are ample long-term benefits to pursuing a resilient supply chain in lieu of more short-term lean manufacturing. A resilient supply chain anticipates disruptions and mitigates the effects of both predictable and unpredictable events through a combination of strategies. Diverse supply networks, robust cybersecurity, and automated processes are just some of the steps organizations can take to reinforce their supply chain and ensure reliable performance over the long term.
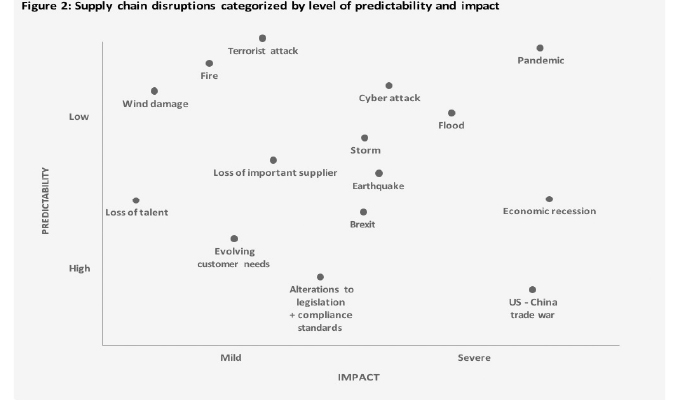
BUILDING SUPPLY CHAIN RESILIENCE IN YOUR ORGANIZATION
Developing a clear strategy is a crucial step in mitigating supply chain disruptions. This series will examine the reasons behind the growing number of supply chain disruptions and discuss approaches for strengthening your organization’s supply chain. The final section will provide a detailed analysis of these approaches and their potential benefits.
- Automation
- Reserve inventory
- Geographical diversification
- Agile internal processes
- Supply chain monitoring
These actions are designed to help you manage risk during the increasing number of supply chain disruptions. After all, it’s not a matter of whether your organization will experience disruption, but rather how often and for how long.
THE GROWTH OF SUPPLY CHAIN DISRUPTIONS, A RISING RISK
Supply chains have become more complex and brittle as a result of globalization.[06] The more complex businesses become, the broader the spectrum of threats. This increased complexity has exposed them to a wider range of threats. In this section, we will explore the level of damage and predictability associated with different types of disruptive events. We will then look at how some supply chain disruptions have become more common, and examine the causes of this increase.
Not all disruptions are created equal. With the rising number of supply chain disruptions, it’s common for businesses to focus their attention on events that are easier to anticipate and control. However, developing supply chain resilience involves examining all variations of risk and tackling each disruption type deliberately and strategically, rather than concentrating on the most predictable risk.
Generally, disruptions can be assessed on the basis of two factors: their predictability, as companies seek to plan long term, and how impactful they are, in terms of the magnitude of the disruption they cause to manufacturing supply chains. Figure 2 summarizes the most common and relevant disruptions that currently threaten supply chains, categorized by their level of predictability and impact.
A robust supply chain strategy should aim to mitigate disruption in each quadrant. It is the most difficult to anticipate the fallout of events that have low predictability and severe impact.
These disruptions are sometimes referred to as “unknown unknowns” or “Black Swans.” They are difficult to foresee and strategize against, and the coronavirus pandemic has shown that these Black Swans demand sufficient attention in order to avoid their devastating aftermath. A resilient supply chain will allow your organization to cope better with a range of different disruptions, both known and unknown.
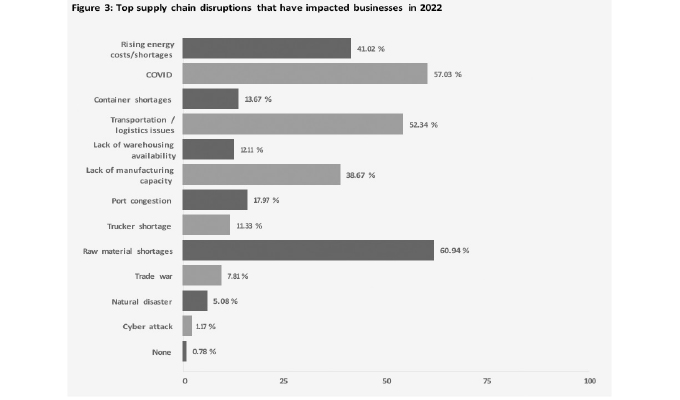
TOP SUPPLY CHAIN CONCERNS
A survey conducted by Hubs in November 2022 with 334 respondents found that 76.6 percent of companies experienced some form of external disruption to their supply chain over the past year. This represents a rise in disruptions compared to the results of surveys conducted in 2020 and 2021. In the 2022 survey, material shortages were the top challenge, affecting 60.9 percent of participants. Likewise, 49.4 percent of respondents reported facing material shortages more often in 2022 compared to 2021.
COVID-19 was the second biggest cause of disruptions, affecting 57 percent of companies in 2022. China’s strict lockdowns, driven by its zero COVID policy, have severely affected the manufacturing output in the world’s manufacturing powerhouse. For example, the output of Apple iPhones is likely to drop by 30 percent due to COVID-related curbs at Foxconn’s factory in Zhengzhou. Other significant concerns among survey respondents included rising energy costs, logistics issues, container shortages, port congestion, natural disasters, and trade wars.
With a military conflict at its door, businesses in Europe experienced widespread supply chain disruptions. In contrast, Asia, home to manufacturing hubs such as China and India, fared better, as shown in figure 4. The automation and robotics industry was the most affected by supply chain disruptions, followed by the electronics and medical corporations.
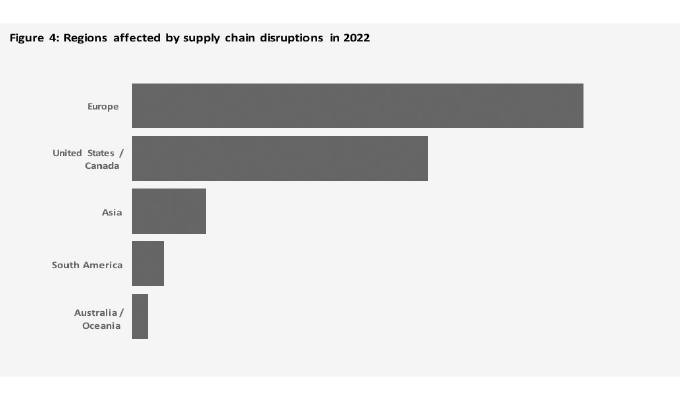
A LOOK AHEAD
In the coming sections of this series, we’ll examine some of the key differences between the finding of 2021 and 2022 surveys with regard to how manufacturers view their supply chain risk. Also, we’ll deep dive into some of the more pressing factors threatening supply chain reliability—geopolitical issues, rising shipping costs, natural disasters, and cyber security. Our series will conclude by shifting focus from the here and now toward the future, naming the top five supply chains risks to watch out for in 2023 as well as six industries that will face supply chain disruptions.
Fortunately, it is not all doom and gloom. We will highlight many tools and strategies for building a resilient supply chain that organizations can use. As you’ll see, resilience is essential if you want your organization to adapt to the future.
FOR MORE INFORMATION
Hubs empowers engineers to create revolutionary products by making custom manufacturing more accessible. The company leverages automation to allow fast and affordable access to manufacturing capabilities from all over the world. Hubs started life as the world’s largest peer-to-peer network of 3D printing services, but as it grew with its customers it needed to offer a broader range of capabilities to help their businesses succeed. Today hundreds of manufacturers in the Hubs global network and their customers can order parts in a broad range of materials using multiple manufacturing technologies, and with many secondary processes as well. For more information, visit www.hubs.com.
MODERN PUMPING TODAY, March 2023
Did you enjoy this article?
Subscribe to the FREE Digital Edition of Modern Pumping Today Magazine!