For such corrosion protection, Wuhan Hengshi Engineering LLC spray applied EonCoat to thirty-eight containers that were put into service for EDC of CNOOC, covering 19,773 square feet total. Over three years later the containers indicate excellent corrosion protection, except for a few areas of coating fall-out due to container collision. These areas were quickly repaired and the units put back into service.
“When equipment like containers are roughly handled to the point where the steel and surrounding CBPC coating are damaged, the coating can typically be repaired by simply spraying a new layer of EonCoat over the old one, provided any chipped edge is abraded to a smooth transition,” says Alpert. “Because of this, equipment can be returned to service in a matter of hours if the company has the spray equipment onsite.”
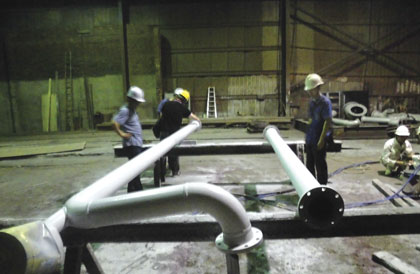
Oil and gas operation managers or corrosion engineers looking to reduce costs are finding additional advantages to CBPC coatings like EonCoat beyond corrosion resistance.
Such coatings consist of two non-hazardous components that do not interact until applied by a standard industrial plural spray system like those commonly used to apply polyurethane foam or polyurea coatings. Since CBPC coatings are inorganic and non-toxic, there are no VOCs, no HAPs, and no odor. This means the non-flammable coatings can be applied safely even in confined spaces.
One of the greatest benefits, however, is quick return to service that minimizes facility downtime. The time saved on an anti-corrosion coating project with the ceramic coating comes both from simplified surface preparation and expedited curing time. With a typical corrosion coating, near white metal blast cleaning (NACE 2 / SSPC-SP 10) is required to prepare the surface. But with the ceramic coating, only a NACE 3 / SSPC-SP 6 commercial blast cleaning is typically necessary.
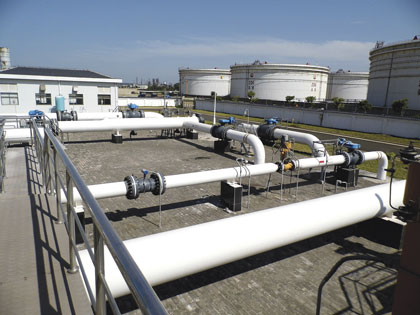
For corrosion protection projects using typical polymer paints such as polyurethanes or epoxies, the cure time may be days or weeks before the next coat of traditional “three part systems” can be applied, depending on the product. The cure time is necessary to allow each coat to achieve its full properties, even though it may feel dry to the touch.
With traditional coatings, extensive surface preparation is required and done a little at a time to avoid surface oxidation, commonly known as ‘flash rust’, which can require re-blasting.
“Typically you need to keep an SP 10 throughout the entire blast operation, cleaning operation, and painting operation with traditional coatings,” says Wesley Newburn, a quality control manager for Mobley Industrial Services, a multi-service specialty contractor serving the chemical, petrochemical, and refining industries. “You may need to rent D-H equipment because humidity above 60 percent will oxidize the surface and require re-blasting.”
In contrast, a corrosion resistant coating for carbon steel utilizing the ceramic coating in a single coat requires almost no curing time. Return to service can be achieved in as little as one hour. This kind of speed in getting an asset producing again can potentially save hundreds of thousands of dollars per day in reduced downtime in oil and gas applications.
“Perhaps the biggest advantage with EonCoat is that there’s no worry about surface prep,” says Newburn. “You can blast the entire surface, then coat it without concern over losing an acceptable blast. There’s no need for D-H equipment because the ceramic coating can be applied when it’s wet or humid. A little surface oxidation makes it adhere better.”
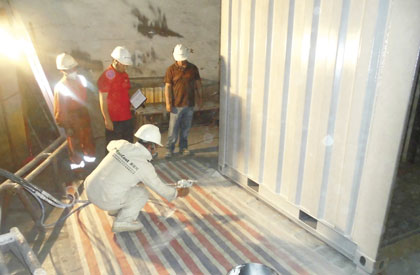
According to Newburn, hydrocarbons are the number one cause of coating delamination at petrochemical facilities. To avoid coating delamination at refineries with traditional coatings, all hydrocarbons such as oil and grease must be found by black light methods, then removed by chloriding until black light passes. This is not required with the ceramic coating because it will not adhere to hydrocarbons, so on surfaces that are not clean the coating will “bubble” on the poorly prepared substrate.
“You can immediately identify and correct poor surface prep during application,” concludes Newburn. “For quality assurance, you can also take the coating’s dry film thickness as early as fifteen minutes after application at 75 degrees Fahrenheit (23.8 degrees Celsius). That means the coating can be performed and corrected at the same time, which makes work quicker and gives a more predictable outcome.”
For More Information
EonCoat is a spray applied industrial coating that prevents rust on carbon steel. EonCoat phosphates the steel it comes in contact with, forming an amorphous magnesium iron phosphate layer. This true alloy—chemically bonded to the steel—is the first line of defense against corrosion. For more information, call 754.222.4919 or visit www.eoncoat.com.
____________________________________________
MODERN PUMPING TODAY, March 2017
Did you enjoy this article?
Subscribe to the FREE Digital Edition of Modern Pumping Today Magazine!
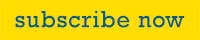