A new jet-mixing pump system has significantly reduced capital, installation, maintenance and energy costs at Moove, the leading global lubricants manufacturer and distributor, in the United Kingdom.
IMPROVED QUALITY AND A BETTER BACK-UP
For a closed-top 13,000-gallon tank used in the manufacturing process of quality lubricating, engine, hydraulic, and gear oils, Moove wanted to trial a set-up that would not only be better economically, but also provide more redundancy.
Ian Lowe, Moove’s manufacturing general manager, explains, “A motor failure on a blender could mean as much as four days impact on production, so it was important for us to take the opportunity to prove a different technology.”
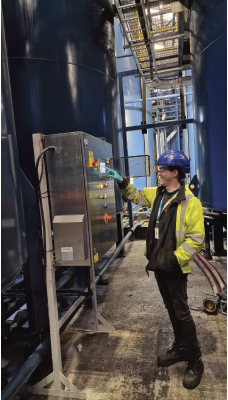
PROVIDING THE BEST OPTION
“The performance of our existing paddle mixers has been good,” Lowe adds, “but Borger were recommended as a company that would work with us to provide a better option; one that could be easily replicated.”
The team at Moove drew up a logic for Borger to examine, outlining their objectives, which ultimately resulted in a pump (plus two nozzles), for a three-bar application with a flow-rate of up to 15,850 gallons per hour. To meet the space requirement at the Gravesend site in Kent, Borger also provided the system as a skid-mounted unit, working closely with Moove to supply a customized control panel with a specially written program.
“The fact that Borger were able to deliver a complete, all-in-one package was a real bonus,” continues Lowe.
“It was also a big advantage to go to Borger for a site test, running different configurations to determine the best operating modes for us. This clearly worked very well, because apart from one very minor tweak, we haven’t had to make any changes since the pump was installed.
SO SIMPLE TO MAINTAIN
“With a 9kW motor (compared to 12kW for the paddle mixers), we are automatically saving on energy, but one of the other main benefits is that the Borger equipment is so simple to look after,” says Lowe. “There’s easy access to the pump-head, and no special tools required. Retrofit to an existing tank is also very straightforward.
“We’re very pleased with solutions provided by Borger that allowed us to achieve the goals of our project.”
FOR MORE INFORMATION
Börger designs, produces, and sells pumps, chopping units, and entry technology for pumping low to highly viscous and abrasive media—including its core component, the patented Rotary Lobe Pump. Börger’s guiding principle has always been to make things better. In the meantime, Börger manufactures many other products. For more information, visit www.boerger.com.
MODERN PUMPING TODAY, April 2024
Did you enjoy this article?
Subscribe to the FREE Digital Edition of Modern Pumping Today Magazine!