By Thomas Chapman, SIFCO ASC
Electroless nickel has many applications, and many are mission critical. But what happens when parts need repair or retouching? Typically, they’re either scrapped and replaced or, if feasible, stripped and replated—a costly and time-consuming process. Selective electroplating offers a faster and more cost-effective solution.
Widely used across multiple industries, nickel and nickel alloy surface coatings create a tough finish that can possess significant wear and anti-corrosion properties. This makes these coatings indispensable for critical applications, especially where harsh conditions are prevalent such as in aerospace, marine, petrochemical, and the oil and gas industries. In particular, nickel-phosphorous plating alloys have grown in popularity due to several unique physicochemical properties.
While Nickel-Phosphorous alloys can be applied electrolytically, they are more commonly applied through an electroless, autocatalytic process due to the unique ability to provide coating uniformity across complex geometries—making them ideal for OEM components. Known as electroless plating, this technique does have some drawbacks though. Namely, this is when you need to repair or replate electroless nickel-phosphorous (ENP) coated parts.
To explain, as ENP plating happens in an immersion tank, replating of already coated areas can cause the part to be out of tolerance due to excess build-up of material. To overcome this, there needs to be either significant—if not cost prohibitive—masking, or risky chemical stripping of the entire part before replating.
There is an alternative to the above though, and that is selective electroplating. This process is focused only on limited, specific surfaces of a part rather than the entire geometry, so the issue of coating uniformity across varying geometries is no longer a concern. Consequently, when it comes to repair, touch-up and refurbishment of ENP coated parts, the selective plating process provides a viable option that can save significant time and cost. Components that might ordinarily be scrapped, can be saved all without compromising the quality or integrity of the part.
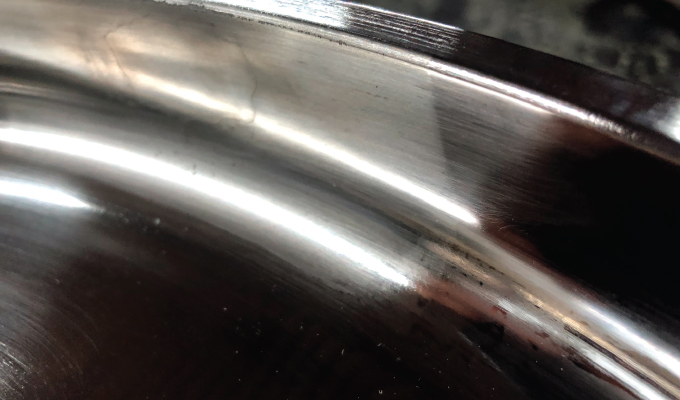
THE TRADITIONAL ENP REPAIR OPTION
The traditional method of retouching or repairing ENP components, involves stripping and replating the entire part; requiring the removal of the component from its setting, immediately creating downtime.
There are other significant drawbacks to the traditional method of ENP repair as well.
The repair of damaged ENP components often involves chemical stripping of the entire part, which can come with the substantial risk of damaging the part beyond repair. While masking is possible, it can be complex and time consuming. Similar issues apply with original equipment manufacturer, where mis-machining after plating can compromise quality, leading to scrap and waste. Equally, even small damage such as minor scratches in transit can result in rejection of the part.
Therefore, while returning components for electroless nickel plating is an option, it inevitably involves more time, cost, and risk. Which is where selective plating such as the SIFCO Process® really come into its own, as many world-class manufacturers have discovered.
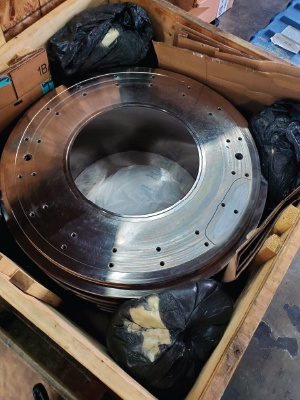
THE ADVANTAGE OF BEING SELECTIVE
With selective plating, the key word is definitely “selective.” Nickel plating that mirrors the performance characteristics of ENP can be applied accurately to small and clearly defined areas without the need to immerse the part in a plating bath. This does away with the need to replate the whole part, and in many cases, the need to disassemble components too. More importantly perhaps, the plating equipment can be taken to the part and applied in situ, eliminating the need to remove it and all the associated costs of downtime and delays.
So how does it work, and how effective is it?
Selective electroplating is actually a long-established technology, originally developed in 1938. Today, the SIFCO Process of selective plating has approvals across multiple industries, including military, aerospace, and energy, and comes with powerful recommendations.
In selective (or brush) plating, an electric current is run through a circuit which is completed when an anode—the plating brush—touches the component to be plated. This allows the deposit to flow onto the negatively charged part. This entire process is done without the need to immerse the part in a traditional plating tank. The deposit can be applied accurately and reliably to very localized areas without the need for post- machining. Deposition rates are also up to 60 times faster than tank plating, further minimizing downtime.
PLATING PORTABILITY
Though it can be automated, selective electroplating is an effective manual process requiring minimal equipment—typically a portable kit which can be easily carried to facilitate the spot retouching.
Apart from portability and being able to repair specific areas, the plating quality of the SIFCO Process® is comparable to tank plating in terms of performance, hardness and adhesion. Just like traditional tank plating methods, selective plating forms a metallurgical bond to the base material. The selective plating process can also deliver good results on aluminum substrates that may require ENP touchup.
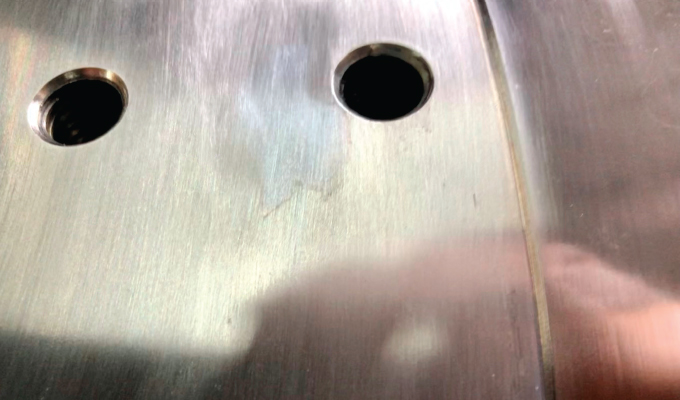
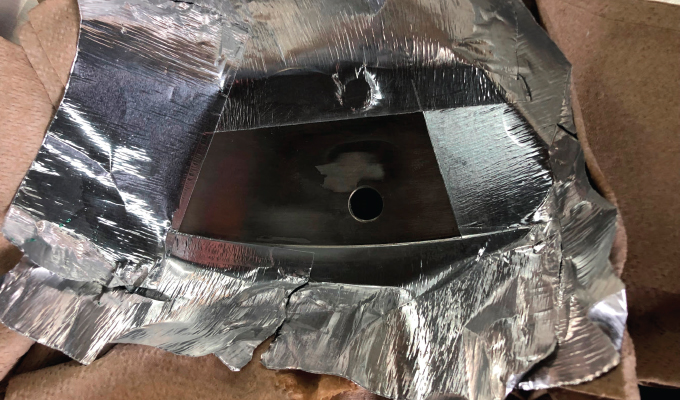
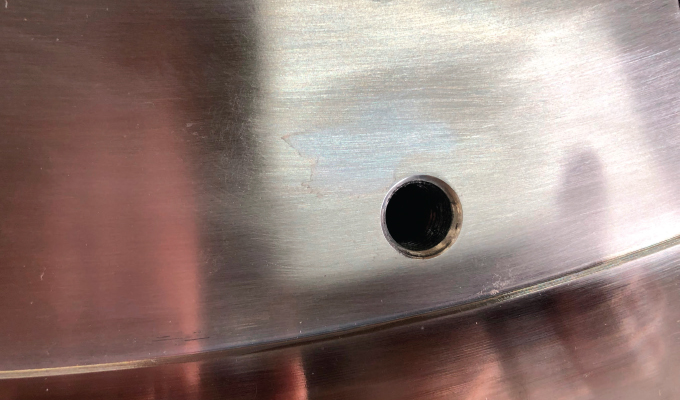
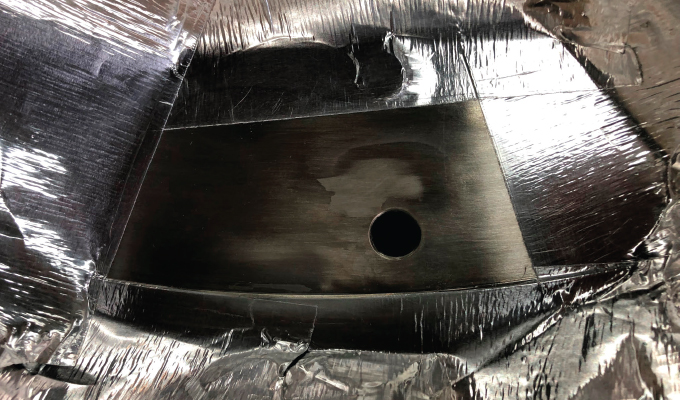
AN ELECTROLYTIC NICKEL-PHOSPHORUS OPTION FOR SELECTIVE REPAIR
SIFCO ASC has a specially developed coating—5709 nickel-phosphorous—the same plating alloy used in electroless nickel plating. What is unique about 5709 nickel-phosphorous is the ability of the plating operator to adjust plating parameters to apply different levels of phosphorus content depending on the specific application. Thus, with one plating solution, both low and high phosphorous type coatings can be applied depending on the desired surface characteristics. When applied with a high phosphorous content, the coating structure changes from crystalline to amorphous, resulting in a coating with superb corrosion resistance properties.
Finally, the SIFCO Process offers a range of environmentally safe alternatives. It also uses less energy and produces less effluent waste than tank plating, and brings considerable environmental benefits too.
For operations committed to in-house resources, the process can also be automated to deliver consistent application during both pre-treatment and plating. Data logging and traceability can be added to the list of benefits.
AN OPTIMAL SOLUTION
Electroless nickel plating is an established, effective and necessary process, improving the corrosion resistance of components across virtually all industry sectors. However, it is not an ideal solution for repairs and retouching, largely because for repairs, it requires the removal and replating of the whole component. This, in turn, adds time and cost to operations.
As a tried-and-tested alternative, selective plating with the SIFCO Process delivers ease, speed, and convenience. Most importantly, it creates a tough, corrosion resistant finish on even the smallest areas, preserving the function and integrity of the component while minimizing downtime and costs.
FOR MORE INFORMATION
Thomas Chapman is Northeast sales manager at SIFCO ASC. A Quaker Houghton company, SIFCO ASC provides practical, cost-effective selective brush plating solutions to improve part performance and reduce manufacturing costs through corrosion protection, increased wear resistance, increased hardness, improved conductivity, anti-galling, or slip. SIFCO ASC surface enhancement technologies and brush plating services have been used for over fifty years on both OEM components and on parts requiring refurbishment in the aerospace, oil and gas, general industry, and power generation sectors. For more information, visit www.sifcoasc.com.
MODERN PUMPING TODAY, September 2021
Did you enjoy this article?
Subscribe to the FREE Digital Edition of Modern Pumping Today Magazine!
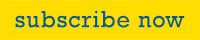