Alleged hygiene failings discovered in the poultry industry thanks to an investigative report in The Guardian newspaper have seen three of the United Kingdom’s leading supermarkets launch emergency investigations into their chicken supplies and have also brought pump specification and pump maintenance firmly into the spotlight.
Landia, whose non-clogging chopper pumps are installed at numerous poultry processors, abattoirs, farms, and biogas plants, says that the shocking evidence shows just how quickly standards can deteriorate when pumps fail. Therefore, operators need to ensure their pumps are properly matched to their applications and are responsive to maintenance needs.
PLANNING IS CRITICAL
“We don’t yet live in a world of course where pumps never break down, but any well-run abattoir will be acutely aware of the sometimes dire consequences of wastewater backing up—and will have already have a preventative maintenance program in place,” says Landia’s Paul Davies.
“With some larger abattoirs running lines at a rate of almost 200 birds per minute, or well over 10,000 per hour, downtime can be disastrous,” Davies adds. “In too many places the production line is being pushed to absolute breaking point in order to meet the deadlines of their supermarket customers, but all the same, a decent sturdy chopper pump that doesn’t allow solids to clog it up, backed by a regular servicing, can make a world of difference.”
THE CONSEQUENCES OF PUMP FAILURE
At one factory, The Guardian discovered offal piled up during a pump system failure, with breakdowns leading to high-risk material—feathers, guts, and offal—piling up for hours.
Another breakdown led to the water in scald tanks at the same site not being cleaned for three days, so that around 250,000 birds passed through dirty water after slaughter.
During The Guardian’s five-month investigation, workers also witnessed a breakdown (which they said are repeated events) where it was the pump feeding the flume of water that is supposed to carry feathers away from the plucking machines.
The evidence prompted Tesco, Sainsbury’s, and Marks & Spencer—three of the United Kingdom’s largest supermarket chains—to launch emergency investigations into their chicken suppliers.
The concern centers on the campylobacter bacteria, which at the last count was present in two-thirds of British fresh chicken sold in the United Kingdom. Although the bug is killed by thorough cooking, around 280,000 people in the United Kingdom are currently made ill each year by it and 100 people are thought to die. Contamination rates are known to have increased in the past decade.
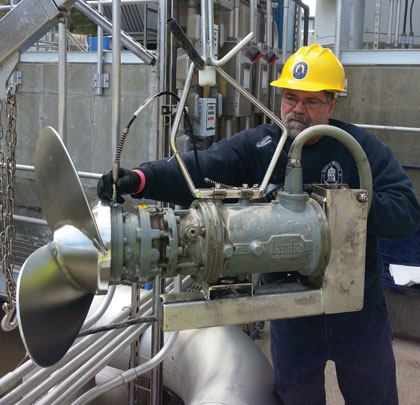
Landia pumps working and production on time
OPTIMAL PUMP PERFORMANCE EXPANDS OPPORTUNITY
However, careful pump selection and routine maintenance are not limitations on a pump’s use—far from it. In fact, when pumps are maintained to performance standards, creative options are available for pump users seeking innovative solutions. For example, a water pollution control facility (WPCF) in Connecticut is benefitting from reduced downtime, thanks to pumps, mixers, and significant back-up service from Landia.
PUMP AND MIXER TEAMWORK PAYS OFF
Serving over 11,000 residents, the facility at Stafford, Connecticut, underwent an upgrade in January 2011, when six 1.8 horsepower Landia mixers were installed in the anoxic tanks as part of a new activated sludge process. Three 2.4 horsepower Axial flow pumps, designed and manufactured by Landia, were also introduced for the aeration basins, from where they return nitrified mixed liquor back to the anoxic tanks for denitrification.
In an effort to improve their maintenance program and equipment service life, plant personnel at Stafford contacted Landia for assistance.
“When we made Landia aware of our need to reduce maintenance costs, they responded in a very timely manner,” reports Rick Hartenstein, chief operator at the WPCF. “Some companies are only interested in helping when they have secured a service contract, but Landia sent one of their skilled engineers to show our maintenance staff how to best look after the pumps and mixers for our benefit, which in turn means we provide a better service to the people of Stafford. Since then, we’ve become more efficient, had no downtime, saved money and had no hassle. It is refreshing to work with a company who has such high standards for customer care.”

Pump system failure
POSITIVE RESULTS FROM PROPER MAINTENANCE
Kenneth E. Jacobs Jr., the Landia service manager who visited the WPCF, adds, “It was a pleasure working with the team at Stafford. We looked at best practice servicing methods, including mechanical seals, electrical testing, oil changes and replacement of oil sealing rings to enhance the performance and longevity of the pumps and mixers at the facility.”
Treated wastewater from Stafford WPCF is discharged into the Willimantic River. The collection system, which has over 2000 hook-ups, encompasses approximately 22 miles (35.4 kilometers) of the town and utilizes four pumping stations. Covering 58 square miles (150.2 square kilometers), Stafford is the third largest town (land area) in Connecticut.
In addition to the equipment at Stafford WPCF, Landia has well over 2000 pumps and mixers installed in activated sludge processes across the United States, many of which have been in continuous operation for more than twenty years.
About the Author
Art Savage is regional sales manager for Landia, Inc. For more information Landia’s range of applications, call 919.466.0603, email info@landiainc.com, or visit www.landiainc.com.
MODERN PUMPING TODAY, October 2014
Did you enjoy this article?
Subscribe to the FREE Digital Edition of Modern Pumping Today Magazine!
