All-Flo’s A200 pump reduces energy costs, improves performance | Part 2 in a 4-part series.
Traditional air operated double diaphragm pumps (AODDP) operate in a very specific way. Compressed air enters the pump through the main air valve and the main air valve spool, in an alternating fashion, directs compressed air behind the left and right diaphragm, exhausting the air appropriately.
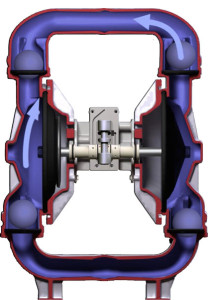
The left and right diaphragms are connected via a rod that runs through the center of the pump and therefore their movements are interconnected. As the air pressurizes behind the right diaphragm, the right diaphragm inflates outward to the right pulling the rod, causing the left diaphragm to move inward and to the right.
Illustrated in figure 3, as the left diaphragm moves inward, the movement creates suction and fluid is drawn into the pump chamber from the bottom suction port. Alternatively, as the diaphragm moves outward, fluid is discharged out of the top discharge side of the pump.
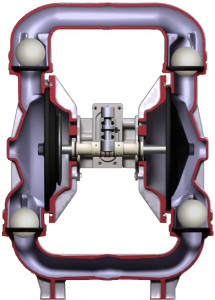
In figure 4, you can see that balls within the AODDP act as check valves, ensuring proper suction and discharge of the process fluid.
During this process of alternating suction and discharge, air is consumed and transformed into the mechanical energy of the diaphragm movement and exhausted from the air discharge port of the AODDP. As shown in the earlier example, this can sometimes be costly in terms of air consumption and the resulting operating cost of a traditional AODDP.
AN ENERGY EFFICIENT SOLUTION
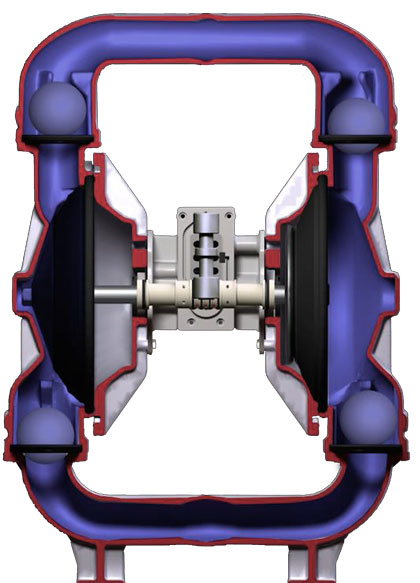
The rising cost of energy and its impact on standard AODDP operation costs were the driving factors behind the development of All-Flo’s new line of pumps, designed to reduce operation costs for its users. After three years of research and development, All-Flo has released the A200 pump, using less than half of the compressed air of previous models and increasing overall performance in both suction lift and flow-rate.
To reduce the air consumption and increase performance, All-Flo made several modifications to its original AODDP design:
- Significant reduction and optimization of “dead space” on both the liquid and air side of the diaphragm
- Adjusting the timing of the shift point of the main air valve, allowing for a longer operating period in a more efficient point of the air-valve’s cycle
OPTIMIZING DEAD SPACE
In Figure 5, the diaphragm on the left is shown fully extended. Optimizing the dead space results in higher liquid displacement per stroke and a higher suction lift, that translates into higher self-priming ability. As a result, the dry lift of this design improvement resulted in an increase from 13 feet (3.96 meters) H20 to 24.4 feet (7.44 meters) H20. The higher displacement per stroke led to a maximum flow-rate of 190 gallons (719.23 liters) per minute, a large improvement compared to the previous limit of 165 gallons (624.59 liters) per minute. By optimizing the dead space on the airside of the pump, the new design boasted higher air efficiencies, allowing the diaphragm to be displaced earlier in the air-valve cycle.
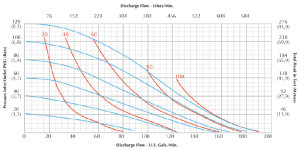
IMPROVED AIR-VALVE TIMING
The timing of the shift point of the air-valve also plays a key role in the overall efficiency of the pump. All-Flo’s earlier design was substantially less efficient near the end of the diaphragm stroke than it was at the beginning, as it continued to consume air while displacing very little liquid.
By changing the pump’s timing so that the valve would shift earlier in the cycle, the pump had a negligible loss in liquid displacement and a substantial decrease in air consumption, resulting in a dramatic increase in the pump’s overall efficiency.
During the design process, the pump’s timing was optimized, resulting in a final production design which consumed 45 percent less air than its predecessor.
THE A200 PERFORMANCE CURVE
Using the same approach to reading a pump curve as in part 1 of this series, figure 6 shows how the All-Flo A200 pump compares to the average AODDP used in the earlier example.
Reading the chart from the same point, 80PSI inlet and 20PSI discharge, you can see that the pump yields 125 gallons (473.18 liters) per minute at a cost of 65 SCFM.
With this information, we can calculate the operating cost for the A200 pump, as we did in the earlier example, for an eight-hour day.
Based on these calculations and the assumed operating conditions, we can see that the All-Flo A200 pump costs $0.85 to operate for one hour. If the A200 pump was to operate for eight hours per day, 5 days a week, it would cost $1,768 per year to operate.
On an annual basis the results are dramatic—the new design consumes 45 percent less air than the previous model, resulting in a savings of approximately $1400 per year for each pump. With the A200 pumps, if a factory ran 100 AODDPs for eight hours each day, the user would save more than $140,000 annually.
THE A200 DIFFERENCE
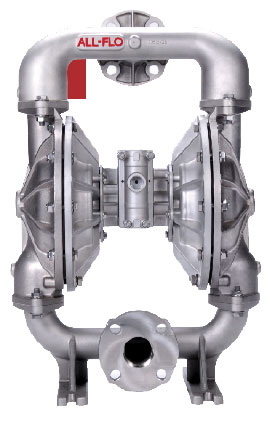
Energy is the engine behind all of our economic activity, but when confronted with rising energy costs, customers are left with few choices—raise prices or accept a lower profit in order to remain competitive. However, with AODDPs, users have a third option, improving manufacturing techniques and equipment with a new All-Flo A200.
In subsequent articles we will evaluate air consumption of the new A200 model compared to typical other AODDPs as well as highlight some real world applications where improvements in overall air-efficiency yield better bottom lines for those involved.
■ ■ ■
ABOUT THE AUTHOR
Paul McGarry is the All-Flo sales and marketing manager for North America. To learn more, visit www.all-flo.com, and www.aoddpumpefficiency.com.
MODERN PUMPING TODAY, MAY 2014
Did you enjoy this article?
Subscribe to the FREE Digital Edition of Modern Pumping Today Magazine!
