All-Flo’s A200 pump reduces energy costs, improves performance | Part 3 in a 4-part series.
All air-operated double diaphragm pumps (AODDPs) are not created equal. In fact, significant differences in performance, efficiency, and total cost of ownership exist from one manufacturer’s pump to another. Sometimes these differences are so pronounced that they can add up to losses of hundreds of thousands of dollars every year.
If AODDPs were truly the interchangeable commodity products as some believe, would this be the case? The answer is an emphatic no. There is still room for innovation and improvement in the field of AODDPs. One example of where these ideas have found a home—as we’ve seen in the first two installments of this series—is All-Flo’s A200 pump. The A200 stands apart from other AODDPs on the market. As you read this month’s article, the importance of choosing the right pump for your application will become abundantly clear.
A QUICK RECAP
Before we move on, let’s take a moment to look back at how we got here. The first two articles in this series covered how AODDPs work, how to read performance curves, and how to calculate pump operating costs. We also delved into how All-Flo’s new A200 model drastically improved upon its predecessor and has raised the bar for performance and efficiency across the entire industry.
Please reference the prior installments if you need a refresher, but for your convenience, here’s a reminder of the primary takeaway: All-Flo seriously advanced pump performance and efficiency with the A200. This was achieved by reducing and optimizing dead space on the liquid and air sides of the diaphragms and by improving the timing of the main air valve.
SETTING THE COMPARISON CRITERIA
To get a fair apples-to-apples comparison underway, we will start with some specific assumptions. First, the application scenario. For our purposes, we are going to suppose that the AODDP being evaluated needs to transfer 8000 gallons (30,283.29 liters) of liquid every hour, for eight hours a day, over the course of a year. It will do this with a liquid discharge pressure of 20 PSI. Second, 8000 gallons (30,283.29 liters) per hour is equivalent to a flow rate of 133 gallons (503.46 liters) per minute. This means that the pump in our example operates at 133 gallons (503.46 liters) per minute against a discharge pressure of 20 PSI.
Using the performance curve shown in figure 7, we can find out how much air is required to run the pump. Simply find 133 gallons (503.46 liters) per minute on the horizontal axis and then look to see where that value intersects with 20 PSI on the vertical axis. You can see that they meet between the two blue lines that represent 80 and 100 PSI. This means that the required operating pressure is around 90 PSI. The intersection point also lies between the red lines that represent 60 and 80 SCFM. This tells us that we can estimate the air consumed by the pump to be 70 SCFM.
WHAT DOES THIS MEAN?
To put it all together to calculate operating costs, we use the following equations:
As you can see, in our example, this particular pump can transfer 8000 gallons (30,283.29 liters) per hour at a cost of $0.91 per hour. This makes the extended annual cost somewhere in the neighborhood of $1900.
ONE OF THESE PUMPS IS NOT LIKE THE OTHERS
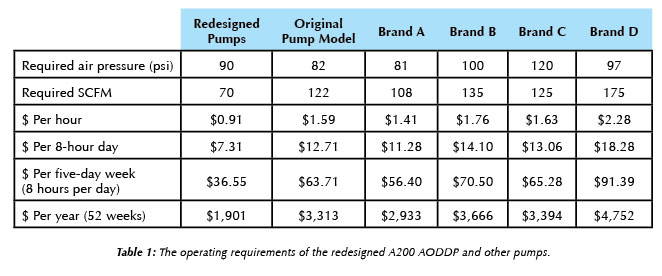
The impressive pump performance used in the previous example belongs to All-Flo’s A200. In Table 1, we’ve put those numbers (found under A200 Redesigned Pumps) up against the operating costs of the A200’s own All-Flo predecessor (Legacy Pump Model) as well as AODDPs currently sold by other manufacturers. As you can see, the A200 beats the competition in every single category.
Sure, the differences in operating costs demonstrated here are stark, but remember—this is just for one pump. Some All-Flo customers run four hundred pumps or more at any given time, so imagine extending these savings across an entire operation! You don’t have to be a mathematician to understand that those kinds of numbers can dramatically impact a company’s bottom line. That’s why it’s so important to know exactly what you’re getting into—exactly what you’re getting for your AODDP investment—before you make a purchasing decision. The numbers don’t lie.
COMING UP
In our next, and final, article in this series, we will discuss how to make sure you get the ideal AODDP for your needs. We’ll clue you in on what to look for when evaluating AODDP performance and give you the right questions to ask pump manufacturers.
■ ■ ■
ABOUT THE AUTHOR
Paul McGarry is the All-Flo sales and marketing manager for North America. To learn more, visit www.all-flo.com, and www.aoddpumpefficiency.com.
MODERN PUMPING TODAY, MAY 2014
Did you enjoy this article?
Subscribe to the FREE Digital Edition of Modern Pumping Today Magazine!
