In order to understand centrifugal pump leakage, it’s important to first understand the basic operation of a centrifugal pump. As the flow enters through the impeller eye of the pump and up the impeller vanes, the fluid is at a lower pressure and low velocity. When the flow passes through the volute, the pressure increases and the velocity increases. The flow then exits through the discharge, at which point the pressure is high but the velocity slows. The flow that goes into the pump has to go out of the pump. The pump imparts head (or pressure), which means it increases the energy of the pump fluid.
Certain component failures of a centrifugal pump, such as coupling, hydraulic, static joints, and bearings, will cause the whole system to fail, but approximately sixty-nine percent of all pump failures result from the sealing device malfunctioning.
THE NEED FOR MECHANICAL SEALS
A mechanical seal is a device that is used to control leakage between a rotating shaft and a liquid- or gas-filled vessel. Its main responsibility is to control leakage. All seals leak—they have to in order to maintain a fluid film over the entire mechanical seal face. The leakage that comes out the atmospheric side is fairly low; the leakage in a Hydrocarbon, for example, is measured by a VOC meter in parts/million.
Before mechanical seals were developed, engineers typically sealed a pump with mechanical packing. Mechanical packing, a fibrous material usually impregnated with a lubricant such as graphite, was cut into sections and stuffed down what was called a “stuffing box.” A packing gland was then added to the backside in order to pack everything down. Since the packing is in direct contact with the shaft, it requires lubrication, but will still rob horsepower.
Usually a “lantern ring” allows flush water to be applied to the packing. That water, necessary to lubricate and cool the shaft, will leak either into the process or into the atmosphere. Depending on your application, you may need to:
- direct the flush water away from the process to avoid contamination.
- prevent the flush water from collecting on the floor (overspray), which is both an OSHA concern and a housekeeping concern.
- protect the bearing box from flush water, which can contaminate the oil and eventually lead to a bearing failure.
As with every pump, you’ll want to test your pump to discover the annual costs it requires to run. A packing pump may be affordable to install and maintain, but if you calculate how many gallons of water it consumes per minute or per year, you may be surprised by the cost. A mechanical seal pump could potentially save you a lot of annual costs.
Given the general geometry of a mechanical seal, anywhere that there’s a gasket or an o-ring, there ensues a potential leak point:
- An eroded, worn, or fretted dynamic o-ring (or gasket) as the mechanical seal moves.
- Dirt or contamination in between the mechanical seals.
- An off-design operation within the mechanical seals.
THE FIVE TYPES OF SEALING DEVICE FAILURES
If the centrifugal pump exhibits an uncontrolled leak, you must thoroughly check all potential causes to determine if you need repairs or a new installation.
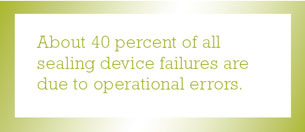
1. Operational Failures
Neglecting the Best Efficiency Point: Are you operating the pump at the Best Efficiency Point (BEP) on a performance curve? Each pump is designed with a specific Efficiency Point. When you operate the pump outside that region, you create problems with the flow that cause the system to fail.
Insufficient Net Positive Suction Head (NPSH): If you don’t have enough suction head to your pump, the rotating assembly can become unstable, cause cavitation, and result in a seal failure.
Operating Dead-Headed: If you set the control valve too low to throttle the pump, you can choke the flow. Choked flow causes recirculation within the pump, which generates heat and promotes a seal failure.
Dry Running & Improper Venting of Seal: A vertical pump is the most susceptible since the mechanical seal is positioned on top. If you have improper venting, air can get trapped around the seal and won’t be able to evacuate the stuffing box. The mechanical seal will soon fail if the pump continues to run in this condition.
Low Vapor Margin: These are flashing fluids; hot hydrocarbons will flash once exposed to atmospheric conditions. As the fluid film passes across the mechanical seal, it can flash at the atmospheric side and cause a failure. This failure often happens with boiler feed systems—hot water at 250-280ºF flash with the pressure drop across the seal faces.
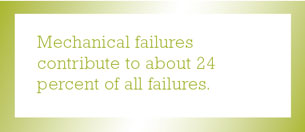
2. Mechanical Failures
Shaft misalignment, coupling imbalance, and impeller imbalance can all contribute to mechanical seal failures. In addition, after the pump is installed, if you have misaligned pipes bolted to it, you will impart a lot of strain on the pump. You also need to avoid a bad base: Is the base secure? Is it grouted properly? Do you have a soft foot? Is it bolted correctly? And last, check the bearings. If the tolerance of the bearings wears thin, the shafts will move and cause vibrations in the pump.
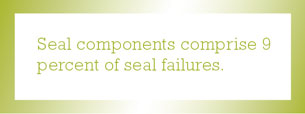
3. Seal Component Failures
Do you have a good tribological (the study of friction) pair? Have you chosen the correct facing combinations? What about the seal face material quality? Are your materials appropriate for your specific application? Have you selected the proper secondary seals, such as gaskets and o-rings, that are prepared for chemical and heat attacks? Your springs should not be clogged or your bellows corroded. Last, keep an eye out for face distortions from pressure or heat, since a mechanical seal under great pressure will actually bow, and the skewed profile can cause a leak.
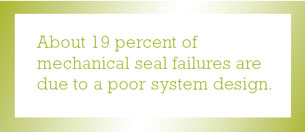
4. System Design Failures
You need a proper seal flush arrangement, along with sufficient cooling. Dual systems have barrier fluids; the auxiliary seal pot needs to be in the right location, with the correct instrumentation and piping. You need to take the Length of Straight Pipe at Suction into account—some older pump systems that often came as a packaged skid include a 90º elbow at suction right before the flow enters the impeller eye. The elbow causes a turbulent flow that creates instabilities in the rotating assembly. All the suction/discharge and bypass piping needs to be engineered correctly as well, especially if some pipes have been repaired at some point over the years.
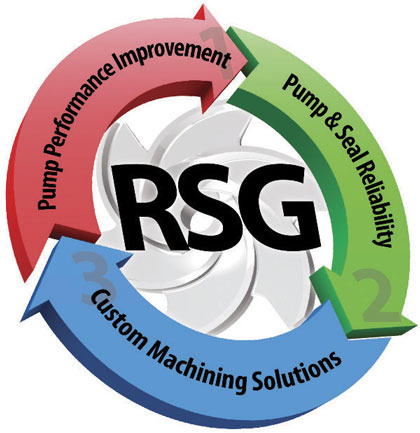
5. Everything Else
Other miscellaneous factors account for only about 8 percent of all failures. For example, auxiliary systems are sometimes required to provide an acceptable operating environment for a mechanical seal. For reference to dual systems, you need an auxiliary fluid to act as a barrier that prevents contamination or process fluid from spilling into the environment. However, for most users, addressing one of the first four categories will hold the solution they need.
CONCLUSION
Mechanical seals are a major factor in rotating equipment reliability. They’re responsible for leaks and failures of the system, but they also indicate problems that would eventually cause serious damage down the road. Seal reliability is greatly affected by the seal design and the operating environment.
For More Information
Frank Rotello is mechanical seal reliability engineer for Cummins-Wagner. Cummins-Wagner Co., Inc. is a distributor for industrial and mechanical equipment covering the mid-Atlantic states with leading brands of compressors, pumps, and heat transfer equipment, and offer support services such as system design, assembly, and aftermarket service and repair. For more information, visit www.cummins-wagner.com.
____________________________________________
MODERN PUMPING TODAY, July 2016
Did you enjoy this article?
Subscribe to the FREE Digital Edition of Modern Pumping Today Magazine!
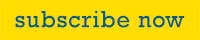