Power plants are filled with applications that require tarps or other barriers to protect equipment and workers from unwanted exposure to a variety of things. In some cases, protection is needed from the weather, including both hot and cold temperature extremes, as well as exposure to rain, snow, wind, or sun. In other situations, foreign material presents a danger, and a rugged barrier material is needed to keep potentially damaging dirt, dust, and debris from entering systems. These situations and more make material providers who can evaluate potentially debilitating plant situations and develop solutions to mitigate the hazards a vital partner to power generating companies.
Griffolyn® is a high-quality, internally reinforced polyethylene laminate manufactured by Reef Industries. The material is designed for a wide range of applications. Its patented, high-strength reinforcement provides superior puncture, tear, and abrasion resistance, even in the most demanding of situations.
Griffolyn can be formulated with many enhanced performance characteristics. From outstanding weathering characteristics to custom features, such as fire retardancy, anti-static properties, corrosion inhibition, or heat shrinkability, Griffolyn products offer a range of features to meet almost any power plant need.
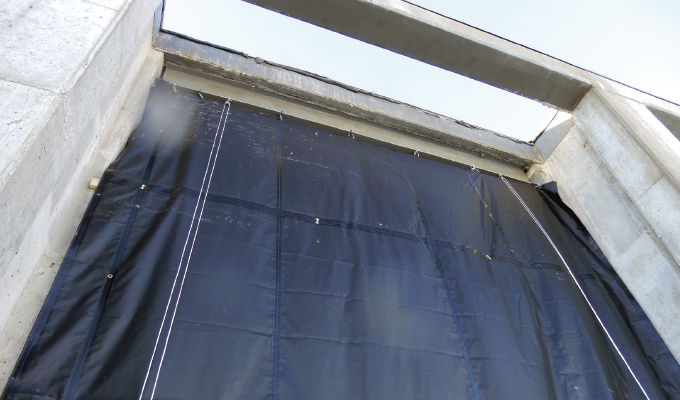
CUSTOMIZED TO ANY SIZE AND SHAPE
Among the uses some power plant operators have found for Griffolyn are as corrosion protection, equipment storage and shipping covers, landfill covers, vapor and moisture barriers, dust and environmental partitions (see figure 1), contaminated soil covers, tarps, and more. The possibilities are virtually endless.
Griffolyn is commonly available in white, black, and clear, but custom colors are also available upon request. The product is a cost-effective and durable solution to prolong the service life of power plant investments.
For example, a municipal utility in Texas worked to solve a problem they were having at one of their power plants. Reef Industries went out to the site a couple of years ago and had its technicians take some measurements. Then, the team made some custom tarps for them to fit around some of their equipment, creating partitions.
Having custom partitions helped keep birds out of the units, but more importantly, it protected vulnerable areas in the units from harsh weather. When the area experienced the hard freeze in Texas in February 2021, the municipal utility had everything ramped up to the fullest. The partitions helped keep them from shutting down.
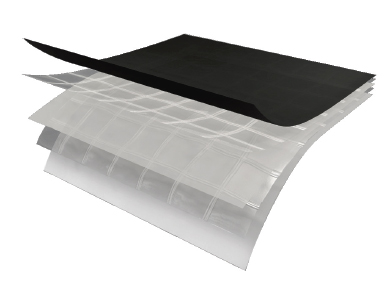
LAYERS EXTEND LONGEVITY AND ENHANCE PERFORMANCE
When it comes to plastic sheeting, it is important to understand the strength and thickness of the film, its composition, additives, chemical makeup, and the job it must perform. These factors will help determine if a film is fit for the task.
Many improvements have been made to polyethylene film such as Griffolyn since it was first used to cover greenhouses in the 1960s. Most polyethylene film is manufactured as a co-extrusion of three layers with different polymers and additives (see figure 2).
It is important, however, to consider more than just a film’s mil thickness. The fact is polyethylene film life is limited due to degradation processes induced by sunlight and heat. For example, co-polymer poly is a low-cost material, but it is only good for about one season. Therefore, if the film is expected to be regularly exposed to sunlight, a greenhouse-grade poly with ultraviolet (UV) protection is often a better option. While the cost could be twice that of co-poly, the product has a life expectancy of four years or more, which ultimately saves customers money. In high-wind locations, a woven poly or scrim-reinforced material could be the best option. That’s why Reef Industries’ technicians are so valuable—they know what their products are capable of and can recommend the best option for a given application.
“We’re a custom fabricator,” says one Reef Industries technician. “We can make whatever shape or size Griffolyn product a power plant needs—box-shaped items, openings with grommets, or anything else you can imagine. We can formulate a specific tarp, go out, measure the equipment or the structure, and we custom fit these things to the application.” For example, equipment at one facility is often different from that at another, but because the group is custom-creating each solution, the end product is always ideally suited to the situation.
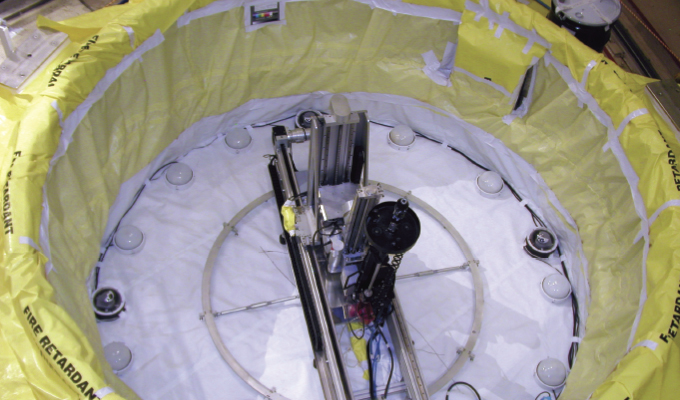
FOREIGN MATERIAL EXCLUSION
The nuclear power industry has unique and closely monitored requirements designed to enhance plant safety, and one thing nuclear operators and maintenance staff take very seriously is foreign material. Foreign material intrusion into primary or secondary plant systems, equipment, and components can cause fuel damage, safety equipment inoperability or degradation, lost generation, high radiation, and increased contamination levels.
The Electric Power Research Institute (EPRI) has reported that single instances of foreign material intrusion have cost hundreds of millions of dollars due to damage to plant equipment and complicated recovery requirements. Therefore, foreign material exclusion (FME) is an industry-wide initiative that all nuclear plant personnel—permanent and supplemental—must enforce.
Nuclear power plants generally conduct refueling outages on an eighteen- or twenty-four-month cycle. During these routine maintenance periods, FME programs are used to prevent debris and foreign objects from entering components. Many FME barriers are available for different situations, and Griffolyn has been used at some nuclear plants for these purposes (see figure 3).
For example, Reef Industries was called about a bird situation at a nuclear facility in the southern United States. The birds were getting into the area over the plant’s spent fuel pool and their guano was changing the pH level of the water. They take that stuff pretty seriously, especially the foreign material exclusion. That’s just something they have to have—these barriers to prevent things from happening—they can’t have contaminants in there. Reef designed a custom tarp to prevent that from happening.
Heavy-duty nylon covers are some of the most frequently used FME barriers. These standard nylon covers provide a cost-effective way to prevent foreign material intrusions. Vented FME covers allow pressurized systems to be covered more safely than with non-vented covers. Nylon FME barriers of all sizes are a convenient way to maintain foreign material control. Furthermore, FME tarps are often used to ensure machines and other components that are important, sensitive, or valuable do not get contaminated or damaged by foreign objects. Designing these critical tarps and covers regularly involves taking precise measurements and meeting extremely tight tolerances, which Reef Industries technicians have proven to be adept at doing.
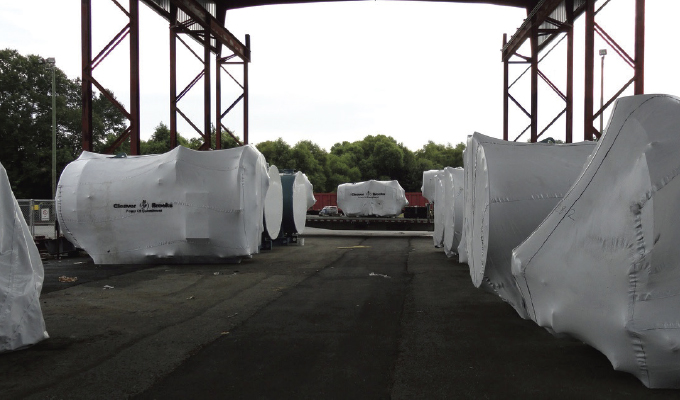
PREVENTING SPREAD OF CONTAMINATION AND PROTECTING EQUIPMENT DURING SHIPMENT
Another application for which the nuclear industry has relied on Griffolyn products is to cover contaminated components and prevent the spread of contamination. In fact, Reef Industries has been providing reliable storage and contamination control solutions to the nuclear industry for more than 60 years. Like other Griffolyn products, contaminated equipment tarps are tough and durable, and come in a variety of shapes, sizes, and colors. Whether customers want to reduce shipping costs, maximize facility use, comply with regulatory requirements, or save time and money, the value and performance of Griffolyn are unsurpassed.
Furthermore, these high-quality plastics can be produced with specialized properties including fire retardancy for safety applications, anti-static for critical equipment, and are incinerable to reduce the volume of radioactive waste. Additional tie-down methods, such as grommets, D-rings, webbing straps, pipe loops, and drawstring closures, are also available to help secure contaminated equipment covers in place.
There are plenty of non-nuclear power plant applications for which Griffolyn tarps and FME covers also make good sense. Boiler manufacturers have found heat shrinkable wraps help to keep shipments clean and reduce corrosion (see figure 4), especially when combined with other rust prevention methods, such as incorporating a volatile corrosion inhibitor (VCI) in the plastic film.
VCI is a technology that simplifies the corrosion process and is ideal for keeping items such as packages, equipment, and metal cavities rust-free. VCIs work by releasing molecules from corrosion inhibiting compounds into the air. When these compounds touch metal surfaces, they form a thin layer of molecules that prevents air and moisture from coming into contact with the surface, which effectively inhibits corrosion.
VCIs are considered one of the better rust prevention methods because the corrosion inhibiting molecules have the ability to protect surfaces that are difficult to reach with traditional rust prevention products. That’s because the VCI transforms from a solid or a liquid into a gas, which permeates throughout the area to be protected and forms a molecular barrier layer. This layer then blocks other molecules, such as water or oxygen, from attaching to metal surfaces.
VCIs can be applied against equipment or incorporated into a material, such as Griff-Shrink®, which is a patented multi-ply heat-shrinkable laminate. Griff-Shrink three-ply VCI consists of layers of UV stabilized polyethylene, cord reinforcement, and high-strength shrinkable film. Reef Industries’ five-ply VCI product combines alternating layers of reinforcing between three layers of specialty shrink films and polyethylene for a heavy-duty cover. One advantage of VCI incorporation is that parts can be stored with the film applied without rust preventative oil, which often requires careful and time-consuming cleaning before a part can be used. Large equipment has been wrapped in VCI shrink film for long-term outdoor storage with excellent results.
Nobody likes to see rust on new components, but the issue goes beyond just visual aesthetics. Rust not only degrades the appearance, but can also hinder equipment operation, causing sticking, in some instances, or even causing components to seize in extreme cases. That’s why taking precautions to protect investments is important.
PROVEN PERFORMANCE WITH WIDE-RANGING SPECIAL FEATURES
Reef Industries began producing Griffolyn in 1957. It has proven to be a high-quality product that has countless applications in many different industries, including the power sector. Among the attributes that make Griffolyn so versatile are weather and corrosion protection, antistatic, chemically resistant, lightweight, fire retardant, heat shrinkable, low permeability, UV stabilized, puncture resistant, fire rated, and long outdoor life.
FOR MORE INFORMATION
Mark Mullin is Griffolyn product manager with Reef Industries. For more than sixty years, Reef Industries has been manufacturing and fabricating reinforced film laminates and composites. Its expertise in producing quality, custom configured final products ensures customers’ needs are always met in a timely and professional manner. Reef Industries offers a wide range of products, material grades, additives and fabrication capabilities to meet or exceed requirements. For more information, visit www.reefindustries.com.
MODERN PUMPING TODAY, December 2022
Did you enjoy this article?
Subscribe to the FREE Digital Edition of Modern Pumping Today Magazine!