Whether it be due to a broken impeller, a busted seal, or a faulty drive, pump system shutdowns due to component failures are expensive in both the cost of repairs and the loss of productivity. One way to combat these often unforeseen stoppages is to adopt a predictive maintenance philosophy, wherein the pump’s operators choose when and why shutdowns occur—rather than playing catch up after a catastrophic failure—thereby minimizing their impact on efficiency and the bottom line. Below, David M. Williams, director of engineering at Liberty Pumps, joins SWPA Executive Director Adam Stolberg to discuss the value of predictive maintenance for submersible wastewater pump owners.
What does predictive maintenance consist of, and how can it best be applied to submersible pump applications?
Predictive maintenance entails monitoring of key equipment properties to detect changes or trends that serve as early indications of conditions which need to be addressed. In the case of submersible pumps, the key items that can be monitored are vibration, power consumption, run time, and output.
How would you describe the benefits of predictive maintenance for extending the life-cycle of the total system and its components?
By detecting and addressing conditions early, longevity of the product and the overall system can be greatly increased. For example, a pump can be scheduled for a service based on changes to vibration signature and conditions can be corrected well before a failure occurs. With preemptive service such as replacing a worn impeller, or bearings and seals, it can mean the difference between the product lasting for years or catastrophic failure that may not be repairable.
What are some of the benefits predictive maintenance offers for improving efficiency?
Conditions such as worn impellers or partial clogging greatly impact pump efficiency. Addressing these issues can lead to reduced run times and power consumption while minimizing wear and tear on the equipment.
What basics would you recommend every pump owner put on their maintenance checklist?
The following items are good indicators of pump conditions and should be performed on a regular basis:
- Visual inspection of pit for debris build-up which could lead to float interference or pump obstruction.
- Vibration/noise sampling—abnormal noises or changes in vibration are good indicators of pending issues.
- Changes in cycle times—increased duration of pump cycles could indicate wear or partial clogging.
- Current draw—increases in current draw or significant variation between legs should be investigated.
How important are professional organizations, like SWPA, for staying up to date on the latest performance and maintenance standards? What resources could you recommend?
Organizations like SWPA bring together experts from all of the top manufacturers and key users from throughout the country and creates a forum where knowledge and best practices are shared for the betterment of the industry. SWPA live training and webinars are great resources for transferring this up-to-date knowledge to the industry—from design engineers to installers to maintenance personnel.
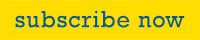
MODERN PUMPING TODAY, August 2019
Did you enjoy this article?
Subscribe to the FREE Digital Edition of Modern Pumping Today Magazine!