Ham Baker and Unitspark have completed the intricate installation of a penstock at a pumping station in South London in which a severely restricted access issue had to be overcome with an innovative, cost-effective engineering solution.
Part of Thames Water’s ongoing program to replace ageing assets before the end of their forecast life, a 3.9 foot by 3.9 foot penstock was required at Wandle Pumping Station but with this size too large for the 29.5-foot deep shaft and pipe, installation of a standard penstock would have caused significant delays and costly disruption.
PUTTING THE PUZZLE TOGETHER
Thames Water called upon two companies with vast experience of penstocks and specialist works to bring about the manufacture and installation of a new unit that would overcome the sizeable access challenge.
Based on a highly detailed concept from bespoke engineering specialists Unitspark, Ham Baker (who have been making penstocks since 1886), set about designing what became known as the “jigsaw” penstock, crafted in segments. Ham Baker Group installs penstocks all over the world, but the one by Thames Water required a very different way of thinking.
Designing a two-leaf segmented penstock (to extremely fine tolerances) that would have to be lowered down and traverse up a pipe for a very precise installation certainly called upon all of Ham Baker’s experience. Together with Unitspark, Ham Baker sought to provide a long term solution for Thames Water, producing a high quality penstock made from stainless steel, including every single component part, with exacting attention to detail.
PUTTING THE PIECE INTO PLACE
Following manufacture by Ham Baker, Unitspark set about planning the quickest and most effective way to carry out the installation of the “jigsaw” penstock with only minimum disruption. The discovery of live assets and a 9.8 foot thick block of concrete (that hadn’t shown in the former sewage treatment works’ plans) made the task even more challenging.
Rob Horne, director at Unitspark, adds, “Working closely with Thames Water and Ham Baker, our highly skilled team went to great lengths to overcome the access issues. We are used to wet and difficult environments and this was no exception—also having to deal with high levels of hydrogen sulphide. Lifting, rotating, and positioning the jigsaw penstock down the 29.5-foot shaft required the utmost skill and precision, before which, our engineers had to first build a fabrication bench to later assemble the penstock and its thirty component parts.”
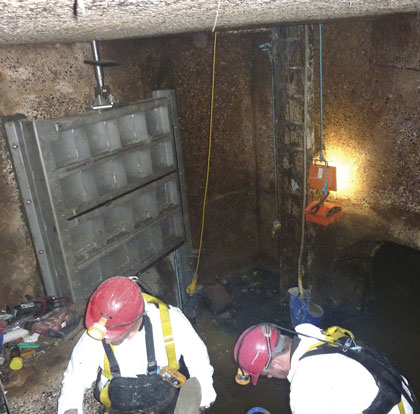
SEEING THE COMPLETE PICTURE
“Ham Baker and Unitspark successfully made this a specialist mechanical job, rather than a very costly and disruptive civil engineering project,” Brett Willis, project engineer from Thames Water, notes.
“The installation has been completed in just one week, with no need for major civils, new shafts, or cofferdams. The benefits in savings are substantial. Working close to a river and major strategic discharge mains drastically reduced the risk to the environment and the catchment. It is a credit to all concerned that this exercise in serious asset management was completed in such a professional manner.”
For More Information
Paul Higginson is director at Ham Baker Group. Ham Baker’s name is synonymous with precision-engineered products and adding value to customer’s individual requirements. The group designs complete engineered solutions, with experts on hand across all sectors to cover customers individual process and flow needs. For more information, visit www.hambakergroup.com.
____________________________________________
MODERN PUMPING TODAY, October 2016
Did you enjoy this article?
Subscribe to the FREE Digital Edition of Modern Pumping Today Magazine!
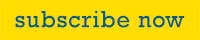