By Emily Newton
Unaddressed compressed air leaks can lead to increased costs, equipment malfunctions, and other issues that cause headaches in industrial settings. However, you can’t fix air compressor leaks before knowing they exist. Here are some steps you can take to identify such issues and prepare to address them.
LOOK FOR UNUSUAL CHANGES IN OPERATING METRICS OR EQUIPMENT BEHAVIOR
Even hidden air leaks can cause issues that people eventually notice before pinpointing the problem. For example, unfixed problems can add thousands of dollars to a company’s operating expenses. Thus, if a plant manager sees creeping increases in energy usage without explanation, that’s a signal to start looking for leaks.
Similarly, leaks can negatively affect the equipment that depends on compressed air to work. For example, a leaky system frequently experiences pressure drops. Those could hurt the performance and lifespan of pneumatic systems, leading to operational disruptions and more maintenance costs.
Increased equipment cycling can also occur due to leaks. Since that characteristic raises the air compressor’s overall operating time, the machine could need replacing sooner than expected.
Moreover, leaks may make compressors occasionally switch to loaded running modes outside of operating hours. That issue could cause as much as 25% more energy consumption when it happens over prolonged periods.
LISTEN AND FEEL FOR LEAKS
A leak doesn’t produce a noxious odor or puddle on the floor, so it’s not always easy to detect. However, the most straightforward way to spot one is to use your ears.
Walk around the air compressor, paying close attention to it and any attached lines. You may hear a telltale hissing sound. However, if you’re in a loud manufacturing environment, hearing that noise will probably become virtually impossible.
Using an auditory identification system can become more effective if every person who works with a company’s air compressors takes responsibility by listening for leaks. Make sure everyone understands that some leaks are significant to feel, even when they’re too quiet to hear.
Implement a system whereby every compressor with an identified leak has an associated tag. That approach makes it easier to quantify a leak problem and estimate the extra costs it causes.
It’s also useful for team members to know which components most often have leaks. Those include:
- Air hoses
- Hose connections
- Hose fittings
- Metal tubes (particularly if rusty)
- Air cylinders (around rod seals and piston packing)
- Piston-packing leaks (around the cylinder control valve’s exhaust port)
- Flanges (often due to missing welds)
- Control and shut-off valves (because of worn packing)
- Filters, regulators, and lubricators (when improperly installed)
Teach people to try the simplest solution first after finding a leak. More specifically, have them check the connection and see if it needs tightening. If that check doesn’t address the problem, more extensive troubleshooting becomes necessary.
USE SOAP TO ASSESS AIR HOSES
Another easy-to-implement leak-detection method involves something you can find in the nearest bathroom—soap. This method works on air hoses. Begin by unplugging the air compressor and covering the air compressor hoses with hand soap and a bit of water. Then, turn the system back on and examine the hoses. If you see bubbles form, escaping air is the culprit.
This method works well for catching tiny leaks. However, contrary to what many people think, a small leak needs prompt repair as much as a larger one. You should ideally treat each leak as a repair priority regardless of its size. That’s not always realistic, though. Perhaps you’re in a situation where your compressed air system has several problem areas of various sizes.
In that case, you can see significant cost savings even before fixing all of them. The best approach is then to tackle the largest leaks first to see the most noticeable outcomes. For example, fixing 10 1/4″ leaks saves more money than 50 leaks 1/16” in diameter.
RELY ON AN ULTRASONIC LEAK DETECTOR
An ultrasonic leak detector is an often-preferred leak detection method. That’s especially true if it’s impossible or exceptionally challenging to find an air compressor leak with touch or hearing methods. Also, some leaks occur in hard-to-access places. In such instances, an ultrasonic leak detector can get the desired results.
Several types of ultrasonic technology exist. Airborne ultrasonic is the most common type utilized to find compressed air system leaks. Most tools used for this task allow an operator to tune the ultrasonic waves to various frequencies. The suggested frequency for leak detection is 40 kilohertz (kHz). However, some airborne ultrasonic equipment has a fixed frequency of 38 kHz.
As a person begins using an ultrasonic leak detector, they’ll scan the area in all directions and may adjust the instrument’s sensitivity. That’s because the high-frequency sound waves coming from the ultrasound are low-energy. Thus, they’ll bounce and reflect off solid surfaces instead of traveling through them.
After finding a leak’s general area, the detector operator will usually slide a focusing probe on to the tip of the airborne scanning module. Doing that helps pinpoint the leak’s location by narrowing the field of view.
If you already have a tagging system in place for logging leaks found through other methods, apply it to a walkthrough with an ultrasonic detector, too. The ultrasonic system will indicate the leak’s decibel level. It’s useful to include that information on the tag.
ESTABLISH A LEAK PREVENTION PROGRAM
Becoming more proactive about addressing leaks takes time and resources. However, creating a thorough plan to meet that goal can save you money and labor when fixing future leaks. One aspect to consider is whether you’ll use in-house resources to find air compressor leaks or hire professionals from external companies. Manufacturing company AFG Flat Glass America opted for the former approach, and leaders sent some of its workers to receive ultrasonic certifications for leak detection.
Douglas Bowker, plant maintenance superintendent at an AFG facility in Greenland, Tennessee, explained, “Compressed air is not free. It costs Greenland approximately $137,000 per year to supply compressed air to the plant. Air leaks, therefore, cost us money. A small leak that is undetected by the human ear can typically contribute to $3,000 of cost per year. The ultrasonic equipment can now be utilized in a cost-saving manner to detect such leaks and fix them proactively.”
You’ll also need to decide how often to screen for air compressor leaks. Experts suggest inspections occur every 4-6 weeks and be carried out by plant maintenance personnel. Ensure that those workers scrutinize the compressed air equipment in every primary section of a facility.
Set a firm timeline for when your company will have the written report of the findings, too. Making it available no more than a week after an analysis occurs is a best practice because it allows people to take efficient action to target any issues.
GET SERIOUS ABOUT AIR COMPRESSOR LEAKS
You may initially think air compressor leaks aren’t significant issues. However, this overview emphasizes why they can become costly problems that affect operations throughout your company. Use the steps here to develop an action plan for dealing with leaks quickly and minimizing unwanted consequences.
FOR MORE INFORMATION
Emily Newton is a technology and industrial journalist. She is the editor in chief of Revolutionized, a publication dedicated to exploring the latest industrial innovations.
MODERN PUMPING TODAY, August 2021
Did you enjoy this article?
Subscribe to the FREE Digital Edition of Modern Pumping Today Magazine!
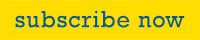