By Emily Newton
When pumps fail, site managers have to manage consequences like downtime, maintenance, and damage — as well as sewage overflow in the case of wastewater pump failures.
Knowing the most common causes of pump failure can help you avoid these consequences. By implementing maintenance plans that mitigate these failure causes, it’s possible to keep pumps running for as long as possible.
COMMON CAUSES OF FAILURE IN WASTEWATER PUMPS
While pumps can fail in a wide variety of ways, there are a few common manners in which pumps tend to malfunction.
Cavitation in pumps is the rapid creation and collapse of air bubbles in pumped fluid. This occurs when the net-positive suction head available (NPSHa) is lower than the net-positive suction head required (NPSHr), meaning the pressure on the pump fluid has dipped below its vapor pressure.
Air bubbles form in low-pressure areas of the pump, typically near the eye of the impeller, then collapse as they move to higher-pressure areas, often at some point along the impeller vane.
Pump cavitation causes damage — primarily to mechanical seals and bearings — and a reduction in pump performance. The NPSH margin needed to prevent cavitation varies depending on the particular pump and how it’s being used.
On average, NPSHa will need to be around four times greater than the NPSHr — but the needed NPSHa can be anywhere between 2 and 20 times greater than NPSHr.
Fouling is another common pump issue for wastewater facilities. Over time, particulate matter from pumped fluid can accumulate to water pump flow path surfaces. Hard water tends to cause scaling, or the buildup of minerals, while wastewater and seawater may cause the creation of biofilms.
Fouling may begin soft and then harden over time, meaning early detection and proactive monitoring of pumps may make fouling easier to fix.
PREVENTING CORROSION OR WEAR AND TEAR
Corrosion of pipes and pump materials will occur over time due to chemical reactions between the pumped fluid and exposed metal surfaces. While some corrosion is inevitable, pumping fluid and system management can sometimes accelerate the pace of corrosion, resulting in earlier-than-expected pump failure or other problems.
Choice of pipe material can also help to slow the rate of corrosion. Cast iron, for example, is a popular choice of pump material but may corrode readily when exposed to low-pH pumping fluid. Stainless steel is more expensive than other materials but is resistant to corrosion under a wide range of operating conditions.
Depending on the composition of wastewater and pump fluid, cast iron may be an acceptable choice. Knowing the conditions your pumps will be under and choosing a material to match will help reduce the speed of corrosion.
Natural wear and tear can also eventually lead to pump failure. Regular maintenance checks and scheduled repairs can help you or your team identify when parts need to be replaced due to wear, helping avoid premature pump failure.
Maintenance methods that take advantage of real-time conditions monitoring technology, like networked sensors monitoring pump pressure and similar variables, may help workers identify excessive wear and tear before it causes failure.
Certain operating conditions can increase wear on pumps, accelerating the failure of pump components. For example, particulate matter in pumped water can both cause fouling and speed up the pace of wear on a pump.
Pumps exposed to especially corrosive or fouling pump fluids may need more frequent maintenance than other pumps.
LOOKING BEYOND THE PUMP
Because pumps are so critical to wastewater systems, post-incident reviews and repairs often focus directly on the pump, sometimes at the expense of other system components. Often, pump failure isn’t a result of issues with the pump itself — instead, other equipment like power supplies or piping.
For example, voltage unbalance and excessive head pressure are two common causes of failure or malfunction in pumps, leading to mechanical stress and cavitation respectively.
Working backwards from pump failures, identifying how the pump failed and how the system’s operation may have caused the failure, is a good way to prevent future malfunction.
Simple measurements, like power and flow meter readings, can provide key information — like voltage and the actual flow rate of a given pump — that can reveal potential pump issues. Information from equipment like pump relays can be similarly helpful.
A maintenance plan that includes regular monitoring of pump and system conditions will offer more chances for catching issues like voltage imbalances and excessive or insufficient pressure.
BEST PRACTICES FOR AVOIDING PUMP FAILURE
Regular maintenance and knowledge of common pump failure causes will go a long way in helping you prevent pump failure.
If you already have an effective maintenance plan in place, condition monitoring and system audits are a good next step.
A variety of condition monitoring platforms are available. Many manufacturers of pumps and pump control systems offer proprietary SCADA systems that monitor wastewater levels, providing early notice on malfunctions or failures.
Some wastewater treatment facilities also use networked sensors to provide real-time operational monitoring. These sensors continuously gather and report information on pump conditions, providing a remotely accessible window into a pump’s current performance and health.
System audits should investigate operating conditions and components that commonly cause pump failure.
For example, re-evaluating a pump performance curve during an audit can provide valuable information that may help prevent future pump failures.
As system conditions change — sediment builds up, scaling occurs, and air is trapped in pipe corners — the pump performance and system curves can change. Repairs, retrofits, and regular maintenance based on pre-existing or legacy pump curves can cause trouble down the line, like oversized replacement pumps.
These oversized pumps can cause serious noise and vibration, jostling flanged pipes and connections loose or fatiguing pipe welds over time.
Ensuring that data on pumps and site systems are up-to-date and accurate will help you avoid problems like these.
TECHNIQUES FOR AVOIDING WASTEWATER PUMP FAILURE
Wastewater pump failure can have serious consequences for a facility — including unplanned downtime, high maintenance costs, and sewage backup.
Avoiding pump failure can be simple — regular maintenance and condition monitoring are good ways to detect issues like corrosion or severe wear and tear before they cause problems.
System audits and reviews can help catch more complex problems — like an oversized pump that is starting to cause pipe damage.
ABOUT THE AUTHOR
Emily Newton is the Editor-in-Chief of Revolutionized, a publication dedicated to exploring the latest industrial innovations.
MODERN PUMPING TODAY, November 2021
Did you enjoy this article?
Subscribe to the FREE Digital Edition of Modern Pumping Today Magazine!
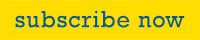