By Thomas Renner
PROJECT AT A GLANCE
What: | A $38.5 million renovation of the Robert B. Diemer Water Treatment Plant in Yorba Linda, California. The treatment plant is part of the Metropolitan Water District of Southern California. |
Why: | The treatment plant began operation in 1963, but many components had not been upgraded or replaced. The treatment plant, which has a capacity of 520 million gallons per day, is one of the largest in the nation and helps meet the water needs of nearly three million people. |
Project Scope: | Replaced flocculators, baffle walls, clarifier, effluent launders, drop gates, Weir gates, inlet gates, pipes of various sizes and material, sludge pumps, valves ranging from 1/2 to 42 inches, Smith Blair couplings, Victaulic couplings, and manual and electric actuators. Teams also stabilized a filter control building, including reinforcement of interior concrete frames and filter decks, and constructed new concrete shear walls. |
Flocculator Access: | Ten single- and double-leaf floor doors from BILCO were included in the project. The corrosion-resistant doors allow access to flocculator equipment. Flocculators are key of equipment that help determine the amount of treatment water needs and the sequence in which chemical agents should be added. |
Did you know? | The Metropolitan Water District of Southern California is the largest suppliers of treater water in the United States. Approximately nineteen million people rely on water from the “The Met.” |
Established in 1928 by the California legislature, with the goal to bring water from the Colorado River to southern sections of the enormous state, the Metropolitan Water District of Southern California has come a long way since it began operation in 1941. Work began in 1931 after voters approved a $220 million bond issue for construction. After decades of wrangling with water issues, leaders in the region believed the new agency could offer a long-term solution towards solving those challenges.
The project was enormous—35,000 workers laboring 24/7 in desert heat, constructing four dams, five pumping plants, blasting 90-plus miles of tunnels and establishing 150 miles of canals, siphons, and pipelines. Workers at the Weymouth Treatment Plant turned the first valve to deliver water to Pasadena on June 17, 1941. Water flowed to Beverly Hills, Burbank, Compton, and Santa Monica the following month, as they were among the thirteen original cities included in the original district.
Now, more than nineteen million people rely on water from the district. Its facilities serve residents that reach across 5,200 square miles, including parts of Los Angeles and San Diego. It is the largest supplier of treated water in the United States, and taps into fourteen cities, eleven municipal water districts, and one county water authority.
The region’s population relies on district water, and a recently completed $38.5 million project at its Robert W. Diemer Water Treatment Plant in Yorba Linda will help ensure continuity of service.
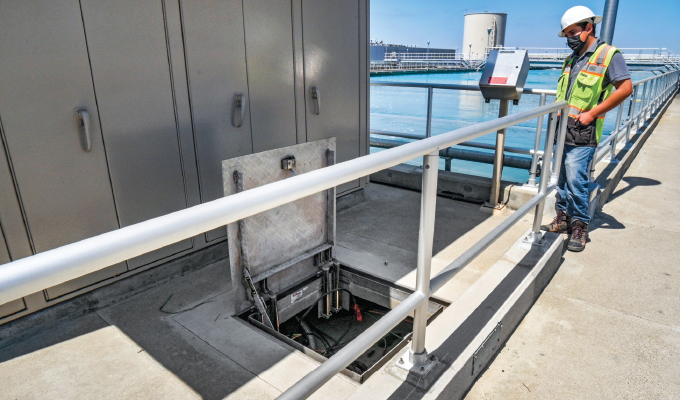
HUGE OUTPUT
The Diemer treatment plant began operations in 1963 but has not made any significant upgrade in improvement since that time. It is one of five water treatment plants in the extensive Metropolitan Water District Network, and has a treatment capacity of 520 million gallons per day, and delivers water via gravity flow to Los Angeles and Orange counties.
The facility is one of the largest in the nation, and has the capability to meet the needs of approximately three million people that live in the region. Water entering the 212-acre plant comes from two sources, a 440-mile aqueduct that is part of the California state water project and a 242-mile aqueduct that funnels water from the Colorado River.
Water is treated to meet or exceed federal and state drinking water regulations. Using advanced treatment technologies, increased monitoring and adhering to the stringent laws and guidelines, the process ensures the water quality meets government standards. The Met performs about 250,000 water quality tests each year.
“Water was not being wasted,’’ says Eber Luquin, project engineer for Environmental Construction, which dismantled the existing equipment and installed new components. “The equipment simply was not as efficient as it once was and water quality could be improved. The old, submerged mechanical equipment was coated in tar and some sealants used contained PCB properties.”
The project started in November 2018 and was completed in March 2021. Due to COVID-19 and other weather delays, the project took about four months longer than anticipated to complete.
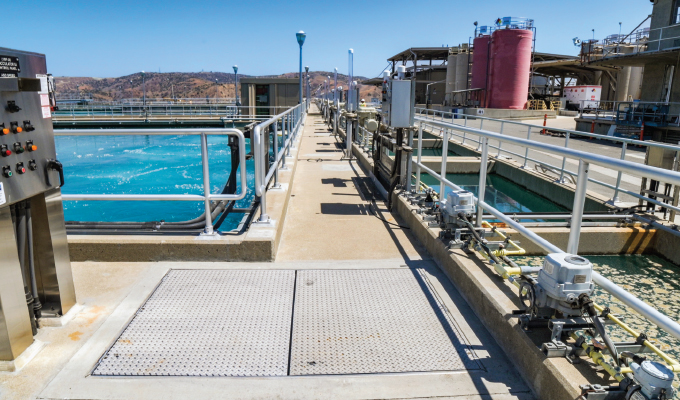
REPLACING COMPONENTS
Due to the age of the facility and minimal replacement over the years, nearly every component needed to be replaced. That included flocculators, baffle walls, clarifier, effluent launders, drop gates, Weir gates, inlet gates, pipes of various sizes and material, sludge pumps, valves ranging from one-half inch to 42 inches, Smith Blair couplings, Victaulic couplings, and manual and electric actuators.
Workers also strengthened a filter control building, including reinforcement of interior concrete frames and filter decks, and construction of new concrete shear walls. Teams also replaced 128 high-performance, rubber-lined butterfly valves and actuators, and replaced or modified structural support components, piping, mechanical equipment, handrails, and lights. Some hazardous material abatement was also required.
The expansive project scope and size of the facility posed some unique challenges for engineers. One task confronting Luquin’s team was installing effluent launders, where workers needed to solve issues regarding access and load restrictions at certain areas of the plant. Launders are an important part of the treatment process, as they help prevent waste materials from ending up in the water.
“We designed large crane pads that would not exceed 1,500 psi (ground bearing pressure) with our given loads so that we could install launders,’’ Luquin says.
Teams also faced access issues in constructing concrete shear walls. “The shear walls were constructed in four quadrants underneath the filter beds and access was very restricted to each location,’’ Luquin says. “There was only ingress and egress. We had to get all of our materials through a small opening, 5-feet by 6-feet, and then had a 15-foot drop. This was considered a confined space, so we had many OSHA regulations to comply with.”
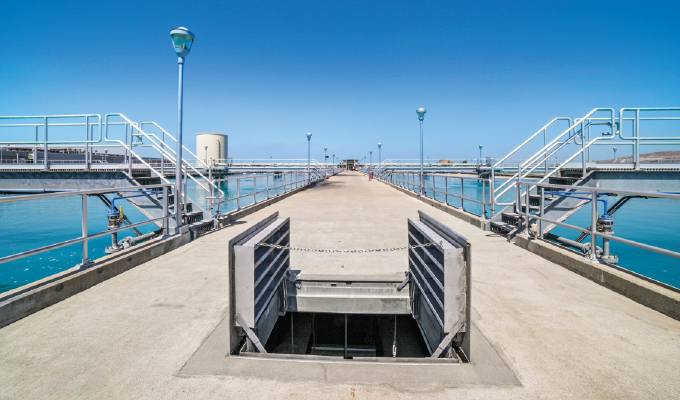
ACCESSING FLOCCULATORS
In any water treatment plant, flocculators are key pieces of equipment that help determine the amount of treatment the water needs and the sequence in which chemical agents should be added. Readings from the flocculators can help water treatment plants operate efficiently. Flocculation is also essential in keeping the water supply clean.
Treatment plant workers will access this important equipment through floor access doors manufactured by The BILCO Company. BILCO products are frequently used at water treatment plants due to their corrosion resistance and safe, reliable operation.
“BILCO hatches were selected due to their dependability and reputation with the plant,’’ Luquin says. “The fact that these hatches are made with quality stainless steel material to the dimensions we required and have a drain port built in were important features.”
Corrosion, especially at water treatment plants, can dramatically reduce the life of floor doors and other equipment. The ten BILCO floor doors used on this project feature stainless steel construction and hardware to withstand the corrosive environment at the facility. The doors also feature BILCO’S engineered lift-assistance to ensure safe and easy one-hand operation, automatic hold open arms, and positive latching mechanisms for security.
CONTINUAL CONCERNS
Water in California is a treasured resource. Efficiency and resourcefulness are paramount for the five treatment plants and the three major water reservoirs of the district. The massive renovations at the Diemer facility will help ensure that.
“I think it’s an essential lifeline for the people in Southern California,’’ Luquin says. “The supply from the Metropolitan Water District is a vital resource for smaller districts in the region. This project will help the system maintain peak efficiency.”
ABOUT THE AUTHOR
Thomas Renner writes on building, construction, engineering and other trade industry topics for publications throughout the United States.
MODERN PUMPING TODAY, November 2021
Did you enjoy this article?
Subscribe to the FREE Digital Edition of Modern Pumping Today Magazine!
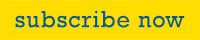