By Emily Newton
Today, leaders in many industries are shifting towards predictive maintenance rather than the traditional approach, which typically requires having equipment maintained on a schedule or only once problems result.
Predictive maintenance involves using tools like specialized sensors and data interfaces to show technicians the minor signs of worsened operations that could quickly turn into major problems. Some diagnostic processes also record vibration signatures so technicians can tell when a pump starts vibrating more, possibly signaling its impending malfunction.
Maybe you’re in a position to adopt predictive maintenance but are still unsure if you’d see measurable benefits from it. Here are some specific ways predictive maintenance could directly support better pump operations.
ENSURING INTENDED PERFORMANCE
Keeping pumps running smoothly is important at all facilities that use them. However, it’s arguably crucial when failures pose public health threats. Those problems can lead to fines, damaged reputations, and negative media attention while putting people’s lives at risk.
A pump failure at a treatment plant led to officials concluding that the problem caused a significant water supply safety risk. It took workers almost eight hours to detect the issue. The matter deposited sludge particles into the water. It also made the liquid have elevated aluminum levels and look cloudy.
If the team at that facility had taken the Industry 4.0 approach of using sensors to get immediate notifications of faults, they could have avoided this situation.
PROVIDING VALUABLE INFORMATION TO RESPONSIBLE PARTIES
As predictive maintenance has become more widely utilized, there has been an increase in tools that help companies capitalize on it. Authorized users can log in to specialized interfaces and see current conditions and historical data. Products that help companies stay on top of maintaining equipment facilitate finding the causes of problems and taking the correct actions to fix them.
This approach can also make equipment last longer. For example, installing a sensor on a progressive cavity pump can prevent issues like premature wear and decreased suction capabilities. When teams can immediately look at data that shows how certain factors change over time, it’s easier for them to know when problems might occur or identify inefficient processes that could reduce a pump’s lifespan.
HELPING COMPANIES REMAIN COMPLIANT
Professionals in numerous industries must follow regulations to satisfy the appropriate regulatory bodies. For example, in the construction sector, the Occupational Safety and Health Administration (OSHA) requires accommodating areas with at least 19 inches difference in elevation by providing ladders or ramps for workers.
It also mandates creating protective systems for trenches of five feet or more. OSHA has extensive requirements, so it’s no surprise that rules exist for concrete pumps, which construction workers often use.
One stipulation is that there must be pipe supports designed for 100 percent overload on systems with discharge pipes. One advantage of predictive maintenance is that it can help professionals become more aware of equipment as a whole.
For example, a technician may notice that a pump system does not comply with OSHA requirements while addressing an unrelated issue flagged by an Industry 4.0-based maintenance approach.
OPTIMIZING DECISION-MAKING
When technicians identify faults with pumps, they typically recommend how quickly a client should act when getting it fixed. For example, do they need to have it addressed immediately, or is it a minor issue that they could monitor carefully to see if it worsens?
When facility managers use predictive maintenance correctly, it can help them decide when to address known problems. Then, they’re better able to make smarter decisions.
Maybe your facility has a pump that transfers slurry between two tanks at a specific rate. In that case, there are total and partial failures to consider when overseeing maintenance. A total failure happens when the pump does not move the slurry, and a partial one occurs if it transfers slurry, but not fast enough.
Thanks to the details provided by predictive maintenance platforms, users can see what factors may combine to cause failures, then decide when to take action.
ENABLING EQUIPMENT TO OPERATE EFFICIENTLY FOR LONGER
Predictive maintenance concerns identifying issues before they cause problems that humans notice. Maybe you’ve been in situations where a piece of equipment was working correctly to your knowledge but experienced a massive failure a couple of days later. In other cases, there are gradual declines in efficiency that take a while to notice because they are so small.
However, even tiny issues can cause significant problems over time.
Applying Industry 4.0 technology to pumps can help professionals avoid circumstances where pumps wear out too quickly or become less efficient. The statistics gathered through predictive maintenance can also teach maintenance professionals how to spot problems.
For example, if a submersible pump experiences longer cycle times, that characteristic could indicate a partial clog or a worn part. Technicians can also let sensors monitor vibrations that could lead to progressively worse inefficiencies if the cause remains unaddressed.
PROMOTING SAFE, PRODUCTIVE WORKING ENVIRONMENTS
Predictive maintenance can also play a crucial role in helping operations occur safely and smoothly. For example, a dashboard may alert you to a previously unidentified leak. Addressing leaks is especially important in certain facilities that use pumps. Many of the substances pumped during chemical processing can corrode equipment or pose hazards to workers. Thus, unknown leaks could introduce preventable complications that hinder a plant’s operations.
Inadequate pressure is a warning sign of a leaky pump. If company managers notice the lack of pressure but don’t know a leak caused it, they could lose valuable working time. Moreover, a leak could make surrounding surfaces slippery, presenting slip-and-fall risks.
In the worst cases, a leak could interfere with traction so severely that a person gets injured and must take time off. Predictive maintenance alerts people to leaks sooner, helping facilities stay safe and retain high output.
MOVE AHEAD WITH AN INDUSTRY 4.0 FOCUS TODAY
Unexpected pump failures can lead to productivity losses, extra expenses, and displeased stakeholders. There’s no single best way to apply predictive maintenance to pump operations. Nor are there specific approaches that guarantee success.
However, these examples show that it’s worthwhile to see how it could pay off to become more aware of faults before they cause significant problems. Start by looking at historical data and seeing if there are certain types of pumps that have broken down prematurely or particular abnormalities associated with those instances. From there, it’s easier to see how you might reap the benefits of an Industry 4.0 plan when maintaining pumps.
ABOUT THE AUTHOR
Emily Newton is a technology and industrial journalist. She is the editor in chief of Revolutionized, a publication dedicated to exploring the latest industrial innovations.
MODERN PUMPING TODAY, May 2021
Did you enjoy this article?
Subscribe to the FREE Digital Edition of Modern Pumping Today Magazine!
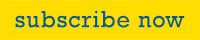