By Geoff VanLeeuwen, BlackmerBy Geoff VanLeeuwen, Blackmer
We’ve all been there. When we hit the on switch and instead of hearing the gentle hum of running equipment all we hear is silence. There might not be a worse feeling in the world. And if it’s your job to maintain this equipment and ensure your company’s operation is running smoothly on a daily basis, then this feeling of dread only increases, especially if your equipment happens to be operating in some of the most difficult, harsh, and rugged conditions possible.
WHERE HIGH-STRESS ENVIRONMENTS ARE THE NORM
When speaking specifically about operating in extreme conditions, liquid-transfer applications in the global mining, wastewater, and storage-terminals industries can be some of the most difficult. To say that equipment breakdowns and malfunctions in these markets are frequent occurrences would be an understatement. Therefore, the equipment tasked with helping maintain these industries, specifically pumps and other rotating equipment, must be able to live up to the stresses and challenges associated with these demanding day-to-day operations while also eliminating efficiency-robbing downtime and reducing costly maintenance.
For a solution, many operators turn to heavy-duty centrifugal pumps that have been designed to deliver the highest level of operational reliability, even in the toughest and harshest operating conditions. In particular, System One® Centrifugal Pumps from Blackmer® have built a reputation as a first-choice pumping technology for these types of operators.
System One pumps excel in tough applications because they have been specifically designed for use in the toughest, most extreme environments. The foundation of this design is a system of vibration-resistant seal and bearing construction that eliminates up to 90 percent of common pump failures. This capability is delivered in conjunction with a heavy-duty, solid, low-deflection shaft that prevents vibration damage and provides greater stability at the seal area, which also improves seal life. In fact, the non-wearing labyrinth-type seals that are featured on System One pumps offer lifetime protection for the pump’s heavy-duty radial and thrust bearings, resulting in greater load capacity and extended life. The result is a pump that offers the widest window of operation off of its Best Efficiency Point (BEP) when compared to competitive centrifugal pump models.
To help illustrate this point, below are a few examples where the operators in three very different industries have experienced unquestioned success by turning to System One centrifugal pumps for their liquid-handling applications.
MINING
A mining company in western Australia required the installation and use of a water-evacuation system that would not pollute nearby waterways. The system features a series of evaporators that take the wastewater and turn it into a fine mist that is blown by large oscillating fans over a large water source, such as a lake, retention area or dam. Critical to the operation are the centrifugal pumps that are used to draw the water from deep underground to the evaporation system at the mine’s surface. However, the standard ISO-style centrifugal pumps that were being used started exhibiting troubling and persistent operational deficiencies, such as a high failure rate and overall low life cycle. As a solution, the mine chose System One LD17 model centrifugal pumps as replacements for the ill-performing units and immediately realized an improved operation with none of the breakdowns and operational inefficiencies that dogged the other pumps.
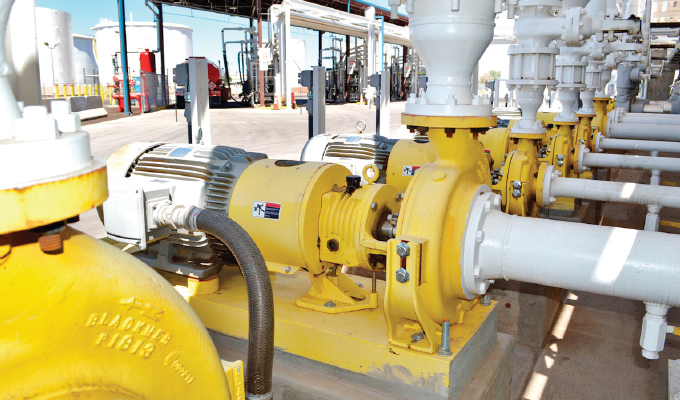
WASTEWATER
A municipality in the midwestern United States was experiencing persistent breakdowns of its pumps tasked with treating and removing sludge and other particulates during the water-reclamation process at its water-treatment facility. The municipality has found the ideal solution for this rugged, trying application in the form of System One centrifugal pumps featuring a “vortex” configuration. Vortex-style pumps differ from traditional centrifugal pumps in that their impeller is recessed into the back of the pump’s casing. This design creates a liquid vortex in the open casing, which allows the pump to direct solids, slurries, sludge, grit and stringy or fibrous material through the piping with minimal chance that clogging will occur. The result has been an increase in pump reliability that has resulted in optimized operational cost-effectiveness for the water-treatment facility.
STORAGE TERMINALS
A growing motor-fuel supplier with five storage-terminal locations in the southwestern United States was searching for reliable pumps that could support its 24/7/365 fuel-delivery and storage operations. With more than one million barrels (44 million gallons) of total storage capacity for refined (gasoline, diesel, aviation) and renewable (ethanol, biodiesel) fuels and lubricity additives, the fuel supplier needed pumps that could handle high volumes at high flow rates. The answer was found in the System One centrifugal pump family, with more than thirty-five System One pumps performing admirably in a variety of unique liquid-handling applications, including loading fuel onto tank trucks, unloading railcars, and the blending of ethanol and biodiesel.
SUCCESSES IN THE FIELD
For more details on the application successes attributable to Blackmer System One pumps, or to learn how this rugged technology can benefit your application, check them out on the PSG website. Still not sure? Be sure to ask about the unmatched five-year performance-assurance warranty for power-end components, and a one-year mechanical-seal performance-assurance warranty that Blackmer offers on the System One.
FOR MORE INFORMATION
Siemens Digital Industries Software, a business unit of Siemens Digital Industries, is a leading global provider of software solutions to drive the digital transformation of industry, creating new opportunities for manufacturers to realize innovation. With headquarters in Plano, Texas, and over 140,000 customers worldwide, we work with companies of all sizes to transform the way ideas come to life, the way products are realized, and the way products and assets in operation are used and understood. For more information, visit www.sw.siemens.com.
Geoff VanLeeuwen, PE, is a product management manager for Blackmer®. He can be reached at geoff.vanleeuwen@psgdover.com. Blackmer is a product brand of PSG®, a Dover company, Oakbrook Terrace, Illinois. PSG is comprised of leading pump brands, including Abaque™, All-Flo, Almatec®, Blackmer®, Ebsray®, EnviroGear®, Griswold®, Mouvex®, Neptune™, Quattroflow™, RedScrew™, and Wilden®. For more information, call 616.241.1611 or visit www.blackmer.com or www.psgdover.com.
MODERN PUMPING TODAY, August 2019
Did you enjoy this article?
Subscribe to the FREE Digital Edition of Modern Pumping Today Magazine!
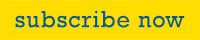