By Ben Keiser, Applied Flow Technology
Pumps, fans, and compressors account for about 60 to 70 percent of total electrical energy usage by US manufacturers. Inefficient operation leads to higher energy costs. However, goals to improve pump efficiency and reduce energy costs may not carry a high priority to owners and operators when their primary focus is to keep operation running smoothly. Owner/operators are more interested in improving reliability, minimizing repair costs and downtime, and increasing profits. A systemwide approach to an efficient and reliable design and operation of a piping systems is much more effective than a component by component approach (i.e., only addressing the pump itself).
A quality flow analysis software tool provides engineers and operators a better understanding of their system. This empowers them to make more well-informed decisions on how they could concurrently improve efficiency and reliability while reducing energy, repair, and maintenance costs, minimize downtime, and increase profits. Before we get into the benefits of flow analysis software, let’s discuss efficiency. In this article, we are going to focus on liquid piping systems and pumps.
In 2016 the US Department of Energy (DOE) launched the first Energy Conservation Standard for Clean Water Pumps. 10 CFR Part 431 is the new standard that increases the importance of energy efficiency for pump systems.
WHAT IMPACT IS THIS STANDARD GOING TO HAVE?
In short, pump manufacturers will need to ensure their pumps meet a Pump Energy Index (PEI) which complies with a minimum allowable efficiency based on the DOE pump energy conservation standards. When plant end users are looking to purchase a pump, they will need to consider the PEI for the pump as well as standard operating values such as flow rate, required total dynamic head (TDH) at the operating point, best efficiency point (BEP), etc.
The details regarding the energy conservation standard or how the PEI is calculated is outside the scope of this article. Rather, it is important to bring awareness to the existence of the standard and that it is a big step forward in the efforts of using more energy efficient pumps.
Unfortunately, purchasing a pump with a compliant PEI does not guarantee it will operate efficiently. There are many ways pumps become inefficient.
Outside of the new Energy Conservation Standard, there are not many standards for designing pump systems. Often, system components are designed independently, and time may not be spent to evaluate how components will interact with each other. This can lead to inefficient pump operation if the system causes the pump to operate away from its BEP.
In other cases, systems may be designed to meet future requirements with increased capacity but must operate to meet current market needs. Pumps may often be oversized, but not just for meeting future requirements. Sometimes, pumps get significantly oversized when design factor upon design factor is applied from the engineer, to the supervisor, the client, and finally the manufacturer. In either case, control valves may be installed to meet current demands. Energy is added from the pump, and then excess energy is removed as pressure loss across a control valve. This is one of the most common ways that energy is wasted, leading to high energy costs.
DRIVES TO MAINTAIN HIGHER EFFICIENCY
It is like driving your car with your foot on the gas pedal and the brake at the same time. If possible, it is better to incorporate a variable speed drive (VSD) or variable frequency drive (VFD), which can adjust the pump curve via the affinity laws to operate at different flow demands. This will maintain higher efficiency as well as help the pump continue to operate closer to the BEP more so than a control valve would. Flow analysis software can be used to help determine what speed the pump should operate at to achieve these goals.
There are a few other factors leading to inefficient pump operation. System aging and equipment wear take their toll on reducing system efficiency. As corrosion, fouling, and internal pipe scaling become prevalent, the system pressure loss increases. Also, as pumps wear out, the performance can deviate to a degraded pump curve. Overall, the pump and system would not be operating where they were originally designed to operate which leads to decreased efficiency and higher energy costs.
Calculating the efficiency for a pump is a simple task and is even easier with flow analysis software. When modeling a piping system with flow analysis software, a pump curve can easily be specified for a pump component. If an efficiency or power curve is entered as well, then the resulting efficiency based upon how the system is operating is simply an output parameter that requires no additional calculation. The resulting pump efficiency has a direct impact on energy costs. Improved efficiency can have a dramatic effect in lowering energy costs.
OPERATING AT THE BEST EFFICIENCY POINT
Although pump efficiency is important, the proximity of operation of the pump to its BEP is more critical. The BEP is the operating flow rate at which the pump’s efficiency is at its maximum. Operating closer to the BEP can increase the efficiency of the pump itself. But it will have a much bigger impact on the overall reliability of the pump and that may be more important to focus on rather than the efficiency value itself.
Figure 1 is known as the Barringer Curve and it provides a graphical relationship between pump efficiency and reliability. Plotted is a typical pump curve and its associated efficiency curve. The BEP flow rate is represented by the vertical dotted line which identifies the maximum value of the efficiency curve. The bell-shaped curve is a reliability curve which represents the mean time between failure (MTBF). If a pump is operating at the BEP, this would represent an MTBF value of 1.0. This means that when operating consistently at the BEP, the pump will operate most reliability and will last the longest period from failure to failure. For some pumps, an acceptable range of flow rates to operate at could be from 80 to 110 percent of BEP. When operating in that zone, the reliability curve shows a significant decrease to 0.5 MTBF. This means more failures, more repairs, more often.As the pump operates at flow rates further to the left and right of the BEP, there are some common problems that can occur in different areas where the pump is operating on its curve. Obviously, the pump is less efficient and will result in higher energy costs. But the real problem is the constant reliability issues that will be present such as cavitation, recirculation within the pump, seals and bearings wearing out faster, etc. Higher energy costs are easy to deal with in comparison to the significant repair and maintenance costs, downtime, and lost production and profits.
A LOOK AHEAD
Although it is good that there are more efforts now for vendors to provide more efficient and energy compliant pumps, it is easy to see from Figure 1 that it is not just about efficiency. With more focus on improving reliability, not only will this minimize repair costs, increase profits, etc., it will naturally improve pump efficiencies as well. In next month’s conclusion to this article, we’ll look into how to improve reliability as well as efficiency.
FOR MORE INFORMATION
Ben Keiser is technical sales consultant at Applied Flow Technology. Keiser holds a bachelor’s of science in chemical engineering (2009) from the Colorado School of Mines. He can be found teaching many of AFT’s technical seminars and stopping over for lunch and learns with AFT customers. Founded in 1993, Applied Flow Technology has grown to be a leader in the pipe flow modeling software market. With a primary focus on developing high quality fluid flow analysis software, AFT has a comprehensive line of products for the analysis and design of piping and ducting systems. For more information, visit www.aft.com.
MODERN PUMPING TODAY, June 2020
Did you enjoy this article?
Subscribe to the FREE Digital Edition of Modern Pumping Today Magazine!
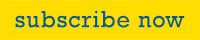