The global competitive landscape for manufacturing is squeezing everyone—from the Tier 1 automotive companies to electronics goods manufacturers. It is shortening the required time to market and with little warning. This high-pressure environment requires high productivity from its players resulting in either doing things faster and leaner without compromising quality or giving the game away to a hungrier competitor who is willing to do whatever it takes.
How do you become more productive? Do you continue to do the same thing over and over again and expect a different outcome? Or do you examine every step in the process to make sure you have an optimal one that enables your team to work smarter and produce more?
Surveys conducted by multiple industry analysts and CAE vendors suggest that successful companies test and assess their designs well before the prototype stage.
Many frontloaded simulation tools are available for use by design engineers. About twenty years ago, the first wave of simulation tools, stress analysis, was introduced for use during the early design stages and it quickly became an integral step in the process. Now, all major MCAD vendors provide design-level stress simulation as a part of their portfolio. By frontloading stress simulation and conducting analysis early during the design stage, manufacturers did not stop simulation during the validation stage. Simulation simply became a method by which trends were examined and less desirable design ideas were dismissed. However, unlike the verification stage, during the design phase, speed is of the essence. Engineers need to simulate not only early but also often to keep in step with the speed of design changes. By iterating rapidly, engineers can discount the less attractive ideas and innovate more. Once a design has been explored and identified as viable, it can continue on to the verification stage.
TIP #1
Encourage performance assessment as early as possible and promote collaboration and knowledge sharing between analysis experts and design engineers during the design process to immediately improve efficiency and productivity in your organization.
The practice has now spread to new areas including computational fluid dynamics (CFD) analysis—long the reserve of the specialist during the validation phase. Frontloading provides the best environment for design centric CFD. This is similar to what in the past was called “upfront” CFD, except that here we are talking about embedding CFD in CAD, which adds benefits throughout a product’s manufacturing process. Market research data such as this from Lifecycle Insights highlights top objectives for fluid simulation as a design tool:
- Meet product requirements (for example: lower weight, faster speed, complex behaviors etc.)
- Avoid downstream development delays and costs (for example: reduce testing and prototyping, reduce change orders, etc.)
- Satisfy customer contractual obligations or regulatory requirements
- Reduce product lifecycle costs
- Drive production costs lower
In short, design engineers can help reduce the number of prototypes and optimize cost (through use of better materials and quality), efficiency, as well as improve company profit margins.
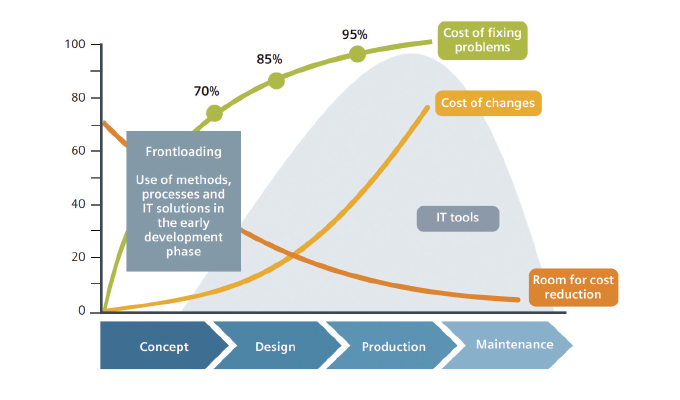
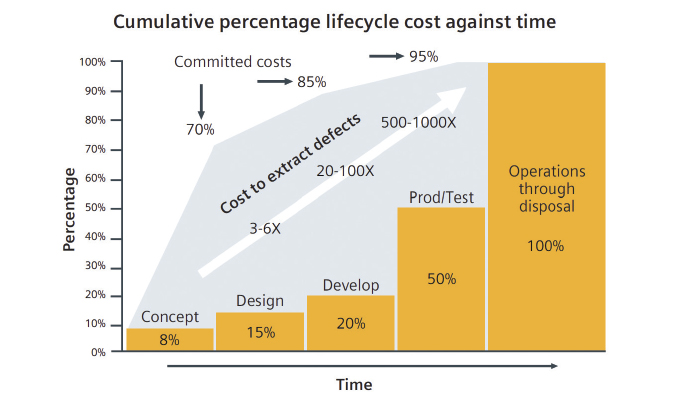
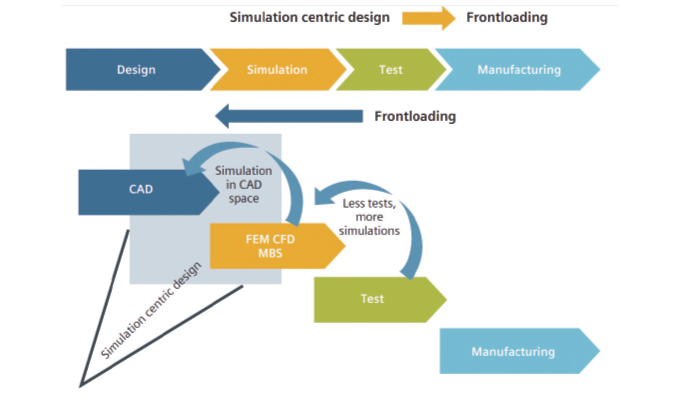
SUCCESSFUL IMPLEMENTATION IS KEY
Frontloading CFD has obvious benefits but how best to implement it? Implementing any change requires an examination of the four main elements of design and product development:
- The product being designed
- The process being used to design it
- The designer
- The end user of the finished product
Each consideration is a potential source of complexity and improvement. However, the process and the designer can be adjusted for immediate productivity gains. The product will be automatically improved as a direct result.
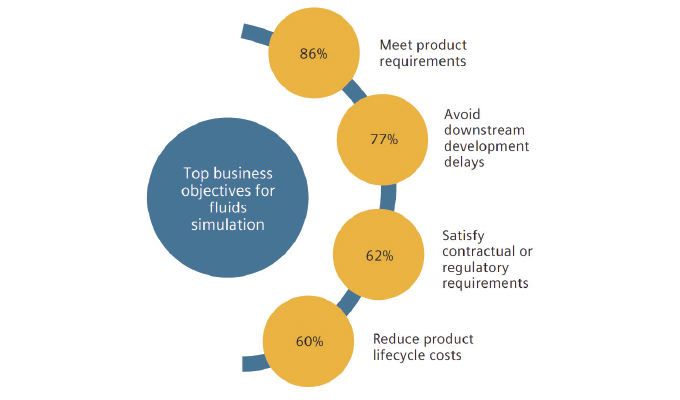
The Process
True to the concept of frontloading, many leading manufacturers have abandoned the old serial design system, where various functions work along a continuum, in favor of a multi-disciplinary product design process that requires successfully integrating multiple authoring systems and processes. For example, the number of electronic components in cars has grown drastically. Electronics now accounts for 35 to 40 percent of its cost. The Mercedes-Benz S-Class has 100+ ECUs and contains nearly as many ECUs as the Airbus A380 (excluding the plane’s inflight entertainment system). Therefore, designers need access to multiple tools across mechanical and electric/electronic domains to ensure a timely delivery of products that meet with customer specifications.
TIP #2
Impact efficiency and company profit margins by reducing the number of prototypes and optimizing cost (through use of better materials and quality).
This complex environment requires a high level of interdependencies to function effectively. Despite this complexity, organizations that have successfully implemented frontloaded CFD have not needed to reimagine or change their engineering process to benefit from it. Many engineering team managers originally thought that it would be more convenient to use existing tools, but they quickly realized that they were forcing their teams to use the wrong tools. The key success factor is selecting the right solution that offers the right combination of application-specific functionality and that fits into existing engineering processes without any disruption.
However, not just any CFD tool can be frontloaded. The CFD software that is used during the verification stage is not a good candidate for frontloading in the design process. This can be seen by reviewing the traditional CFD process where the CFD code receives geometry from a stand-alone CAD system versus a CAD-embedded one.
All CFD simulations require use of CAD models, geometry preparation including CAD clean-up and repair, meshing, solving, postprocessing and reporting. But each type of software deals with this process differently. The traditional process requires stepping inside and outside of the CAD package and repeatedly returning to the CAD tool with inherent risks of geometry approximations coming into the CFD simulation. Because design is iterative in nature, this process needs to be repeated for every single geometry change. In comparison, CAD-embedded CFD is contained within the CAD software; any and all geometry changes take place inside the CAD environment.
TIP #3
Successful implementation is the key to reaping benefits of frontloading CFD.
Many traditional CFD software programs consist of multiple interfaces – one for preprocessing, one for solution, and another for postprocessing. Traditional CFD software programs also tend to have their own proprietary interfaces that are not integrated with CAD. Every time a model needs to be analyzed, the data has to be prepared and exported out of CAD and imported into the CFD tool where the model can be “healed” for use.
Traditional CFD tools are crammed with technology that requires advanced training and education, which is why dedicated analysts are usually assigned the task. For example, most traditional CFD tools support many types of meshing algorithms. The engineer has to know which one would be the most appropriate for the specific application. In addition, he or she will have to work on the mesh until an optimal mesh for the model and application has been achieved. In short, using traditional CFD tools can be extremely time-consuming and slower than is needed during the design stage.
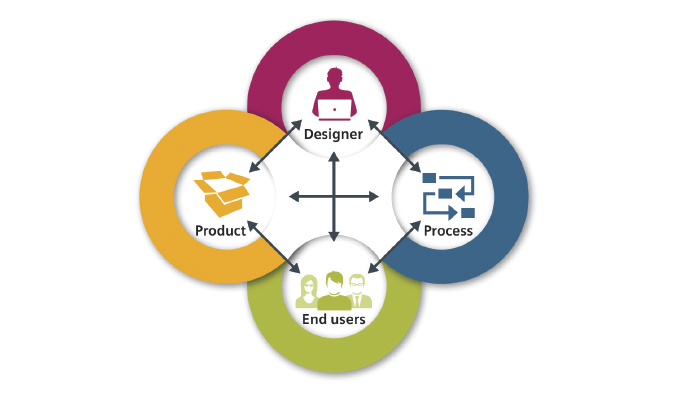
A LOOK AHEAD
In next month’s conclusion, we’ll take a closer look at these traditional CFD tools but with an eye toward how they compare against the benefits of design-level frontloaded CAE solutions. Finally, we’ll demonstrate how Simcenter FLOEFD technology, first introduced to the market in 1991, has been used by thousands of engineers to frontload CFD in the design process and the successes they’ve found using it.
TIP #4
Select the solution that fits into your existing processes without any disruption.
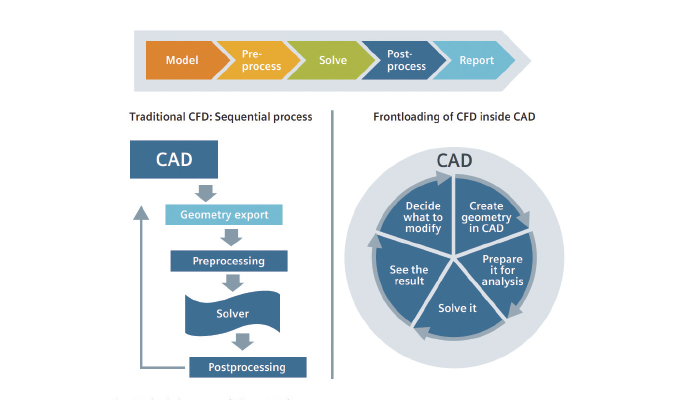
FOR MORE INFORMATION
Siemens Digital Industries (DI) is an innovation leader in automation and digitalization. Closely collaborating with partners and customers, DI drives the digital transformation in the process and discrete industries. With its Digital Enterprise portfolio, DI provides companies of all sizes with an end-to-end set of products, solutions and services to integrate and digitalize the entire value chain. Optimized for the specific needs of each industry, DI’s unique portfolio supports customers to achieve greater productivity and flexibility. DI is constantly adding innovations to its portfolio to integrate cutting-edge future technologies. For more information, visit www.siemens.com/software.
MODERN PUMPING TODAY, August 2022
Did you enjoy this article?
Subscribe to the FREE Digital Edition of Modern Pumping Today Magazine!