By Bryan Christiansen, Limble CMMS
Within the modern plant setup, the reliability and safety of assets take center stage. As competition soars, organizations seek innovative means to boost productivity, enhance plant safety, streamline workflows, and increase profitability.
Computerized maintenance management systems (CMMS) have taken the lead by simplifying maintenance operations, a key ingredient for establishing safe production environments. Below is how CMMS solutions can be utilized in improving plant safety.
1. TIMELY, PRECISE, AND SUFFICIENT MAINTENANCE
Safety hazards exacerbate when maintenance activities are poorly planned. Delaying or deferring maintenance increases the probability of accidents and failure of equipment occurring. Improving plant reliability demands a shift towards a data-driven proactive maintenance strategy.
Having a CMMS solution opens up a world of possibilities. Plant managers can monitor the health and productivity status of each asset in real-time. It enhances the early identification of defects that may threaten plant safety. CMMS programs retain centralized historical records of all maintenance activities performed on a wide range of assets. They are vital for scheduling maintenance activities, generating work tickets, allocating work orders to technicians, and reconciling spare parts and tool inventories.
With these capabilities, every piece of equipment is maintained correctly, guaranteeing safe operation. Maintenance activities are well scheduled, with the work orders evenly distributed. This systematic approach reduces maintenance workloads and minimizes confusion brought forth by a sudden spike in maintenance workloads, a factor that escalates safety risks.
2. AUTOMATION OF SAFETY AUDITS
Routine safety audits are necessary for keeping a safe plant environment. They are vital for evaluating compliance to minimum safety standards and procedures set out by the organization or government agencies. Performing safety audits can be strenuous, especially when dealing with a complex plant.
CMMS programs are crucial for speeding up audits and monitoring compliance. They provide tools for creating and updating equipment checklists. It ensures that every safety aspect is logged in during routine inspections and has provisions for recording and communicating developing risks in time.
Maintenance records stored by the CMMS programs are a source of evidence and are used for verifying compliance with statutory requirements. When inevitable equipment failure occurs, plant managers dig up equipment-specific maintenance history and use it to perform a conclusive failure mode and root cause analysis. This informs the execution of the appropriate corrective maintenance to prevent a recurrence.
With CMMS programs installed on mobile devices, it is simpler for managers to schedule safety inspections and send reminders to the responsible technicians. These programs enable maintenance teams to remotely monitor high-risk equipment with dedicated warning systems to generate appropriate alerts.
3. STANDARDIZATION OF OPERATIONAL POLICIES AND SAFETY PROCEDURE
Safety incidents occur due to human errors or violations of laid-out procedures. Given the complex nature of plants, technicians may be overwhelmed, causing them to overlook some operational steps or guidelines.
By implementing a CMMS program, an organization centralizes all the safety and maintenance information. Technicians access this information remotely, helping them make informed and accurate decisions to eliminate operational safety risks.
Maintenance technicians are exposed to a myriad of risks with accidents occurring in their line of duty. Organizations that have a CMMS in place can easily design a standard procedure for reporting such events. For instance, maintenance technicians can access a standard lockout tagout policy hosted by a CMMS program to ensure strict adherence to machine maintenance shutdown and start-up procedures.
4. OPTIMIZING FACILITY LAYOUT
Optimum plant layouts have the potential to minimize safety risks. As production scales up, the organization acquires additional assets. Production equipment must be laid out in an orderly manner to facilitate continuity of processes, ease asset tracking and guarantee the accessibility of safety utilities.
A CMMS solution enables the organization to keep a detailed record of the physical locations of all production equipment. Customized CMMS programs contain layouts of the plant floors that are frequently updated to accommodate newly acquired equipment. A definite plant layout ensures that no equipment is out of place, limiting safety risks due to improper asset arrangement. Plant floor workers use CMMS programs to gain access to information on safety facilities within the plant, making it easy for them to respond promptly during emergencies.
5. CMMS FOR STAFF SAFETY TRAINING
Safety policies and compliance requirements change as the business grows. Employees must be acquainted with these changes in good time. The scheduling of the safety training sessions should not affect routine production.
With a CMMS system, organizations can schedule training and outline key safety topics for specific equipment, operational area or facility. CMMS enables remote safety training for employees in different locations. Those employees who complete safety training receive certifications and their information captured in the CMMS database. With this information, maintenance managers identify the most critical tasks and allocate them to technicians with verifiable safety certifications.
SUMMING UP
Improving plant safety requires the involvement of all plant employees. The goal of a safety culture is to protect all employees from injuries and prevent the damage of production equipment. CMMS programs have sufficient tools that guarantee the reliability of plant assets and reinforce the safety strategies of any company.
CMMS programs are flexible solutions that can be upgraded and customized with time. These updates are necessary for improving safety compliance and matching technological advancements.
FOR MORE INFORMATION
Bryan Christiansen is the founder and CEO of Limble CMMS. Limble is a modern, easy-to-use mobile CMMS software that takes the stress and chaos out of maintenance by helping managers organize, automate, and streamline their maintenance operations. For more information, visit www.limblecmms.com.
MODERN PUMPING TODAY, August 2021
Did you enjoy this article?
Subscribe to the FREE Digital Edition of Modern Pumping Today Magazine!
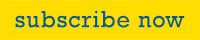