It’s common to find pump impellers with significant surface damage. The three most common causes of surface damage are erosion, corrosion, and cavitation. For each of these there are characteristics that will help indicate the primary cause of the damage. A brief description of each of the three phenomena will be helpful. Erosion is the simplest; it is simply the wear to the impeller surfaces from abrasive materials suspended in the pumpage. Corrosion is also straightforward; corrosion is a chemical reaction between ionized molecules in the pumpage and metallic elements of the impeller. Oxidation is the most common corrosion on pump impellers.
THE MANY CAUSES OF CAVITATION
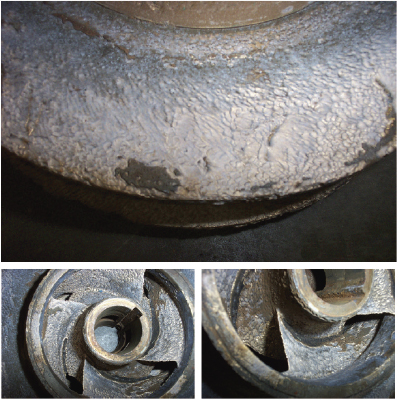
Cavitation is a more complex phenomenon. Cavitation is all about bubbles forming and imploding in the pumpage due to the pressure changes that occur as the pumpage flows through the impeller. Low pressure at the suction allows vapor bubbles to form and then these bubbles implode as the pressure increases through the impeller. The appearance of the damage to the impeller surfaces reflects the characteristics of the each of these three phenomena.
Since erosion damage results from the abrasive action of solids suspended in the pumpage, wear will be greatest where the flow velocity is high. Damage may be greatest at the leading edges of the impeller vanes, but the damage will continue through the flow path to the impeller discharge. Even outside surfaces of the shrouds will have some evidence of the abrasive wear. Due to the turbulence of the flow, especially at the suction, furrows will be common with erosion damage (see figure 1).
CLOSE INSPECTION NEEDED
There are similarities between the appearance of erosion and corrosion damage. But corrosion is somewhat less affected by the flow velocity. So, corrosion damage will be more evenly distributed across the impeller surfaces and all surfaces exposed to the pumpage will be affected. The evenness of the damage may be most apparent on the outside of the shrouds. While erosion may cause some damage to those outside surfaces, corrosion damage will be very evident (see figure 2). A key tip-off to corrosion is to inspect the face that butts against the shaft shoulder; it will be unaffected by corrosion.
Suction cavitation damage has unique characteristics that make it easy to identify. Since it is the implosion of vapor bubbles in the pumpage that causes the damage, the damage will be limited to only a portion of the flow path through the impeller, usually initiating right near the leading edge of the impeller vanes. This is where the initial pressure increase occurs causing the bubbles to implode. Once the bubbles have imploded, the rest of the flow path will show little or no damage.
The actual surface damage from cavitation will appear as erosion damage since the implosion of the bubble does erode the surface. But the limited area of damage in the flow path that begins near the leading edge of the vane is the tip-off to suction cavitation as the source (see figure 3). The outer surfaces of the shrouds will be unaffected.
The term “suction cavitation” is used here since that is the most common location for cavitation damage to impellers. The low pressure as the pumpage enters the impeller precipitates the bubbles that subsequently implode as pressure rises through the impeller. But cavitation is a phenomenon that can occur wherever there are pressure gradients in the flow stream.
Pressure gradients occur in the turbulent flow at the impeller discharge from recirculation when flow through the impeller is restricted. This phenomenon known as discharge cavitation is less common than suction cavitation. The trailing edge of the impeller vanes at the discharge will be eaten away, or the impeller discharge may be badly distorted. The rest of the impeller will be unaffected by discharge cavitation.
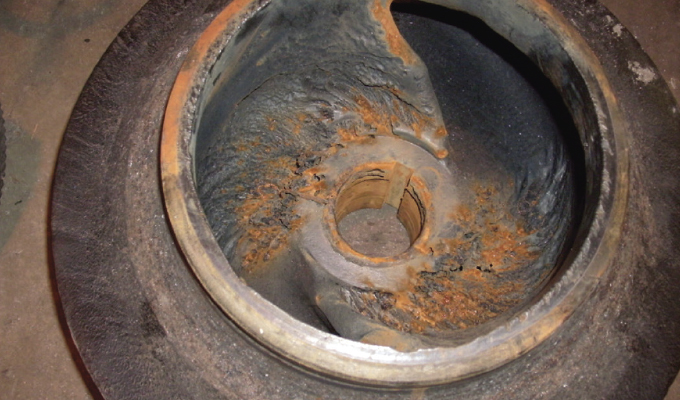
SPECIAL CASES
There are some special cases and combinations of causes which should be mentioned. One peculiar type of corrosion damage is de-zincification. Zinc is an element with “low nobility” and easily corrodes. On common bronze alloys containing zinc, ionized molecules in the pumpage will dissolve the zinc in the alloy leaving deep furrows and plug holes in the remaining copper elements of the alloy. A clear tip-off of de-zincification is the reddish color of what remains of the impeller (see figure 4).
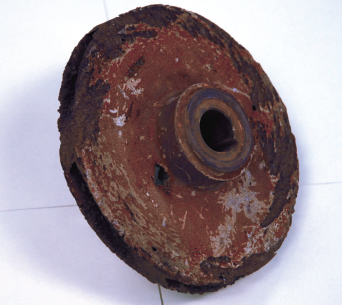
Another common occurrence is the combination of multiple causes of impeller damage. Various combinations of erosion, corrosion, and cavitation can occur. While the individual causes can be distinguished, when combined the characteristics are blurred and it won’t be clear that a single phenomenon is at work. Sewage is an example of pumpage that can be corrosive and carry abrasive matter causing erosion. All surfaces will be affected (corrosion), but deep furrowing will be present in high-flow velocity areas (erosion). And of course, cavitation could also be present adding to the erosion damage at the impeller suction. In these cases, an accurate diagnosis of the damage would have to include an analysis of the pumpage for the presence of corrosive elements and erosive materials.
In some applications, particularly in the petro-chemical industry, the sophistication of impeller damage analysis rises almost to an artform as analysis of rubs at close tolerance locations indicates operational problems with the pump. But for garden variety municipal water, wastewater, and circulation pump application, the tips provided here for identifying erosion, corrosion, and cavitation will help repair technicians classify the likely cause of impeller surface damage.
FOR MORE INFORMATION
Eugene Vogel is a pump and vibration specialist at EASA, Inc., the Electrical Apparatus Service Association. EASA is an international trade association of more than 1,800 firms in nearly seventy countries that sell and service electromechanical apparatus. For more information, call 314.993.2220, fax 314.993.1269, or visit www.easa.com.
MODERN PUMPING TODAY, August 2023
Did you enjoy this article?
Subscribe to the FREE Digital Edition of Modern Pumping Today Magazine!