Under the directives, national and regional laws, end users, machine builders, and system integrators are generally responsible for safety of machines and systems. The text in this month’s article will mainly refer to EU (European Union) legislation, which however is based on IEC/ISO standards that are globally applicable. All machinery supplied in the European Union must meet the essential health and safety requirements (EHSR) of the EU Machinery Directive 2006/42/EC.
EU MACHINERY DIRECTIVE, RELEVANT HARMONIZED STANDARDS, AND NATIONAL LAWS
To fulfill these requirements, it is sensible for the machine builder to follow a roadmap of set safety design steps. This helps both to meet legal requirements for the CE compliance marking and also to generate the necessary technical documentation. Functional safety regulations in the EU consist of two parts: the EU Machinery Directive and the harmonized safety standards. The harmonized standards provide the technical means and procedures to fulfill the Machinery Directive requirements.
European Standardization organizations CEN, CENELEC, and ETSI have harmonized certain international IEC/ISO standards as means to fulfill the legal requirements of the Machinery Directive. Product standard EN/IEC 61800-5-2 specifically focuses on drive-based functional safety and defines the standardized safety functions such as safe torque off, STO; safe stop 1, SS1; and safely-limited speed, SLS.
The same international IEC/ISO standards that are harmonized in Europe are widely applied in outside European Union as well. But it should be noted that different market areas also have their own local safety legislation, for example in the United States, Brazil, and South Korea.
HARMONIZED STANDARDS: RELEVANT FOR SAFETY DESIGN INCLUDING DRIVES
The harmonized safety standards are a collection of ISO, IEC, and European standards listed under the EU Machinery Directive. A harmonized standard, identified by the prefix EN, is an agreed norm in the EU member states and basis for national laws. Outside the EU the same standards, in IEC/ ISO versions, provide a global requirement framework that machine design should comply with.
In the following section, we list the most commonly-used harmonized standards, which are relevant for safety experts at machine builders and system designers.
ROADMAP FOR ACHIEVING CONFORMITY
The Machinery Directive requires machine manufacturers (or their representatives) to perform and document a risk assessment. The machine design must then take these results into account, with any risks reduced to an acceptable level. This is done either via risk-reducing machine design changes or by applying appropriate safeguarding techniques such as drive-based functional safety.
After the risks have been reduced to acceptable level, measures to control any residual risks have to be documented in user documentation (i.e., warnings, instructions, etc.).
A common way to design a safe machine and ensure conformity is to follow suitable harmonized standards when implementing the safety system. By fulfilling requirements of harmonized standards, it is presumed that the machine conforms to EHSR of the Machinery Directive.
Certified safety devices greatly simplify the design and validation process of a safety system. This is a big advantage since certified devices already have the necessary safety capability to achieve a given safety level, and the necessary supporting safety data for safety integrity level (SIL) / performance level (PL) verification calculations.
Usually a third-party certification is not necessary for machines. Manufacturers can “self-declare” conformity to the Directive based on proper design and documentation, a conformity assessment and achievement of CE marking (see figure 6).
Harmonized standards provide unified guidelines for hazard and risk assessment, and also outline the approach for reducing risks to acceptable level (EN ISO 12100). Designing machine safety functionality is most effectively achieved by following the harmonized standards for the specific machine types, if they exist, and/or the harmonized generic machinery application standards EN/IEC 62061 or EN ISO 13849-1.
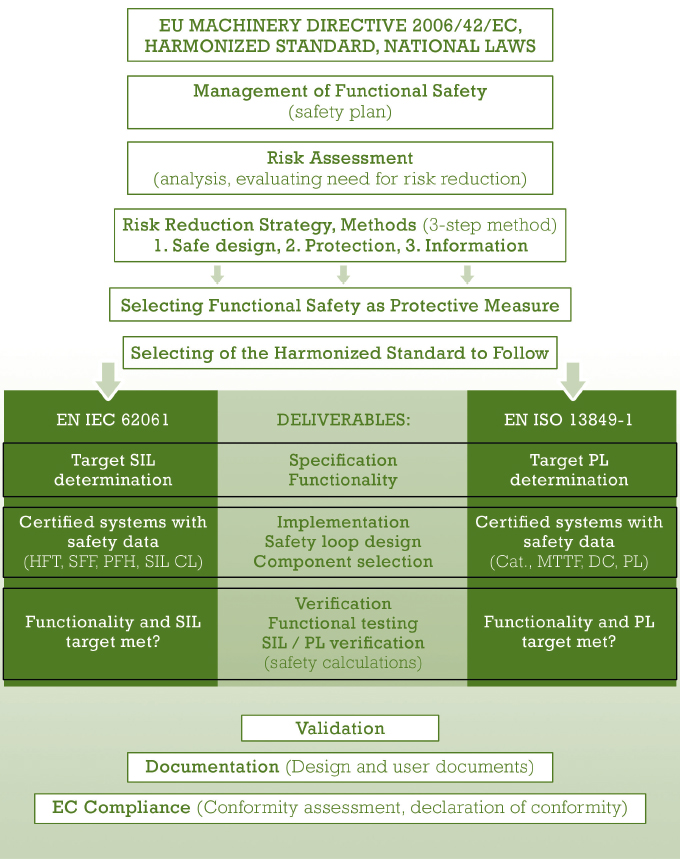
A LOOK AHEAD
In next month’s conclusion, we’ll wrap up this series by detailing how ABB drives facilitate drive-based functional safety for several users and include many certified safety functions.
FOR MORE INFORMATION
Siemens Digital Industries Software, a business unit of Siemens Digital Industries, is a leading global provider of software solutions to drive the digital transformation of industry, creating new opportunities for manufacturers to realize innovation. With headquarters in Plano, Texas, and over 140,000 customers worldwide, we work with companies of all sizes to transform the way ideas come to life, the way products are realized, and the way products and assets in operation are used and understood. For more information, visit www.sw.siemens.com.
Joonas T. Saarela is technical product manager for functional safety and can be reached at joonas.t.saarela@fi.abb.com. Ilpo Kangas is product compliance manager and can be reached at ilpo.kangas@fi.abb.com. Mikko Ristolainen is functional safety manager and can be reached at mikko.ristolainen@fi.abb.com. ABB drives offer many features that can help the safety designers achieve the required level of safety in a cost-effective way. Drive-based functional safety offers a vast world of possibilities to machine builders, designers, and safety professionals. For more information, visit www.abb.com/safety.
MODERN PUMPING TODAY, June 2019
Did you enjoy this article?
Subscribe to the FREE Digital Edition of Modern Pumping Today Magazine!
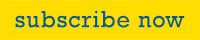