INSIGHT #5
If manufacturers can fully leverage the benefits of digitization, all the way from core manufacturing out to the end-user experience, the opportunities are exponential because they can better use all of the available data in the enterprise.
Across myriad industries, organizations are looking to transition from reactive to predictive maintenance, which will allow them to optimize asset management strategies, improve operations, and reduce costs. In the first half of this article, we laid out how the Industrial Internet of Things (IIoT) and Industry 4.0 are focused on digital transformation of the field device network with a goal of using available information from existing, installed field instruments to improve safety, operations, and reliability. Below, we’ll continue to share some valuable insight industrial leaders have discovered on this journey and examine how these innovations are being implemented today as well as where they may lead in the future.
ROLE OF COMMUNICATION PROTOCOLS
The FieldComm Group, formed in 2015 with the merger of the Fieldbus Foundation and HART Communication Foundation, is dedicated to developing, managing, and promoting global standards for integrating digital devices into automation system architectures while protecting process automation investments in the HART and Foundation Fieldbus communication technologies.
The mission of FieldComm Group is to provide a unified vision for a smarter industry. No single automation protocol addresses all industrial use cases—particularly with wireless. Instead, today’s environment requires secure plant floor to executive office data integration. FieldComm Group technologies provide the means to connect and integrate digital information. They enable a connected framework using intelligent field devices to reduce waste, improve safety and increase operational efficiency, and have for over twenty years.
INSIGHT #6
To focus on the new era of the IIoT, innovators must build systems that communicate information not just to developers or end-users, but to between the devices themselves, which can take the digital revolution to the highest of levels. For example, the FieldComm Group combines the resources of the Fieldbus Foundation and HART Communication Foundation in its systems, with plans to expand even more.
Digital down to the sensor level, Foundation Fieldbus has been at the forefront of digital transformation since its inception. The technology provides an all-digital communication infrastructure for process automation, with powerful multivariable measurement capabilities, robust device diagnostics, and the ability to integrate wireless devices across multiple networks. Its block structure is unique, enabling true distributed functionality, improved data management, and alarm and alert management.
Foundation Fieldbus allows industrial organizations to unlock the full capabilities of their existing assets. By providing the means to leverage immense amounts of data generated by modern automation systems, the potential uses and benefits are numerous. They range from enhanced data collection and improved remote monitoring, diagnostics, and asset management, to reduced configuration and commissioning effort.
Designed for use with analog instruments, HART technology offers a proven, reliable, long-term solution for plant operators who seek the benefits of intelligent devices with digital communication, while preserving existing investments in analog instrumentation and plant wiring. Much more than a communication protocol, with HART technology process plants have access to a wealth of digital process, maintenance and diagnostic information that is valuable throughout the plant lifecycle from design, to installation and configuration, through operation, and finally maintenance.
INSIGHT #7
With so much attention focused on the digital agenda, it’s easy to forget the important role that field level communication has to play. For example, HART and Foundation Fieldbus have both been proven over many years of use in the industrial sector and are the mainstay of process control today.
The bi-directional HART communication protocol provides two simultaneous communication channels—one analog, the other digital—and enables data access between intelligent field instruments and host systems. Communication occurs between two HART enabled devices, typically a smart field device and a control or monitoring system. Standard 4-20 mA wiring practices assure reliable communication.
WirelessHART and HART-IP deliver the benefits of intelligent devices with digital communications while preserving existing infrastructure, training, control system and operational investments. WirelessHART is a wireless communications protocol that uses mesh network technology for process automation applications. It adds wireless capabilities to HART technology while maintaining compatibility with existing HART devices, commands, and tools. HART-IP enables the HART protocol to run over any internet protocol (IP)-based connection, offering valuable HART data at the speed of Ethernet and supporting intelligent device management for smart process instrumentation.
OVERCOMING IMPLEMENTATION CHALLENGES
The goal with IIoT is to secure data seamlessly and improve applications, but there’s a large skills gap because many process engineers can’t get data from devices using their current plant network. The technology also leaves room for improvement because, while end users want a dashboard of useful information they can streamline right to the top of their organization, they don’t want to be inundated with data. It is important to prioritize the information coming from programmable logic controllers (PLCs) and distributed control systems (DCSs).
In recent years, there’s been plenty of talk about the wall coming down between OT and IT, but there are still profound language and protocol differences between them. And, because IT-based protocols enable IIoT and “Big Data” applications, these language differences must be resolved for IIoT to succeed on the OT side. For example, IT staffs use high-level, data exchange formats like XML and JavaScript Object Notation (JSON) as building blocks for web applications. To bridge the OT/IT gap, JSON, and XML representations of intelligent field device data would be very valuable.
Just as most transmitters and other process control devices progressed from point-to-point, 4-20 mA hardwiring to twisted-pair fieldbuses and digital communications in recent years, IIoT is expected to further simplify and accelerate their networks and communications. However, process engineers and operators will need more IT know-how as IIoT moves down to the plant floor and out to the field to interact with so-called edge devices, which include all the usual sensors, instruments, valves, actuators, transmitters, and other equipment
In this environment, the need for a universal, standardized, and interoperable technique to comprehensively describe automation components is more important than ever. It is vital for everyday purposes like device configuration, device replacement, maintenance, diagnostics, or audit trails—all essential building blocks in a modern field device management system. This description must be usable for all systems, independent of suppliers of devices, systems, or tools. Without it, the true potential of decentralization, transparency, integration and a central view of all data and functions cannot be fully realized.
SOLUTION FOR SYSTEM INTEGRATION
Today’s field instruments look more and more like embedded computers. Intelligent, microprocessor-based devices deployed across a wide choice of networks transmit a broad range of data that has never been available before. But increased data creates an information management dilemma. How can users take the huge volume of data created by intelligent devices and turn it into actionable information?
The first step is to simplify the procedures needed to access field device information by higher-level control or host systems. These procedures, known as integration, must be completed to assure proper device management by the host, including device configuration, replacement, maintenance, and diagnostics. They must be standardized, usable across all systems, and independent of device suppliers, system suppliers, or vendor-specific tools.
Leading process industry foundations, including FieldComm Group, PROFIBUS International, and the OPC Foundation, jointly developed the Field Device Integration (FDI) standard to solve the problem of integrating field devices with the multitude of networks, operating systems, and control systems commonly used in process plants. FDI takes account of the various tasks over the entire lifecycle for both simple and complex devices, including configuration, commissioning, diagnosis, and calibration.
The core of FDI technology is the scalable FDI Device Package, which describes a field instrument or automation component in all aspects. No other files are needed. The FDI Device Package incorporates a device specific Electronic Device Description (EDD) based on the harmonized Electronic Device Description Language (EDDL) per IEC 61804.
INSIGHT #8
Standards like FDI are the path to the future. It has been specified and developed by leading technology foundations and major suppliers of process control systems and field instrumentation. The specification is also based on close cooperation with respected end user organizations.
FDI Device Packages can be processed in FDI hosts as well as in an FDT2 Frame Application. This allows device suppliers to create a single FDI Device Package for their devices—instead of separate device type managers (DTMs) and device descriptions (DDs)—while still providing users the choice of either an FDI host or an FDT host environment.
By including all tools, documents, and interfaces in a single device package, FDI improves system integration efficiency and allows easier access by IT organizations to OT information. Moreover, it unifies device drivers, configuration tools, diagnostics, and documentation regardless of operating system with an independent and downloadable software package compatible with any FDI-registered host system.
Manufacturers and other industrial firms deploying IIoT applications can connect to valuable information in intelligent field devices—regardless of protocol—by using FDI to integrate the information in a process control system, asset management tool or enterprise resource planning (ERP) system; then visualize and evaluate the data; and ultimately take action based on the information to prevent shutdowns, lower operating costs, reduce maintenance expenses, and become more predictive in how plants are run.
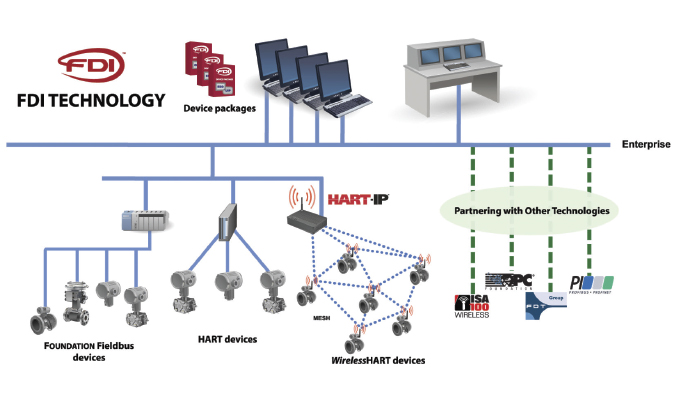
NEW ARCHITECTURAL MODEL
The Purdue Enterprise Reference Architecture has been a defining architecture for instrumentation, automation, manufacturing operations and business planning and logistics systems since its introduction in the 1990s. This pyramid model describes various “levels” of applications and controls in a manufacturing enterprise. It describes components from the physical levels of the plant (Level 0) through control equipment and strategies (Level 2). Level 3 describes the manufacturing control level, and Level 4 is the domain of enterprise business planning, or enterprise resource planning (ERP) systems.
With the emergence of the IIoT, however, and rethinking of the traditional process network view, two crucial questions for the automation industry are:
- Where will digital transformation occur?
- Where should the internet protocol (IP) network exist?
Some believe digital transformation is most appropriate at the field device level of sensors and actuators with digital-capable devices, while others think the IP network should reside all the way down in safety-critical systems. In either case, security is an overriding factor.
Undoubtedly, the classic automation architecture is undergoing profound changes to accommodate IIoT operational strategies. It starts with the ability to connect data and integrate it across the enterprise – only then can value be captured. FieldComm Group protocols and technologies play a vital role at different layers of the new architectural model, and assist with a well-balanced IIoT approach that can be deployed today and effectively maintained well into the future.
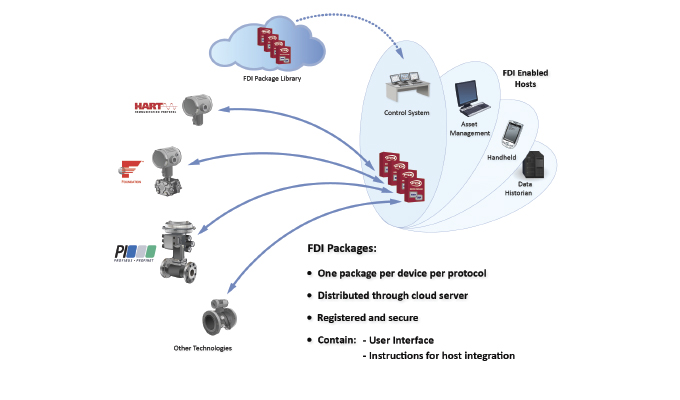
INSIGHT #9
The big advantage of FDI is it replaces various platform-dependent integration solutions and makes device packages interoperable with host systems because their device descriptions (DDs) are harmonized across the communication protocols and host systems.
At the bottom of the IIoT pyramid are “things” like transmitters, actuators, valves, controllers, monitoring systems, and other familiar equipment, as well as more recent developments such as video sensors and global positioning system (GPS) systems. Above the physical layer is a fabric of communication and control systems that manage field-level devices. This includes DCS, PLC, and safety systems utilizing wired and wireless networks, radio frequency identification (RFID) networks, fiber optics and copper wiring, and run by local or remote operators. The third layer consists of IIoT platforms and processors that take information from a plant or multiple facilities, aggregate the data, and then support tasks such as predictive maintenance, asset management, advanced control, and supervisory control and data acquisition (SCADA). While all this information is valuable, it is not really actionable without a human and external interface at the highest layer that gleans insights from the various systems in place. These insights help decide what type of analytics to run or what processes to optimize.
INSIGHT #10
Existing standards and technology will continue to advance, and will play a crucial role for decades to come, especially when it comes to providing IIoT connectivity and interoperability for the millions of existing devices installed across industry.
Based on the IIoT architectural model, system requirements include:
- Intelligent assets, connected intelligently by the appropriate communication protocol for a given application
- Data communications infrastructure with a span from the plant floor to the executive suite, and a scope that captures process data and intelligent asset information
- Analytics and applications to integrate asset data and deliver information
One of the core elements of the FDI specifications is an optional OPC-UA server that can be built into compliant products to seamlessly present data from field devices to higher-level systems. In the future, the FieldComm Group plans to offer a developer kit for connecting WirelessHART and HART-IP devices into cloud-based systems. This would include a server platform allowing an IIoT content delivery gateway to provide information from devices on the plant floor up into cloud computing platforms and services like Microsoft Azure.
Beyond the aforementioned system requirements, there is no substitute for an invested and capable workforce that is trained and knowledgeable in enterprise systems. Operational executives are charged with making data-driven decisions, and Subject Matter Experts (SMEs) must interpret intelligence from all available information. These and other people make the difference for the business, whether it’s business and risk analysis, or enterprise and supply chain planning.
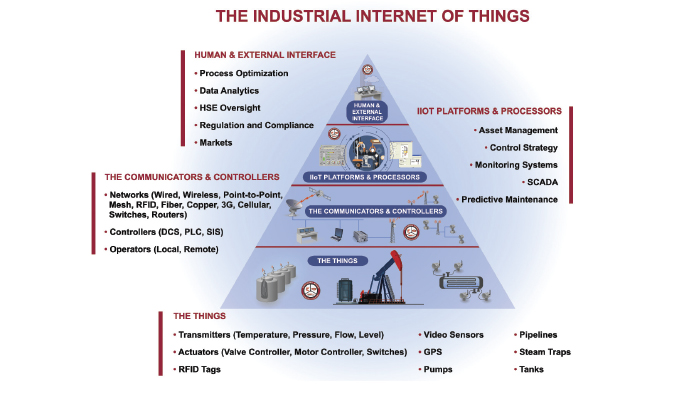
VALUE TO INDUSTRIAL ORGANIZATIONS
As described in this whitepaper, the IIoT connects sensors to analytic and other systems to automatically improve operational and business performance. Savings from greater utilization of digital intelligence creates more capital investment. Higher field reliability helps ensure increased uptime, safer operations, and greater efficiency. Advanced automation technology also raises productivity, manages assets over their entire lifecycle and optimizes experts’ knowledge to drive profitable business results.
INSIGHT #11
Experience around the world has shown IIoT devices can improve equipment reliability, process availability and integrity, and significantly reduce maintenance costs.
There is significant value to industry as a result of a smart connected device ecosystem, which makes it possible to address performance, reliability, safety, and environmental problems that have yet to be solved by traditional approaches. It is becoming possible to securely get the right information into the hands of problem-solvers wherever they are located, whether in a control room on-site or in a factory somewhere on the other side of the world.
One of the biggest opportunities for companies to realize IIoT benefits is to take advantage of the capabilities offered by plant floor to enterprise data management solutions. Although Foundation Fieldbus, HART, and WirelessHART technologies have been around for some time, the automation industry is still not utilizing their full capabilities, with a few notable exceptions. For instance, a 4-20 mA level transmitter simply evolved to became a fieldbus level transmitter or wireless level transmitter, whereas a digitally networked level transmitter can also provide multi-variables such as pressure and temperature measurement. Some advanced new devices like two-wire tank gauging systems, 4/8-input temperature transmitters, intelligent on-off valves, and other smart connected devices are already available, and more will be on the market soon.
Process industries and instrument manufacturers continuing to 4-20 mA and on-off signals should revisit plant automation architectures, product designs, and decide upon new business models to take advantage of the IIoT, since modern plants have already deployed it. Most new plants will be built on Foundation Fieldbus, and existing plants will be modernized using WirelessHART.
Fieldbus and industrial wireless technologies are also changing how plants are designed. Thanks to digital networking, end users can now deploy many more sensors in a plant because they pay for control loops, while the monitoring points are essentially free. This enables new business models like remote monitoring services to improve energy efficiency and reliability.
While the IIoT can utilize a vast number of connected industrial systems that communicate and coordinate their data analytics and actions to improve performance and efficiency, and minimize or eliminate downtime, there is no substitute for human experience and actions to improve operations and reduce costs.
CONCLUSION
The drive for digital transformation and smarter plant operations, as enabled by developments like the IIoT and Industry 4.0, can help manufacturing firms and other industrial enterprises leverage digital technologies to enable rapid deployment of new products, dynamic response to customer demands and real-time optimization of production and supply chain networks through interconnectivity of machinery, sensors and control systems. This approach also extends to asset management via predictive maintenance, statistical evaluation and measurements to help increase reliability.
At the heart of IIoT solutions for the process industries are FieldComm Group technologies helping automation suppliers and end users digitally connect to the data revealed by increasingly smart instrumentation, and to integrate the information with enterprise systems to advance business performance.
It’s worth noting there is a global installed base of millions upon millions of Foundation Fieldbus and HART protocol-enabled instruments. Information from those devices represents robust content for IIoT systems. The FieldComm Group is committed to enhancing the ease of use of its technologies to enable people—wherever they are located—to access critical data. The good news: there’s no need to reinvent existing data models, since they have been proven over more than two-and-a-half decades of use.
FOR MORE INFORMATION
Ted Masters is president and CEO of FieldComm Group. The FieldComm Group is a global standards-based organization consisting of leading process end users, manufacturers, universities, and research organizations that work together to direct the development, incorporation, and implementation of new and overlapping technologies and serves as the source for FDI technology. FieldComm Group’s mission is to develop, manage, and promote global standards for integrating digital devices to on-site, mobile, and cloud-based systems; provide services for standards conformance and implementation of process automation devices and systems that enable and improve reliability and multi-vendor interoperability; lead the development of a unified information model of process automation field devices while building upon industry investment in the HART®, Foundation™ Fieldbus, and FDI® standards. Membership is open to anyone interested in the use of the technologies. For more information, visit www.fieldcommgroup.org.
MODERN PUMPING TODAY, February 2023
Did you enjoy this article?
Subscribe to the FREE Digital Edition of Modern Pumping Today Magazine!