Reverse osmosis (RO) systems offer power plant owners and operators a reliable and well-proven water treatment solution. However, designing and caring for an RO system requires a thorough understanding of a plant’s water supply and the technology’s capabilities. The information presented here could help plant engineers design and optimize an RO system to match their needs.
The success of a new RO membrane system is often directly related to its pre-treatment. The previous section of this article discussed RO design issues and introduced how a pilot study should include a study of its probable pre-treatment equipment since the pre-treatment performance will directly affect the performance of the RO system. However, piloting the upstream processes can be challenging in sizing these components for the pilot RO unit’s low flow rate.
PRE-TREATMENT CONCERNS
The most important role played by pre-treatment is protecting the RO from incompatible substances. With the polyamide thin-film RO membrane commonly used today, the biggest concern is removal or destruction of any chlorine, or other potentially oxidative compounds. This membrane has very little tolerance to free chlorine (present in many municipal water sources), and is only slightly tolerant of chloramines (in other municipal water sources).
The most common methods for breaking down chlorine are reducing-agent injection and activated carbon filtration. The most common reducing agent is sodium bisulfite (NaHSO3), which reacts preferentially with free chlorine in breaking it down to the innocuous chloride ion.
Sodium bisulfite/sulfite injection systems can fail in ways that degrade RO membrane elements if not quickly remedied. The day tank could run out of solution, or the injection pump could lose power or pump-head prime. The injection pump setting might provide insufficient chemical to handle the full range of chlorine concentrations, or might be set for such a low pulse speed that the chemical does not sufficiently mix with the feedwater.
The proper NaHSO3 dosage should be injected any time the RO inlet valve opens, even if this opening is for filling the RO or for flushing it out before a shutdown. There should not be significant pipe length distance between the point of injection and the RO inlet valve, because this length will become fully chlorinated during shutdown by chlorine diffusion. The point of NaHSO3 injection should be immediately upstream of the inlet isolation valve.
ACTIVATED CARBON FILTRATION
Activated carbon filtration may offer a more reliable means of breaking down chlorine. During manufacture, non-carbonaceous materials are burned off, leaving porous granules with a high amount of pure carbon surface area. This has a high attraction for adsorbing almost any contaminant, including most organic materials and heavy metals, although there may be limited removal capacity for some contaminants that are shed into the effluent water.
The breakdown of chlorine by activated carbon involves an electrochemical reaction, which offers a high capacity for chlorine removal. The carbon gives up electrons to the chlorine atoms, forming innocuous chloride ions (Cl-) that remain in the water. In this reaction, oxygen atoms previously bonded with the chlorine atoms as hypochlorous acid (HOCl) now attach to the carbon surface. Because the carbon also reacts with dissolved oxygen in the water, the carbon surface can become fully oxygenated. It then loses its ability to remove additional chlorine, but this typically takes a few years with inlet chlorine concentrations less than 1 milligram per liter (mg/L).
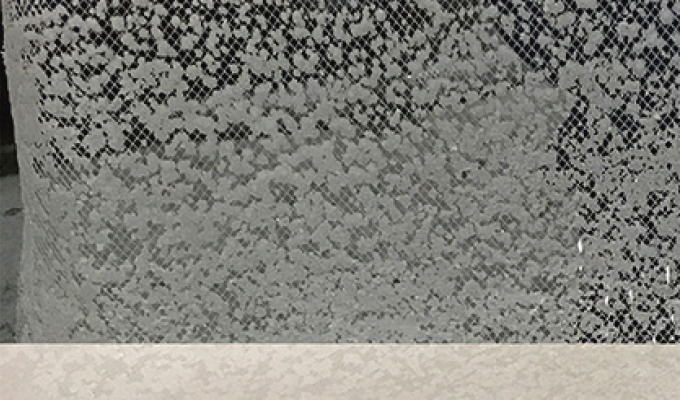
When ammonia is present naturally or when added by a municipality, chlorine chemically bonds with the ammonia to form monochloramine (NH2Cl) or possibly dichloramine (NHCl2). The chloramines are not as chemically reactive, and require more carbon volume for their breakdown. A catalyzed carbon media is available at an increased cost that improves the carbon reactivity with chloramines and reduces the need for oversizing the carbon filters.
Carbon system valves must not leak or otherwise bypass. They should be normally closed and driven by sufficient air pressure to prevent chlorinated water from reaching the RO system.
Maintenance is critical to the success of either reducing-agent injection or carbon filtration. It is recommended that the activated carbon media be replaced annually, or based on an increase in the effluent concentration of TOC, to prevent the shedding of biological particles into the RO system.
Over-injection of sulfite causes increased breakdown of dissolved oxygen in the water. This increases the potential for heavy growth of slime-forming species of bacteria, which can quickly foul an RO system if there is a sufficient concentration of organic food in the water source. This potential can be minimized by maintaining a residual sulfite concentration that is greater than zero but less than 2 mg/L as sodium sulfite, measured using a low-level test with sensitivity of 1 mg/L or less. As long as the sulfite concentration is greater than zero and it is well mixed into the feedwater, free chlorine will not be present.
PREVENTING SCALE FORMATION
There is typically at least one salt in any natural water source that will concentrate beyond its solubility and potentially form scale. Preventing scale formation should not be a major challenge unless the water source has an unusually high concentration of a slightly soluble salt, or unless the RO is being operated with an unusually high permeate recovery.
Scale formation may be prevented by injecting an acid into the inlet water, by softening the water, or by injecting a chemical scale inhibitor. Usually the least expensive method is a scale inhibitor, which slows the rate at which salt crystals grow when their solubility is exceeded.
Acid injection prevents calcium carbonate scale formation, but leads to an extremely high concentration of CO2, which is not removed by the RO system and places a high removal demand on downstream ion exchange processes. Also, acid injection alone doesn’t offer much protection against the formation of sulfate or certain other scales.
Softening offers several advantages, but suffers from high capital and operating costs, unless there are particularly low concentrations of calcium and magnesium hardness in the water. The softener also removes other potential scale-forming ions such as strontium and barium, and removes metals that would otherwise foul the RO system, such as iron, manganese, and aluminum. But the softening resin also fouls with the metals and then requires periodic chemical treatment.
Scale-inhibition chemical suppliers often use software programs to estimate the potential for scale formation. These programs predict the concentrations of salts present in the RO concentrate stream, as well as its pH, to determine how much scale inhibition chemical is needed.
The potential for silica scale is common with certain groundwater sources in the western United States. Inhibition formulations have shown varied success. Maintaining warmer water temperatures improves silica solubility, as does changing the water pH. Increasing pH is a common strategy, although the water must first be softened to prevent hardness scale from forming when a caustic chemical is injected to raise the pH.
When using a scale inhibitor, it is critical to rinse the RO system of its increased concentration of dissolved salts whenever the RO shuts down. Otherwise, scale particles grow and stick to the membrane surfaces during the shutdown. This rinsing process should be automated and is often performed with low-pressure inlet water. Low pressure reduces the RO permeation that tends to concentrate the dissolved salts.
A better rinse might be performed with pressurized permeate water if a line can be plumbed back to the RO from a permeate storage tank system. The permeate is biostatic; its use reduces the formation of biological solids within the RO while shut down.
A LOOK AHEAD
The next section of this article will discuss the issues related to membrane fouling. Fouling doesn’t necessarily reduce RO membrane life if the RO is effectively cleaned. However, if the RO is allowed to foul too severely and cleaning is not effective, then the membrane will likely continue to lose performance.
FOR MORE INFORMATION
Siemens Digital Industries Software, a business unit of Siemens Digital Industries, is a leading global provider of software solutions to drive the digital transformation of industry, creating new opportunities for manufacturers to realize innovation. With headquarters in Plano, Texas, and over 140,000 customers worldwide, we work with companies of all sizes to transform the way ideas come to life, the way products are realized, and the way products and assets in operation are used and understood. For more information, visit www.sw.siemens.com.
U.S. Water, a subsidiary of ALLETE, Inc., provides options for environmentally friendly, safe, and cost-effective water management. As experts in water, they use their in-depth industry knowledge and experience to enhance system reliability, efficiency, and profitability. For more information, visit www.uswaterservices.com.
MODERN PUMPING TODAY, May 2019
Did you enjoy this article?
Subscribe to the FREE Digital Edition of Modern Pumping Today Magazine!
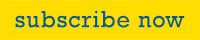