For nearly ninety years, ARO has been delivering reliable fluid management intelligence to the global marketplace, including the world’s first closed-loop controller for air-operated diaphragm pumps. Building on years of innovation and technical expertise, ARO responded to customer needs for a closed-loop system that allows them to customize production lines and remotely monitor fluid transfer to ensure greater efficiency and less production downtime. With the ARO Controller, ARO proactively solves some of industry’s most challenging fluid management issues while providing a solution that is easily integrated into existing production lines.
INSIDE THE BOX: TOUCH-AND-WALKAWAY AUTOMATION
The ARO Controller is a dual-pump controller featuring remote triggers that can perform auto shutdowns and display critical operating data and service alerts to operators via a control-panel display. With a closed-loop system, the ARO Controller features touch-and-walk-away automation that achieves dispensing repeatability within 1 percent.
A primary feature of the ARO Controller is that it operates within a closed-loop system with the air-operated diaphragm pumps it is connected to. The controller sends signals to the pump to maintain pump speed and volume delivery. Sensors in the pump relay signals back to the Controller, which are used to adjust the outgoing signal’s rate and maintain programmed parameters.
Additionally, the controller monitors a number of other signals, including leak detectors, analog signals, and remote commands. For example, these innovations alert the operator so they know when a diaphragm has ruptured, with the end goal of avoiding loss in productivity and equipment damage.
The ARO multi-pump controller also includes auto-fill functionality that receives signals from level sensors installed in a container. One sensor indicates when the container is full while the other sensor indicates when the container is empty. Depending on whether the pump is filling or emptying, these sensors allow the pump to maintain a consistent fluid level in the tank.
The controller also features full leak detection capabilities in the form of leak-detector sensors that uses optical technology, which is embedded into the pump’s air chambers to alert the system that liquid is present where it shouldn’t be. The sensor prism refracts light when fluid enters a space where fluid is unexpected, sends a signal back to the controller, and ultimately alerts the operator so that spills can be avoided.
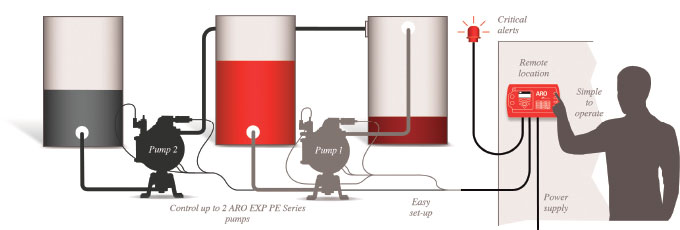
THE VALUE OF A CLOSED-LOOP CONTROLLER
Traditional control systems rely upon a series of manual processes that require the attention of an operator or multiple operators along a plant line. In contrast, a closed-loop controller allows customers to remotely take control of batching and monitoring fluid transfer with an ease of use that reduces errors and lowers costs.
Because a closed-loop controller doesn’t require the same level of operator attention as traditional control systems, an operator doesn’t have to be stationed at each pump as it draws and dispenses into another location.
This feature has the potential to increase productivity by saving on labor, while additionally saving on economic resources because it’s more accurate in product delivery. Overfill scenarios can be avoided without manual oversight, potentially delivering large cost benefits over time.
Repeatability is an essential element of any controller system. With ARO’s touch-and-walk-away automation, the customer can be assured that their process is running smoothly. For example, the controller relays signals to the pump in an effort to maintain the fluid flow entered by the operator. Because the pump sends responsive signals back, the controller can determine if the required flow rate can be maintained or not. If the flow rate cannot be maintained, an alarm will alert the operator who can then pinpoint the problem. The controller is easy to use and simple for the operator to program.
Another differentiator of the Controller is the ability to detect loss of prime. When the pump loses its prime, it stops pumping fluid and starts pumping air, at which point the controller triggers an alarm which the operator can use to stop the pump. This feature enables the operator to save time, energy cost and unnecessary pump wear. When an alarm is triggered, an LED on the controller blinks, an icon appears, and a buzzer goes off. Most importantly, there is an electrical contact on the controller that can be wired by the user to drive an external alarm—such as a siren or strobe—to readily attract attention when an alarm occurs.
Finally, ARO’s controller technologies can control two pumps with a single controller. The pumps can mirror one another or complement each other based on how the system is set up. The controller then uses a proprietary algorithm developed by ARO fluid intelligent experts to monitor stroke timing and determine whether the pump is running at the programmed speed, triggering an alarm if not.
Thanks to these innovations, ARO’s closed-loop system achieves dispensing repeatability within 1 percent, higher levels of production safety, and increased productivity.
Beyond these standard processes, however, are additional applications the controller can accomplish. For example, the proportional mode on the controller allows for two different pumps to operate off of two different analog input signals within the same process. This functionality works well when a process requires mixing two different products into a single container.
Another example is maxing out tank fill. In this application, level sensors are installed at both the top and the bottom of a container. When the pumps are in operation, a signal is sent to the controller notifying it that the container is full. The controller then shuts down the pump, and the system’s processes empty out that container. When the low-level sensor is reached signifying that the container is empty, the controller is notified, the pump is restarted, and the process can initiate a new cycle.
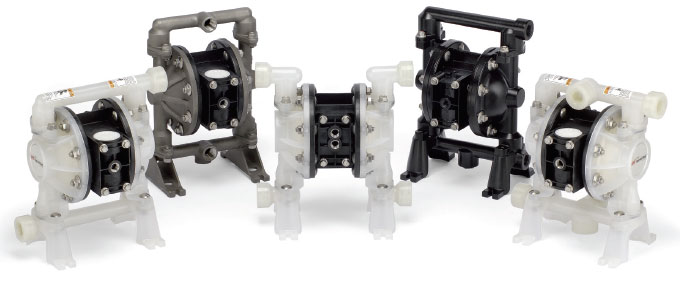
CONTROLLER FEATURES
The ARO closed-loop controller allows full-featured, multi-pump control in a simple-to-use and easy-to-install package. Further, a variety of pre-programmed and manual functions allow the plant manager to customize the system to suit their application needs. Finally, simple software updates ensure that the system is always running at an optimal level.
PROGRAMMABLE PUMP MODES
The ARO Controller’s general behavior is managed by programming specific pump run modes and general pump activities. These modes are programmable by the end user, allowing for maximum flexibility. The Controller features three run modes whose parameters are secured within a password-protected setup menu.
The ARO Controller also includes remote operation, which allows for operation of the pump from a remote location. This feature doesn’t allow programming capabilities, but does allow start/stop operation within these three modes.
BATCH MODE
Batch mode allows dispensing of a precise amount of fluid, at a specified flow or cycle rate. Each pump can be programmed to perform up to two independent batch sequences, named A and B.
In batch mode, the operator programs the controller to deliver a certain fluid volume through the pump. When the controller determines that it has completed that volume it will automatically stop the pump. The end-of-stroke sensor is able to adapt pump speed to increase fluid delivery accuracy, forcing every stroke to be identical regardless of external conditions.
A simple calibration procedure must be followed so that the controller knows how much volume is transferred per stroke. This technology ensures each and every stroke is exactly the same so that regardless of the environmental conditions of the pump, the total volume of fluid is going to remain constant. ARO’s technology even allows for two separate batch modes per each of the two pumps that are part of the control system.
PROPORTIONAL MODE
Proportional mode allows for an analog input to be used as the pump speed-controlling factor. In this mode, the pump speed will depend proportionally and linearly to the analog input signal. Proportional mode is, in some senses, the opposite of batch mode, in that the emphasis is placed on fluid rate to ensure the designated amount of fluid is delivered in the expected time period. The operator will set the parameters of how an analog input signal relates to the speed of the pump. These parameters are user-set on the controller, allowing for greater flexibility and process automation.
MANUAL MODE
Manual mode is used to run the pump at any specified speed. This is the only run mode in which parameters can be modified outside the password-protected area.
With manual mode, the operator sets the pumps to run at a specific rate. This speed can be adjusted manually via the controller keypad while the pump is running.
SELECT SCREEN DISPLAYS
The ARO Controller features an intuitive user interface. The screen can display up to seven lines of full text, which allows for plenty of information to be clearly conveyed to the user. The different operational modes and information entry screens are conveniently arranged in easy-to-navigate menus. One menu section, where critical programming parameters are to be entered, is password-protected to prevent involuntary changes. For example, the Totalizer Screen displays the number of cycles the pump has executed since the last time this counter was reset.
The Service Interval Screen is used to establish the estimated number of cycles the pump will execute before requiring maintenance; an alarm will be triggered when the service interval is reached.
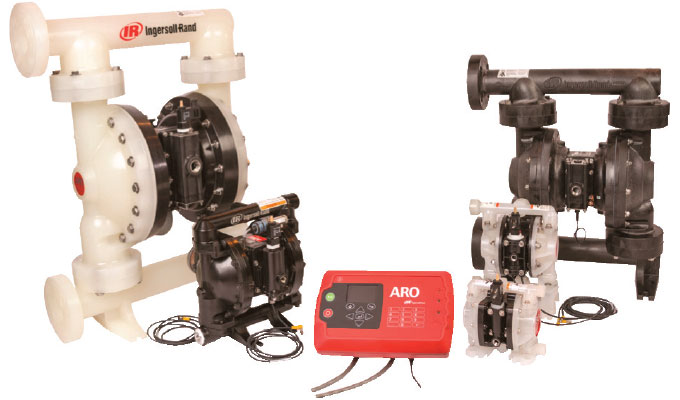
ALARM FUNCTIONALITY
Finally, alarm functionality is built-in to support safety, longevity, reliability and accuracy of the system. When an alarm is triggered, an LED on the controller blinks, an icon appears and a buzzer goes off. Most importantly, there is an electrical contact on the controller that will be closed; that contact can be wired by the user to drive an external alarm—such as a siren or strobe—to readily attract attention when an alarm occurs.
The controller can react to five different external conditions and inform the user that the corresponding condition has occurred. The five different alarm conditions are:
- Lost Prime: The pump has lost its prime and does not pump fluid anymore.
- Leak Detect: Fluid has been detected in either of the two air chambers of the pump.
- Service Needed: The number of cycles programmed as the service interval for the pump has been reached.
- Signal Range: The analog input signal received falls outside the programmed range.
- Max Rate: The cycle or flow rate programmed for the pump cannot be maintained. This can be due to, among others, to excessive back pressure, a cycle rate in excess of the pump’s capabilities, a high fluid viscosity that slows down its flow, or reduced air pressure. Each alarm condition can be configured to either inform the user of its presence only or also to stop the pump.
CALIBRATION
The pump can be calibrated for units other than cycles per minute. If units other than cycles per minute are selected, the pump will have to be calibrated for the desired units, such as gallons per minute or liters per minute.
Upon initial calibration, the operator will select a flow rate required for the process that the pump will serve. The pump will begin running and when the calibrating vessel is full the operator stops the pump and enters the actual volume pumped. The controller internally performs the calculation of the volume per stroke the connected pump delivers.
This procedure assures knowledge of the exact volume per stroke by the controller, regardless of the size of the pump being controlled, and eliminates the need of the operator to perform any manual calculations or the inclusion of compensation factors due to operating conditions; the controller is able to perform all of this internally.
ADVANCED LEAK-DETECTION CAPABILITIES
The ability to detect leaks—preventing equipment damage and production downtime—has historically been a reactive process. Essentially, leaks are dealt with after external symptoms are detected, by which time losses have increased dramatically. Not only can product be lost and equipment severely damaged, but an operator’s health could be put at risk if the fluid leaked is dangerous.
That’s why ARO developed a controller which incorporates advanced leak detection capabilities into a multi-pump controller, allowing the system to self-monitor, therefore reducing the time it takes to react to a fluid leak. Leak-detection sensors are installed on each side of the pump and produce a signal when they detect fluid in the air chamber; the controller is setup to receive these signals and trigger an alarm.
Leak detection functionality can be added to the pump at the time of purchase or easily installed at a later date if deemed necessary.
APPLICATIONS
ARO’s smart touch-and-walk-away system can help optimize costs while controlling multiple pumps—ideal for a wide variety of applications including:
- Tank filling
- Repackaging
- Blending
- Dewatering
- Pipe flushing
- Dispensing
- Fluid Transferring
- Cleaning
- Batching
TARGET INDUSTRIES
From mixing chemicals to cleaning water to combining fluids and beyond, smart, efficient air control systems touch a variety of industries throughout the world, including:
- Chemical processing
- Paint/ink/coatings
- Wastewater treatment
- Agriculture
- Car wash dispensers
- Ceramics
- Electronics
- Dry cleaning
- Nuclear power
- Pet food
- Pharmaceutical
- Printing
- Pulp and paper
- Water treatment
- Steel
CONCLUSION
ARO’s closed-loop control system provides the marketplace with a system that is both easier to use and more economical than previous offerings. The differentiating factors of a touch-and-walk-away pump controller system include closed-loop control, advanced leak detection capabilities, and an end-of-stroke sensor solution that allows greater flexibility and accuracy for the end user.
ARO’s closed-loop system achieves dispensing repeatability within 1 percent and its remote operating capabilities allow for safer monitoring. Additional safety features include remote triggers that can perform auto-shutdowns and send critical operating data and service alerts to operators to notify them of predictive maintenance. These elements work together to increase productivity and reduce downtime, all while positively impacting a company’s bottom line.
FOR MORE INFORMATION
Nelson Wesley is global product leader for diaphragm pumps and Carlos Becerra is a fluid management engineer for Ingersoll Rand/ARO. ARO, an Ingersoll Rand company, is fluid intelligence and a leading worldwide manufacturer of fluid handling products that are expertly engineered to deliver performance and serviceability, enabling our customers to achieve the best total cost of ownership. For more information, visit www.arozone.com.
_______________________________________________________
MODERN PUMPING TODAY, October 2018
Did you enjoy this article?
Subscribe to the FREE Digital Edition of Modern Pumping Today Magazine!
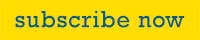