As of late, Hochdorf has been using a Triplex G3F hygienic process diaphragm pump from the experienced pump manufacturer LEWA to pump milk concentrate.
Manufacturers of milk-based food for babies and small children have to uphold the highest purity standards in their products, as well as consistent quality and optimal process safety in the plant. There is significant risk of hygienically unsuitable system components recontaminating the end product. This is why there are strict standards regarding hygiene and material approvals for production systems. For even better compliance with these requirements, Hochdorf Swiss Nutrition AG., a Swiss producer of infant formula and follow-on milk, has acquired a new, hygienic high-pressure pump for conveying the manufactured milk concentrate reliably and safely as well as for metering and further processing precise quantities.
Unlike the plunger pump previously in use, the hermetically sealed diaphragm pump does not require plunger flushing. This substantially lowers the risk of the system recontaminating the end product. The company decided on a Triplex G3F process diaphragm pump in an aseptic design with a collecting pipe and pressure transmitter solution from LEWA GmbH. It is designed for the pressure necessary for spraying the concentrates in the spray tower and also stands out thanks to its hermetically sealed diaphragm pump heads, its high-power drive unit and its low noise emissions. The unit has been in continuous operation without errors since April 2017 and the risk of recontamination has been substantially lowered.
MEETING THE HIGHEST PURITY STANDARDS AND BEYOND
“Due to the high hygiene requirements for the production of food for children and infants, it is necessary to make continuous adjustments to new legal mandates,” explains the plant manager responsible at Hochdorf Swiss Nutrition AG. “This is why it is essential that we coordinate the individual components in our plant to each other perfectly in order to meet the highest purity specifications and, beyond that ensure consistent product quality. Therefore, the references from LEWA about similar hygienically advanced applications were important when deciding on diaphragm pump technology.”
This is especially true for producing special milk powder for infants and small children. To manufacture these products, whole milk, consisting of about 87 percent water, is dehydrated. In this process, the first step is producing a milk concentrate under gentle vacuum conditions. The concentrate is extremely critical with regard to hygiene. The prepared concentrated semi-finished product is then pumped to a clean room for further processing, which is where subsequent drying takes place. This step previously involved using a plunger pump that was not optimally suited for the application due to its design and mode of functioning.
“The need to cool the plungers of the pump with water resulted in a high recontamination risk for the finished product, which cannot be sold and must be disposed of if it becomes contaminated. That is why we were looking for a solution that did the job without plunger flushing,” says the plant manager.
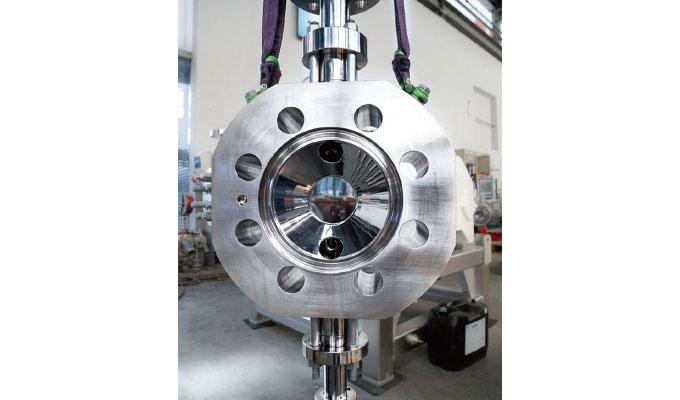
The G3F features a total of three M9 pump heads specifically selected for the aseptic application at Hochdorf. These pump heads feature PTFE sandwich diaphragms, which guarantee both high operating safety and comparably low maintenance effort.
TRIPLEX G3F PROCESS DIAPHRAGM PUMP
The decision was made to purchase a Triplex G3F process diaphragm pump from experienced pump manufacturer LEWA. The Triplex series in the company’s repertoire features pump units that are specifically designed for the high pressures and flow rates of the food and fat-processing industry, meaning that the required throughput of 4,000 l/h at 250 bar was no problem at all. The G3F also features a total of three M9 pump heads specifically selected for the aseptic application at Hochdorf. These pump heads feature PTFE sandwich diaphragms, which guarantee both high operating safety and comparably low maintenance effort. The pump’s hermetic tightness with the corresponding system connection ensures sterile conveyance of the product. All wetted surfaces are made of high-strength DIN 1.4571 (316 Ti) stainless steel and designed with a surface roughness of Ra < 0.5 µm in accordance with the hygiene requirements.
There is a collecting pipe on the suction and discharge side which was provided with a pressure transmitter in an aseptic design at the request of Hochdorf. Both the collecting pipe and flange were designed with a surface roughness of Ra < 0.8 µm for improved cleanability. As a result, maximum operating safety can be ensured in accordance with the required hygienic design specification.
TRIPLEX DRIVE UNIT GUARANTEES HIGH CAPACITY
The basis of the Triplex series from LEWA is the special drive unit: Thanks to its ruggedness, it is suitable for a wide variety of areas in the processing and food industries. The Triplex pump is constructed for continuous operation to ensure long-term operation without interruptions or errors. The drive element housing is designed as a single piece with vertical flange-mounted motor. This design allows the required components, such as bearings and seals, to be reduced to an absolute minimum. The result is a compact and space-saving design that is suitable for the available space in the plant.
The pump is used directly downstream from the heating and homogenization process of the product fluid. The process diaphragm pump then pumps the product to the spray tower, where the final infant or follow-on milk powder is formulated. In addition to compliance with hygiene requirements, another challenge for the LEWA team was adjusting the required cleaning cycles (CIP/ SIP) to the new G3F pump—with stricter compliance rules and a very tight schedule. The employees who were responsible for error-free operation of the unit after installation also had to receive the appropriate training and prepared for future maintenance and repair measures.
Although maximum precision was required in terms of hygiene with significant time pressure at the same time, the cooperation of all those involved in the project went off without a hitch,” says Hochdorf, pleased with the result. After finalizing the project in April 2017, the system was put into operation and has been running up to standard ever since. The hazard posed by recontamination was also lowered substantially.
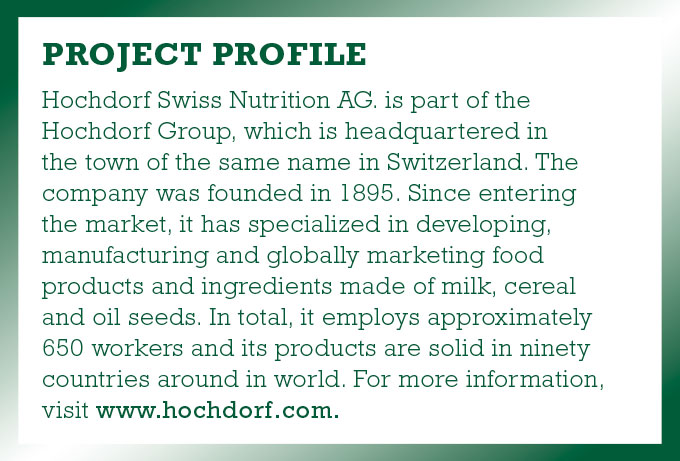
FOR MORE INFORMATION
Pietro Pettoruto is vice director at LEWA Switzerland. LEWA GmbH was founded as a family company by Herbert Ott and Rudolf Schestag in 1952. Today, it is the world’s leading manufacturer of metering pumps and process diaphragm pumps as well as complete metering packages for process engineering. The Leonberg, Germany-based company developed into an international Group within a few decades and saw further improvement in its position on the world market as part of integration into the Japanese Nikkiso Co. Ltd. in 2009. As a research and production-oriented company, LEWA develops technologies and provides solutions for the vast array of applications among its customers. Its products are used mainly in the oil and gas industry, in gas odorization, in refineries and petrochemicals, as well as in the production of plastics, detergents, and cleaners. Additional application areas include the chemical industry, cosmetics industry, pharmaceuticals and biotechnology, food and beverage industry, and energy utilities. LEWA currently employs around 1,200 people and owns fourteen subsidiaries around the world along with having eighty representatives and sales offices in more than eighty countries. For more information, email lewa@lewa.de or visit www.lewa.de.
_______________________________________________________
MODERN PUMPING TODAY, October 2018
Did you enjoy this article?
Subscribe to the FREE Digital Edition of Modern Pumping Today Magazine!
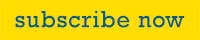