By Del Williams
Industrial facilities can benefit from scheduling corrosion protection of their carbon steel structures and equipment during seasonal slowdowns, when such projects have a minimal impact on output.
However, too often such “scheduling windows” occur during periods of cold, harsh weather, when typical coatings cannot easily be applied.
“For application in low temperatures, you traditionally have to build a container or a tent around the equipment you are corrosion coating and heat it with an electric or propane heater,” says Bryan Stallings, a project manager at Sam Estes Painting Company, an industrial painting contractor based in Owensboro, Kentucky. “Failing that, the coating won’t set and the cold weather will shock it, so it will peel off or crack.”
Fortunately, to extend the service life of industrial facilities with carbon steel assets, facility managers are turning to a new category of tough, chemically bonded phosphate ceramic (CBPC) coatings that can stop corrosion, ease application, and reduce production downtime even in below freezing temperatures.
RAPID WINTER CORROSION PROTECTION
When an aluminum recycling plant in Kentucky recently required a lengthy conveyor belt corrosion coated in four sections, one challenge was coating it in winter weather. The conveyor belt was an integral part of the recycling plant’s process of converting aluminum scrap into reusable aluminum.
“Without heated containment, you might wait indefinitely for the right weather conditions to proceed,” says Stallings. “Some traditional coatings stop curing if it’s not 40 degrees Fahrenheit (4.4 degrees Celsius) or above, so that’s a big problem. For proper application, you usually have to keep coatings several degrees above dew point for hours or days.”
Another challenge involved the way traditional polymer paints and rubber type coatings have been used as physical barriers to keep corrosion promoters such as water and oxygen away from steel substrates. This works until the paint is scratched, chipped, or breached and corrosion promoters enter the gap between the substrate and coating. Then the coating can act like a greenhouse—trapping the corrosion promoters—that allows the corrosion to spread under the coating.
“With typical coatings, once they chip or break off, corrosion can spread under the coating so you might not be aware of it,” says Stallings. “That happens a lot. That’s when steel equipment or structures get eaten away.”
To address such issues, the aluminum recycling plant and Stallings turned to EonCoat, a spray applied inorganic coating from the Raleigh, North Carolina, based company of the same name. EonCoat represents a new category of rugged, chemically bonded phosphate ceramics (CBPCs) with unique properties.
In contrast to traditional polymer coatings that sit on top of the substrate, the corrosion resistant CBPC coating bonds through a chemical reaction with the substrate, and slight surface oxidation actually improves the reaction. An alloy layer is formed. This makes it impossible for corrosion promoters like oxygen and humidity to get behind the coating the way they can with ordinary paints.
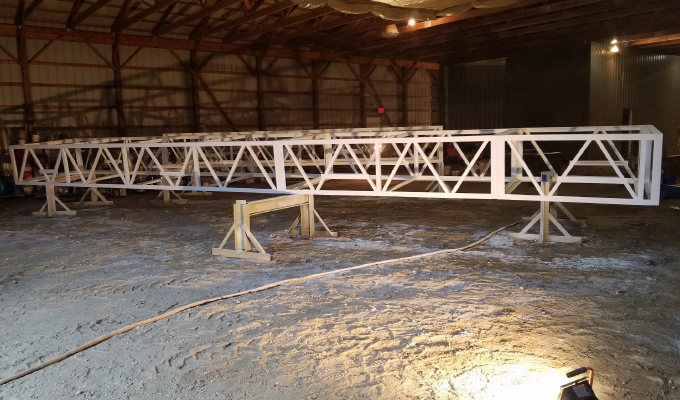
STOPPING CORROSION
Although traditional polymer coatings mechanically bond to substrates that have been extensively prepared, if gouged, moisture and oxygen will migrate under the coating’s film from all sides of the gouge.
By contrast, the same damage to the ceramic-coated substrate will not spread corrosion in industrial infrastructure because the carbon steel’s surface is turned into an alloy of stable oxides. Once the steel’s surface is stable (the way noble metals like gold and silver are stable) it will no longer react with the environment and cannot corrode.
Visible in scanning electron microscope photography, EonCoat does not leave a gap between the steel and the coating because the bond is chemical rather than mechanical. Since there is no gap, even if moisture was to get through to the steel due to a gouge, there is nowhere for the moisture to travel, which effectively stops corrosion in industrial applications.
The corrosion barrier is also covered by a ceramic layer that resists corrosion, water, impact, abrasion, and chemicals as well as fire and temperatures up to 842 degrees Fahrenheit (450 degrees Celsius).
For such durable corrosion protection, Sam Estes Painting Company successfully sprayed EonCoat’s cold weather formulation on the aluminum recycling plant’s conveyor belt sections. This was done at a below freezing temperature.
“We were able to spray at 30 degrees Fahrenheit (-1 degrees Celsius) without needing to use a containment tent or wait for warmer conditions,” says Stallings.
Industrial operation managers or corrosion engineers looking to reduce costs are also finding additional advantages to CBPC coatings like EonCoat beyond corrosion resistance.
SAVING TIME AND MONEY
Such coatings consist of two non-hazardous components that do not interact until applied by a standard industrial plural spray system like those commonly used to apply polyurethane foam or polyurea coatings. Since CBPC coatings are inorganic and non-toxic, there are no VOCs, no HAPs, and no odor. This means the water soluble, non-flammable coatings can be applied safely even in confined spaces, or when adjacent parts of a plant continue to operate.
One of the greatest benefits, however, is quick return to service that minimizes facility downtime. The time saved on anti-corrosion coating projects comes both from simplified surface preparation and expedited curing time. With a typical industrial coating, near white metal blast cleaning (NACE 2 / SSPC-SP 10) is required to prepare the surface. But with the ceramic coating, only a NACE 3 / SSPC-SP 6 commercial blast cleaning is typically necessary.
With traditional coatings, extensive surface preparation is required and done a little at a time to avoid surface oxidation, commonly known as flash rust, which can require re-blasting.
However, with the CBPC coating, the flash rust is no issue. There is no need to hold the blast. The reason for this unique CBPC characteristic is due to the presence of iron in the rust, which helps to create the magnesium iron phosphate alloy layer. It is this alloy layer that allows CBPCs to so effectively protect carbon steel from corrosion.
“The preparation was easy,” says Stallings. “We were able to blast it once and leave the tightly adhered rust in place. It rained once, but we didn’t have to re-blast it so it helped quite a bit.”
For traditional three-part system coatings utilizing polyurethanes or epoxies, the cure time may also be days or weeks before the next coat can be applied, depending on the product.
SUCCESS WITH CERAMIC COATING
In contrast, a corrosion resistant coating for carbon steel, utilizing the ceramic coating in a single coat, requires almost no curing time.
Stallings, in fact, was able to spray the aluminum plant conveyor sections with a 331 tip to the recommended thickness of 25 mils in a single application with no runs. A half hour after application, the coating was hard enough to move the conveyor sections back into place.
“Altogether, we saved at least a week of application time with the ceramic coating,” concludes Stallings. “Without containment and with only minimal surface preparation, we were able to spray an effective single coat instead of the usual three coats. This is the way to go for industrial plant managers needing reliable corrosion coating protection applied in cold weather.”
FOR MORE INFORMATION
Siemens Digital Industries Software, a business unit of Siemens Digital Industries, is a leading global provider of software solutions to drive the digital transformation of industry, creating new opportunities for manufacturers to realize innovation. With headquarters in Plano, Texas, and over 140,000 customers worldwide, we work with companies of all sizes to transform the way ideas come to life, the way products are realized, and the way products and assets in operation are used and understood. For more information, visit www.sw.siemens.com.
Del Williams is a technical writer based in Torrence, California. EonCoat is focused on preventing corrosion on a wide scale, and the company only works with corporations of significant size, often those that are publicly traded with multinational operations. For more information, call 754.222.4919 or visit www.eoncoat.com.
MODERN PUMPING TODAY, October 2019
Did you enjoy this article?
Subscribe to the FREE Digital Edition of Modern Pumping Today Magazine!
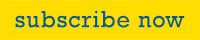