As many manufacturers know, chemicals used throughout product development and production are often purchased in large 55-gallon drums. Spills or other accidents occur when employees try to dispense the chemicals from these unmanageable containers, either manually or with large machinery.
For High Point-based Carolina Casting, a leader in polyester resin products for the furniture industry, a large quantity of acetone is used daily, which requires dispensing the liquid from a 350-pound drum several times throughout the day.
Carolina Castings creates bunn feet, finials, moldings, and roto-casted table bases to include on items such as chair backs, ornate fixtures, tabletops, mirror frames, and highly complex assembled table bases and pedestals. Recent products include upscale hotel corridor corner guards, lamp bases and chandeliers, statuettes, decorative mailbox trim, outdoor dining tables and bases, as well as items such as specialty kitchen and bath tiles.
Carolina Casting uses acetone to clean hand tools, small containers, and for machine flushing operations, with the primary use being to clean all finished products of chemical components, flashing, and foreign debris.
Previously, dispensing acetone for the resin manufacturer was a slow, labor intensive, and wasteful process with large amounts of acetone being lost from spills.
Typically, the manufacturer would move the large heavy container to another location, place it on a cradle in a prone position, attach bonding and grounding wires, and then tip it to dispense the acetone through a hand-controlled faucet. Then the entire process would be reversed to return the 350-pound drum of acetone to the chemical storage room.
The manufacturer also tried rotary hand crank pumps. However, these offered no flow control and created more spills.
After determining other cost-prohibitive options were not feasible, Carolina Casting found a safer, easier-to-use, cost effective dispensing option called GoatThroat Pumps, by the Milford, Connecticut, based manufacturer of high-quality chemical transfer equipment of the same name.
With a spring-actuated flow valve, these pressure action pumps function like a beer tap for chemicals, allowing workers to maintain absolute control when handling the chemicals, and allows the large container to remain in a safe and upright position.
The operator attaches the pump, presses the plunger several times to build up a low amount of internal pressure, and then dispenses the liquid. The tap is configured to provide precise control over the fluid delivery, from slow (1 ounce) up to 4.5 gallons per minute, depending on viscosity.
Because such pumps use very low pressure (<6 PSI) to transfer fluids through the line and contain automatic pressure relief valves, they are safe to use with virtually any container.
The pumps are safe for use with more than 1,700 liquids, including the most aggressive acids, flammables and solvents used in manufacturing.
Using the pumps to transfer the acetone from drums proved to be efficient and provided more precision to Carolina Casting’s daily process. After a month, they added the BGA pneumatic device to eliminate pumping by hand.
Carolina Casting Plant Engineer Dan Stiles commented about the improved efficiency and safety of using GoatThroat Pumps, which exceeded compliance requirements.
“At a rate of four gallons a minute, it takes one person about twelve minutes to fill the 40-gallon tank,” says Stiles. “No more carrying buckets of acetone across the factory, which consumed the better part of thirty minutes and could hurt the employee’s back. We have replaced o-rings a couple of times, but the original pumps are still in use after four years.”
“The new procedure is faster, safer, and has helped us exceed our environmental compliance requirements,” concludes Stiles.
FOR MORE INFORMATION
GoatThroat is a global technology leader that makes corrosive chemical handling more efficient, reliable, safe, and sustainable. For more information, call 866.639.4628, email info@goatthroat.com, or visit www.goatthroat.com.
MODERN PUMPING TODAY, March 2020
Did you enjoy this article?
Subscribe to the FREE Digital Edition of Modern Pumping Today Magazine!
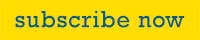