By Mila Darling, Datum Electronics
Power plants use a wide range of pumps for multiple operations. These include primary pump systems, such as boiler feed pumps and cooling water pumps, as well as auxiliary pump systems, such as fuel transfer pumps, slurry pumps, lubrication pumps, and chemical feed pumps.
THE BACKGROUND
Unsurprisingly, primary pumps, including boiler feed and water cooling pumps are critical to a plant’s efficiency, availability and profitability. They are costly to manufacture, operate and maintain, however, create more potential for significant maintenance savings, as well as reduction in energy and operating expenses, therefore optimising their efficiency is critical to achieving increased plant efficiency.
Pump failures can jeopardize the entire operational efficiency of a plant in the form of unscheduled repairs, costly downtime, or even an injury. Rather than being caught off-guard, power plant operators are tasked to move from complete maintenance routines toward a more predictable processes and increased system efficiencies.
THE CLIENT
Our client is a world-leading pump manufacturer, serving mining, oil and gas, and general industrial markets in over fifty countries worldwide. For the past 150 years, the company has been focusing on making its customers’ operations safer, more efficient, and more sustainable, by producing a range of integrated pump solutions for high wear applications at near the optimum efficiency point.
THE CHALLENGE
For this specific project, the team was looking to measure and monitor power and torque on three pumping systems, which they were developing for a customer. They already had received a quote from a torque measurement specialist, however, due to the necessary adaption of the existing flanges on the drive line, their budget would only accommodate a single inline torque transducer. This would mean the team would be able to monitor one of the three pumps at a time and then move the measuring system every three months, which was far from ideal.
As a result, the team decided to explore other options available on the market. Datum Electronics, well known for making bespoke and OEM torque measurement solutions, was approached to provide an alternative quotation. Using their thirty years of experience, Datum Electronics can guide potential customers through the specification process and deliver the optimum torque sensing solution for a specific customer’s application.
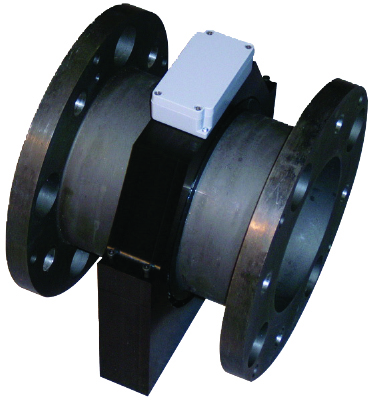
THE SOLUTION
After looking at project specifications, Datum Electronics were able to offer a very cost-effective solution, which allowed monitoring all three pumping systems simultaneously, as required by the customer. Using the latest innovative technology, The Datum team converted the existing coupling spacers into torque sensors, which negated the need for costly flange adjustment. The coupling spacers had the pre-requisites of a torque sensor: (1) a good quality steel 4340; (2) a simple length of the shaft (in this case a tube).
Subsequently, the coupling spacers were free issued to Datum, where they were adapted with a tailored set of Series 425 strain gauge instrumentation. The coupling spacers were calibrated by the Datum team, showing linearity better than 0.1 percent and a non-repeatability of better than 0.05 percent.
THE IMPACT
Using the existing spacers facilitated the customer to save on unnecessary modifications to the drive line, as well as potential issues with balancing and misalignment. It also removed the need for new couplings and costly flange adaptations, required to fit the standard torque sensor.
The bespoke torque sensor solution, offered by Datum, enabled the customer to purchase and fit three torque sensing solutions and conduct permanent monitoring on heavy duty pumps for a lower cost, than fitting a competitor’s single standard torque sensor.
Therefore, the custom torque sensor from Datum Electronics enabled the pump manufacturer to deliver the best available pump to their customer, minimizing operation costs, simplifying maintenance and increasing the plant availability for the foreseeable future.
FOR MORE INFORMATION
Datum Electronics develops, produces and sells innovative torque and shaft power measurement solutions, such as shaft torque sensors, torque transducers, torque meters, marine shaft power meters, bolt-on strain gauge sensors, amplifiers, power take off (PTO) shaft sensors, and wind turbine monitoring systems. For more information, visit www.datum-electronics.co.uk.
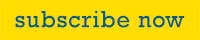
MODERN PUMPING TODAY, December 2019
Did you enjoy this article?
Subscribe to the FREE Digital Edition of Modern Pumping Today Magazine!