By Peter Sucharda, Devine & Associates, and Mark Gimson, Cla-Val Company
Determining the optimal run time of the stagnation valve depends on a few parameters that can vary from one location to another. Dave Alberton, manager of water distribution and wastewater collection for Hamilton Water, points out, “Our engineering firm created a spreadsheet to determine how long the anti-stagnation valves need to open for. By entering in the diameter of the pipe that the normally-closed boundary valve is connected to, and the distance to the nearest piping intersection, upstream or downstream of the isolation valve (whichever is longer), the program calculates the total volume of potentially stagnant water on one side of the boundary valve. Then we input the upper zone and lower zone pressures which are normally constant. And lastly, we can ‘play’ with the size of the anti-stagnation valve—trying different sizes to see what is the most suitable for the application.”
The program takes the valve’s size, converts that to its Cv and can then calculate the flow through the valve using the equation Q (flow) = Cv * square root of the Dp across the valve. The volume divided by the flow rate gives the city the time required to flow the entire volume of stagnant water through the valve.
BATTERY USE AND RELIABILITY
To meet the need for high demand and reliability without fail, the latching solenoid is a high-quality unit, and the entire valve, including the solenoid, is rated to 232 psi. It can range in size from 1/2 to 4 inches, but most common is the 3/4 inch. The unit runs off a long life 9-volt lithium battery and the whole assembly is IP-68 submersible which is important to have in a valve chamber where flooding can happen. The battery is rated for three years of service, but the city prefers to err on the side of caution and replace the batteries every year during regular maintenance checks to ensure the valves are working properly and continue to do so.
“In the worst case, if the battery runs out of power, the valve will cease to function but is designed to fail in the closed position. The unit will retain its program so that, when a fresh battery is installed, the program does not have to be re-entered. When connected to a computer the unit will synch to its date,” says Alberton.
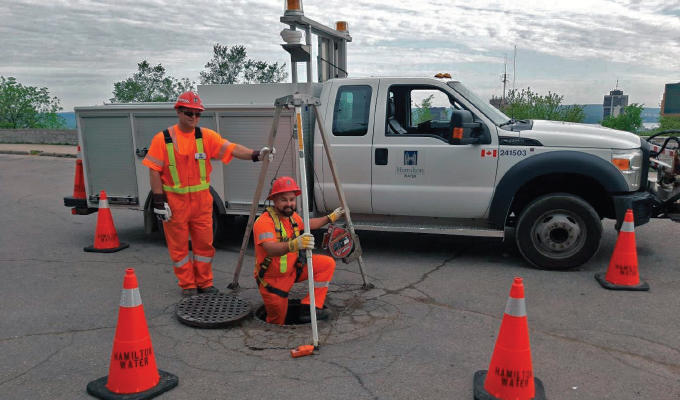
SAVINGS ACROSS THE BOARD
The pilot project focused on thirty-seven water distribution level valves and open bypass lines that separate the two pressure districts. The previous one-year historic pumping station electrical demand (kW) and energy consumption (kWh) were used as a baseline for the pilot project.
The post-retrofit period is being continuously monitored using the city of Hamilton’s Office of Energy Initiatives to gather electrical demand (kW) and energy consumption (kWh) data to verify actual project energy savings and electrical demand reduction.
Based on the product calculations, it was estimated that each valve would save 44,000 kWh of energy, or 1,628,000 kWh per year in total for thirty-seven valves. This was based on a 185-kW reduction in electrical demand and a 24/7 process operation. However, the valve timers were set for fifteen minutes, which is shorter than the original time used to estimate savings, so the actual energy savings were even greater.
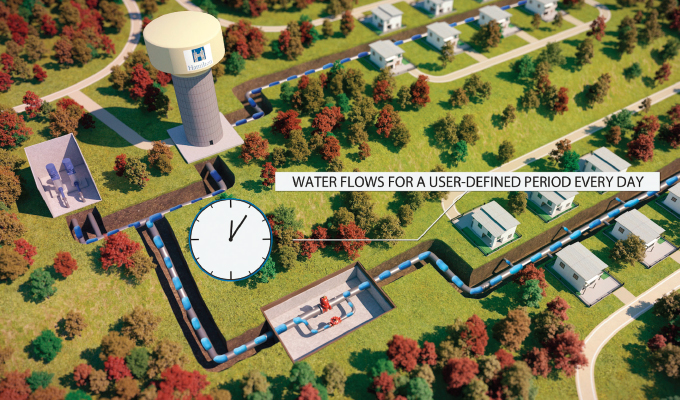
Energy Savings
The graph shows the flow before and after the anti-stagnation valve installation. The actual results of the pilot study were a monthly savings of 258,515 kWh which equates to a reduction 3,102,180 kWh per year of energy use. This translates into an annual coast savings of CDN $199,637 for the pilot project. With a total installed project cost of under CDN $90,000, the simple payback is under five months for this technology.
Water Savings
Using anti-stagnation valves has enabled the city to eliminate stagnant water concerns and reduce water consumption. The valves are programmed to open at staggered times in order to minimize impact to the system. By flowing during the daytime, when there is normal demand, these valves can reduce and even eliminate over-pressurization in the lower system. As they flow for shorter periods of time there is less wear and tear to the chamber piping, significantly reducing breaks down the 3/4-inch line elbows and fittings that occur due to high velocity flow and cavitation issues. Since the pilot project watermain breaks have decreased by 15 percent resulting in a reduction of non-revenue water loss.
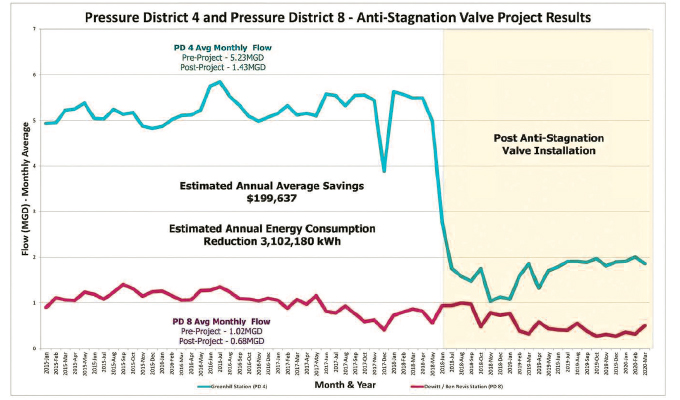
Equipment Savings
By reducing flow, the city will also reduce equipment costs associated with delivering that water in three key areas.
- Annual Maintenance:As pump usage is reduced by 50 percent, maintenance costs should decrease by 50 percent (based on running time).
- Pump Replacement Costs: With 50 percent reduction in operation, each pump’s life expectancy will double. Therefore, replacement cost will drop by half on a yearly basis.
- New Station Costs: If the original plan were to use four pumps but now only two are required, new station costs will decrease significantly. With a reduced number of pumps, station size decreases as does its complexity since the station will require less valves and associated piping.
The pilot project (Phase 1) has clearly demonstrated that incredibly significant energy savings and water reduction for the city of Hamilton is achievable using the anti-stagnation valve technology in its pressure district zones.
“We have a culture of continuous improvement at Hamilton Water, so with such a positive ROI and reduction on energy consumption we are now in the process of rolling out two more phases. Phase 2 will involve the installation of an additional thirty-seven valves, providing an energy savings estimated at 445,000 kWh per year … Phase 3 will see the installation of a further 36 valves, estimated to reduce energy consumption by 400,000 kWh per year,” adds Alberton.
THE TIME IS NOW
The city of Hamilton is well on its way to improving operational practices that reduce carbon emissions with the end game of 60 percent reduction in emissions by 2050.
“Every effort counts when it comes to saving the planet for our future generations. I encourage all municipalities to step up to the challenge—the technology is there, it’s up to us to implement it,” concludes Alberton.
FOR MORE INFORMATION
Peter Sucharda, P.Eng., is president of Devine & Associates, which works with end users, consultants, and contractors to design, produce, implement, and support flow solutions for water, wastewater, storm water, slurry, and other fluid applications. He can be reached at psucharda@devineassoc.com. Mark Gimson is director of marketing and international sales for Cla-Val Company and can be reached at mgimson@cla-val.com. Cla-Val is a world-leading designer and manufacturer of automatic control valves. From reducing and relief valves to deluge, air valves and more, Cla-Val manufactures and provides a wide variety of solutions for use in some of the world’s most demanding applications. For more information, visit www.cla-val.com.
MODERN PUMPING TODAY, September 2021
Did you enjoy this article?
Subscribe to the FREE Digital Edition of Modern Pumping Today Magazine!
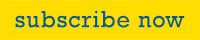