Cooling towers are an attractive method to provide cooling water to power plants and other process cooling applications. The use of cooling towers versus once-through cooling significantly reduces the amount of water drawn from rivers and lakes, which is particularly important in many regions in the Western United States, where water availability is a problem. Cooling towers also eliminate thermal pollution due to cooling water discharges into and greatly reduce the amount of water withdrawn from natural bodies of water.
COOLING TOWER CHALLENGES
Despite these advantages, cooling towers provide special challenges with regard to the design of cooling water pump intake structures. These challenges must be addressed to ensure a reliable flow of cooling water with a minimum expenditure of power in order to maximize the plant capacity and efficiency. Design factors such as design footprint, civil constraints, increases in plant capacity requiring increased cooling flow, and off-design operation can all affect the flow hydraulics and therefore negatively affect the performance of the intake pumps.
Cooling towers are increasingly being used to provide cooling water to power plants. These structures are able to conserve the use of water, and minimize potential environmental impact caused by the use of once through cooling.
COOLING TOWER ISSUES AND PUMPING
At the base of the cooling towers a pump intake structure is constructed to convey the flow from the tower to the power plant. These structures are designed to provide acceptable approach flow patterns to the pumps, free of adverse hydraulic problems such as unacceptable free surface and subsurface vortices, pre-swirl at the pump bell entrance, and air entrainment. The Hydraulic Institute Standards (HIS) provides acceptance criteria as regards to the flow entering pumps, and gives general guidelines for the dimensions and layout of pump intakes (see “American National Standard for Rotodynamic Pumps for Pump Intake Design,” ANSI/HI 9.8-2012). However, due to space constraints and limited submergences to pumps, it may not be possible to satisfy all HIS requirements. Hydraulic (physical) model studies are required in such cases to evaluate the hydraulic performance and to derive remedial modifications as needed.
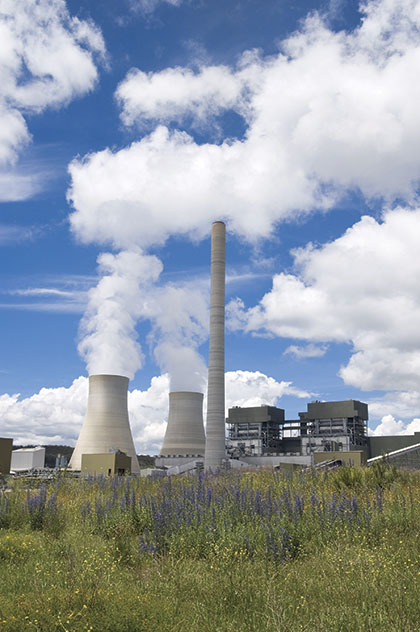
Typically, a hydraulic model study would include 1) observation and documentation of flow patterns approaching the pump bays and within the pump bays, 2) observation and documentation of the location, strength and frequency of any free surface and subsurface vortices present, 3) measurement of swirl within the pump bell or in the suction pipe to evaluate any pre-rotation present in the flow approaching the impeller, and 4) measurement of velocity distribution within the pump bell or in the suction pipe to evaluate the axial velocity profile of the flow approaching the impeller. Acceptance criteria for vortices, swirl, and velocity distribution are available in HIS. Further, the HIS has a list of criteria for which a physical hydraulic model study is required, in order to assure that the guidelines for satisfactory hydraulic performance are met. A hydraulic model study may also provide for solutions to flow patterns that may not directly impact the pumps but have a negative impact on the operation of the station such as flow separations and air entrainment due to reasons other than vortices.
Based on several hydraulic model studies, the issues that are of special concern in the design of cooling tower pump intakes are discussed. Some recommendations as to how to avoid these problems are also explored.
A LOOK AHEAD
In this series, general hydraulic design guidelines and performance acceptance criteria for pump intakes based on Hydraulic Institute Standards are outlined. Case studies from physical model studies of cooling water pump intakes are presented, which may provide insight into likely problems and design flaws that engineers should be aware of while designing cooling tower pump intake structures. Examples of measures to avoid or remedy the commonly-encountered hydraulic problems derived from hydraulic model studies are discussed.
For More Information
Founded in 1894, Alden is the oldest continuously operating hydraulic laboratory in the United States and one of the oldest in the world. Alden has been a recognized leader in the field of fluid dynamics research and development with a focus on the energy and environmental industries. For more information, visit www.aldenlab.com.
____________________________________________
MODERN PUMPING TODAY, January 2017
Did you enjoy this article?
Subscribe to the FREE Digital Edition of Modern Pumping Today Magazine!
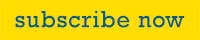