In the late nineteenth century, Olin J. Garlock devised a better way to seal piston rods in steam engines. Since then sealing materials have been developed for various industrial applications. Over the years, different manufacturing processes such as calendering and beater addition have improved the performance of fiber sheet gaskets for these applications; however, design concepts for their formulation remain similar regardless of manufacturing method.
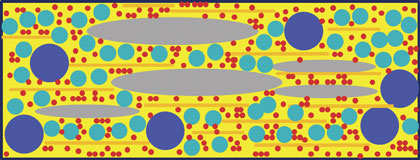
Figure 1: Microstructure of a compressed fiber sheet material ingredients: silicates [gray]—laminated structure; mineral [blue and aqua]—irregular/spherical shape; fiber [orange]—fibrillated, cylindrical or curly; silica, carbon black, or fine filler [red]—spherical shape; elastomer binder [yellow].
OVERVIEW OF MATERIALS
Many of the applications for compressed fiber sheet gaskets involve elevated temperatures and/or high pressure, which require high bolt loading in flanged joint assemblies. Various materials are added to the fiber-binder matrix to sustain this high compressive loading. To provide strength, different types of fibers such as p-aramid (Kevlar™), cellulose, polyester, glass fiber, carbon fiber, and others are added. Some of these fibers are organic materials, which limits their use at elevated temperatures. Minerals in cylindrical form provide balance in the formulation due to their high-temperature stability and strength. To form a compact structure, materials of different sizes are used, including silica, carbon black, and other micro-sized fillers. Figure 1 illustrates the ingredients and microstructure of a compressed fiber sheet material.
Finally, an elastomer, or rubber, is used to fill the interstices between these ingredients and bind them together. The binder used depends upon the application. For example, nitrile rubber is more chemically resistant to fluids such as oil and gasoline, whereas chloroprene is a better option for many of the newer refrigerants.

Table 1: Refrigerant resistance of chloroprene and nitrile gaskets
REFRIGERANT APPLICATIONS
Historically we have recommended a gasket with a nitrile rubber binder (Style 3000) for sealing refrigerants. This gasket provides satisfactory performance, even though gaskets with chloroprene binders are the preferred choice for these applications. Table 1 compares the refrigerant resistance of chloroprene and nitrile gaskets; note the superior suitability of chloroprene gaskets for most refrigerants.
Despite their superior resistance to a broader spectrum of refrigerants, the balance of materials in the formulation of chloroprene gaskets has made it more difficult to manufacture tight-sealing gaskets than using nitrile binders.
To resolve this issue, the chloroprene gaskets underwent a process of continuous improvement that resulted in an advanced formulation (Style 3300) to provide better sealing performance. This process began with a root cause analysis that identified the gasket material itself as a leak path (figure 2).
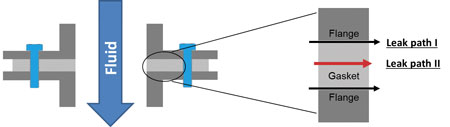
Figure 2: Potential leak paths of a flanged joint: I flange-gasket interface and II micro channels in gasket material.
Next, a series of engineering formulation designs were created and subjected to precise laboratory tests and statistical analysis. In air conditioning applications, the refrigerants transition back and forth between liquid and vapor phases to remove heat from the system. Therefore, leakage tests were conducted in both nitrogen (gas) and Fuel A (liquid), to assess sealing capability. Figure 3 depicts formulation progress in reducing leakage.
The well designed formulations performed at 0.1 milliliters per hour, the minimum measurable leakage on the test device. Further engineering work finalized the optimal formulation to provide the best sealing performance. The result is a gasket that seals as tightly as a nitrile gasket (Style 3000), while maintaining the properties of the chloroprene gasket (Style 3300).
A proprietary p-aramid reinforced composite material with harmonic composition balance, the new formulation (Style 3300) is produced through an optimized calendaring process that provides consistent quality and maximized performance in refrigerant applications. Significantly it contains environmentally friendly materials that comply with the European Union’s REACH regulation protecting human health and the environment from risks posed by chemicals. In addition, it is produced using a proprietary solvent that is exempt from EPA restrictions on volatile organic compounds and a solvent recovery system that captures emissions and recycles them back into the production process.
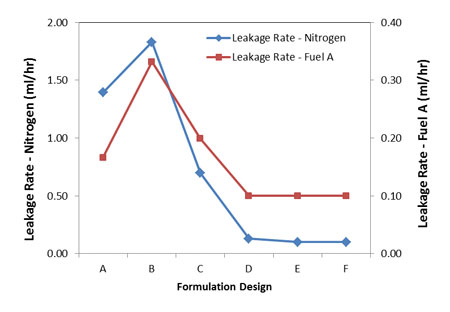
Figure 3: Iterative formulation designs of chloroprene gaskets and corresponding sealing performance.
GASKETS: A VITAL ROLE TO PLAY
Gaskets play a relatively small role in an air conditioning or chiller system, but their function extends beyond merely sealing a joint to reliability, safety, and environmental concerns. Developing new gasket material formulations or improving existing ones is challenging, but it makes our industries cleaner and safer and our environment healthier.
For More Information
Ming-Hang Yang is a material engineer at Garlock Sealing Technologies. He has worked on material development for fiber gaskets, expansion joints and mechanical oil seals. Prior to Garlock he worked as an R&D engineer for a semiconductor manufacturer. He is a graduate of the University of Akron where he studied rubber/ polymer composites, reinforcement, and fracture science. He can be contacted at ming-hang.yang@garlock.com. Dave Burgess is a senior gasket application engineer with Garlock Sealing Technologies. Working with rubber, fiber, PTFE and metal gasket materials, he makes recommendations and assists with gasket selection and trouble-shooting. He also represents Garlock on the ASTM F3 Gasket Committee. He can be contacted at dave.burgess@garlock.com For more information, visit www.garlock.com or call 800.448.6688.
____________________________________________
MODERN PUMPING TODAY, January 2017
Did you enjoy this article?
Subscribe to the FREE Digital Edition of Modern Pumping Today Magazine!
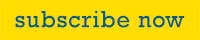